Product 1: Peristaltic Pump it Up
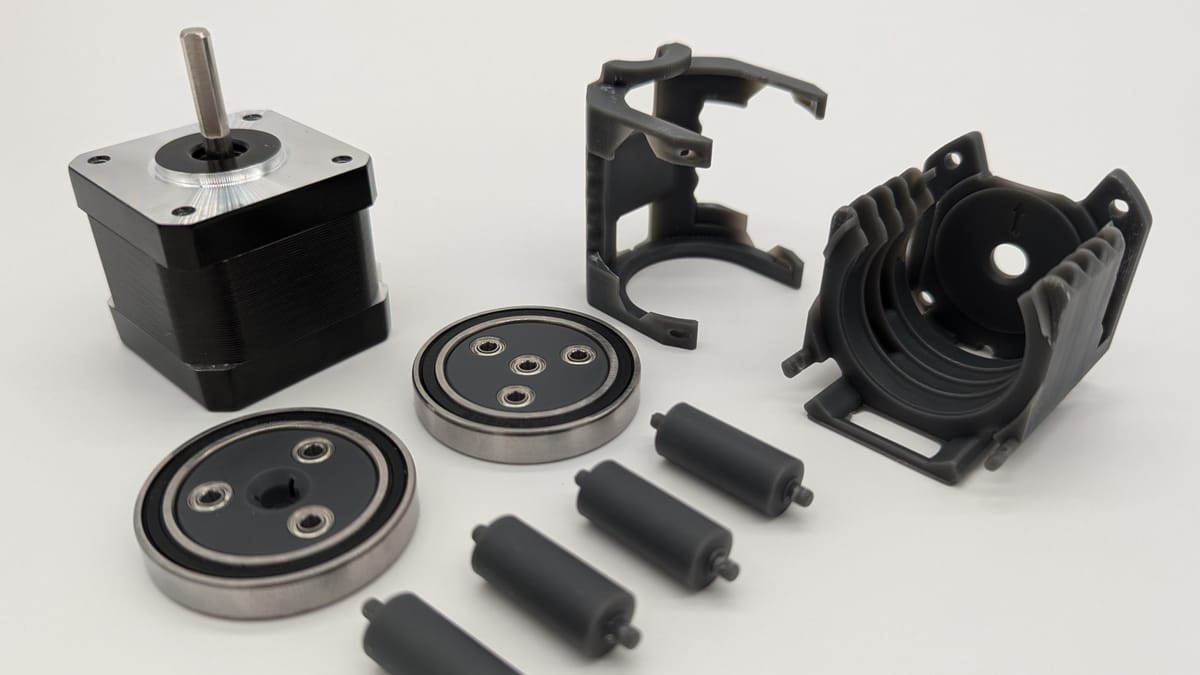
I present the PrecisionFlow 1743!
My first product launch this year is a programable 0-136mL/min flowrate peristaltic pump compatible with NEMA17 stepper motors. Reach out to Sales@JoshAdams.io for full details, pricing and customization options!
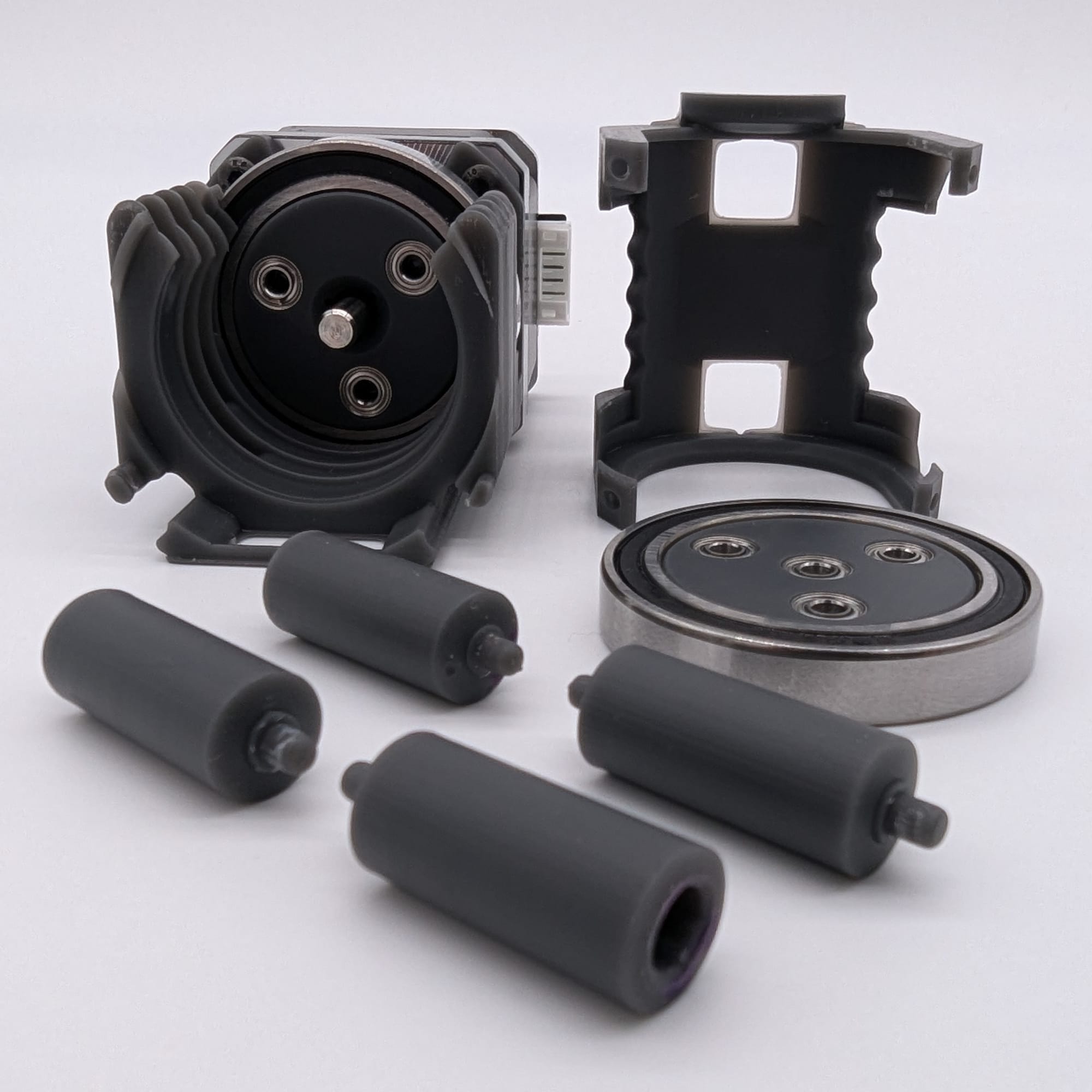
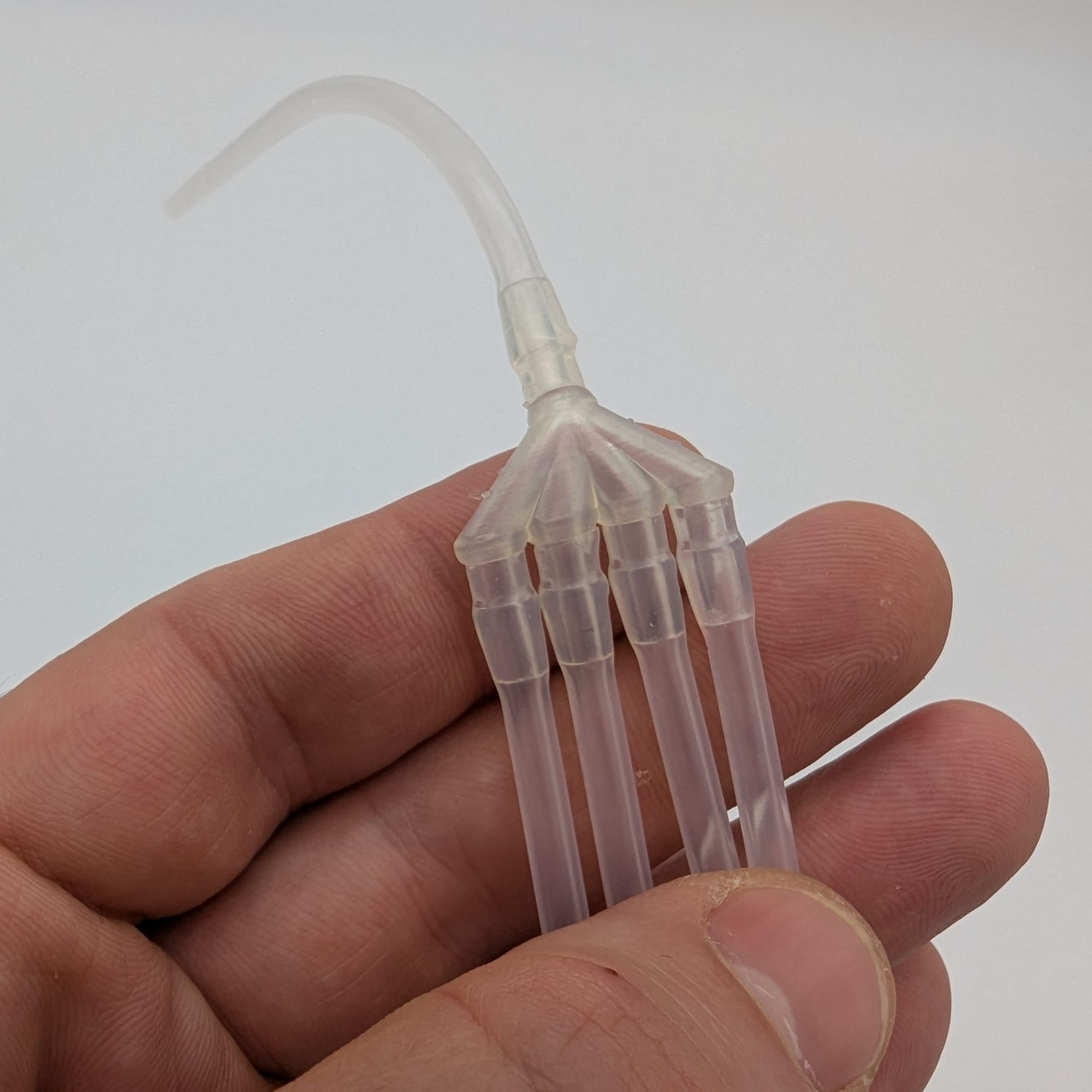
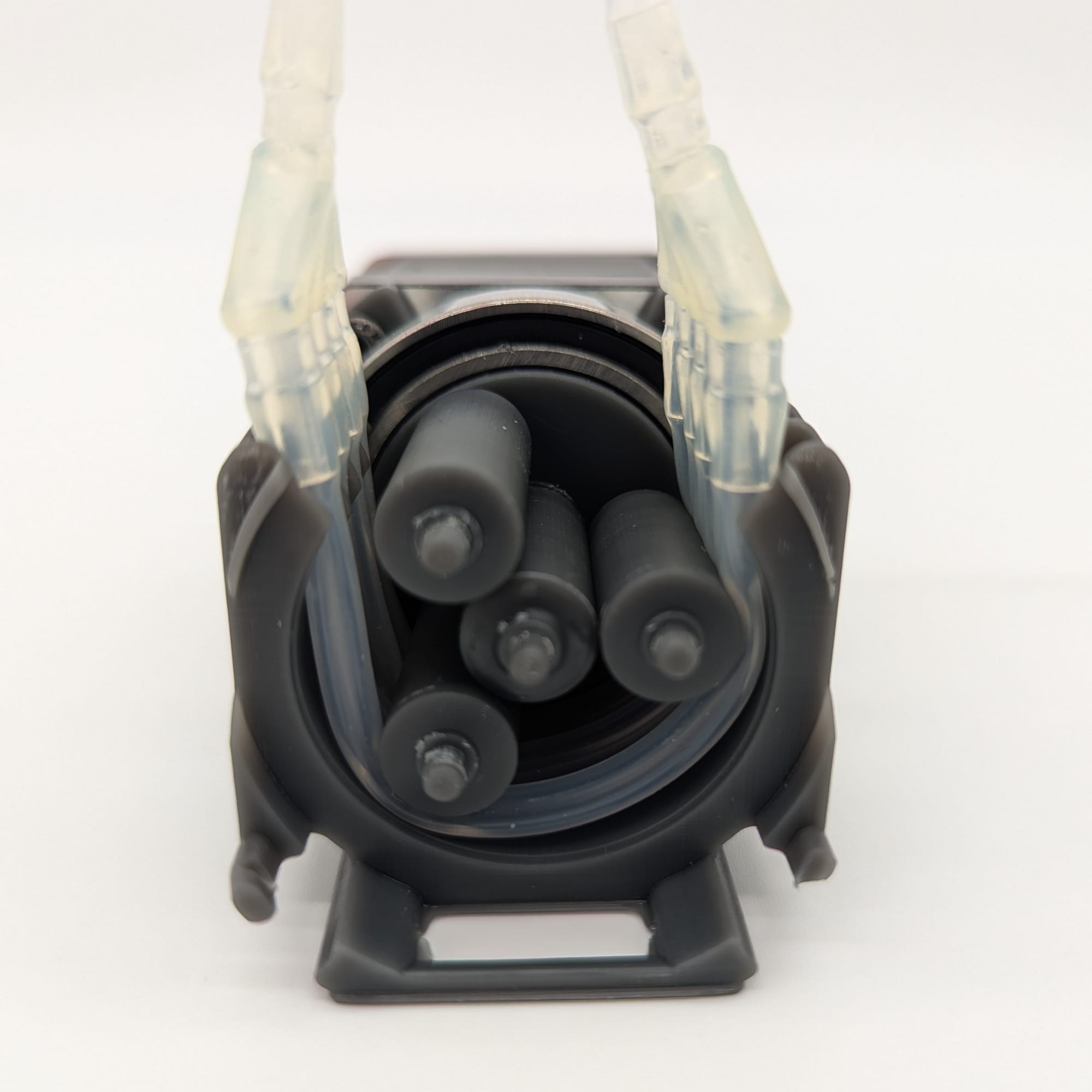
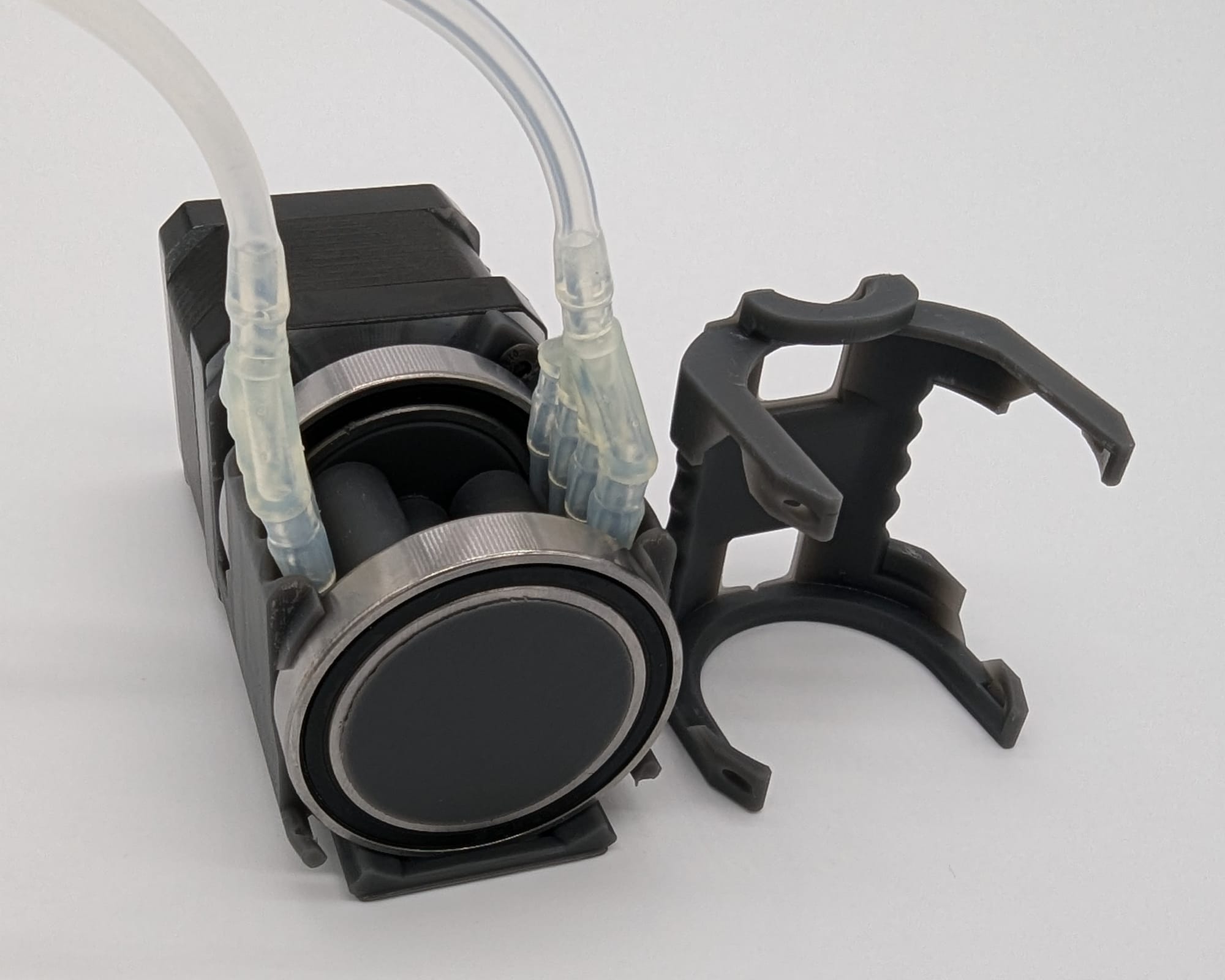
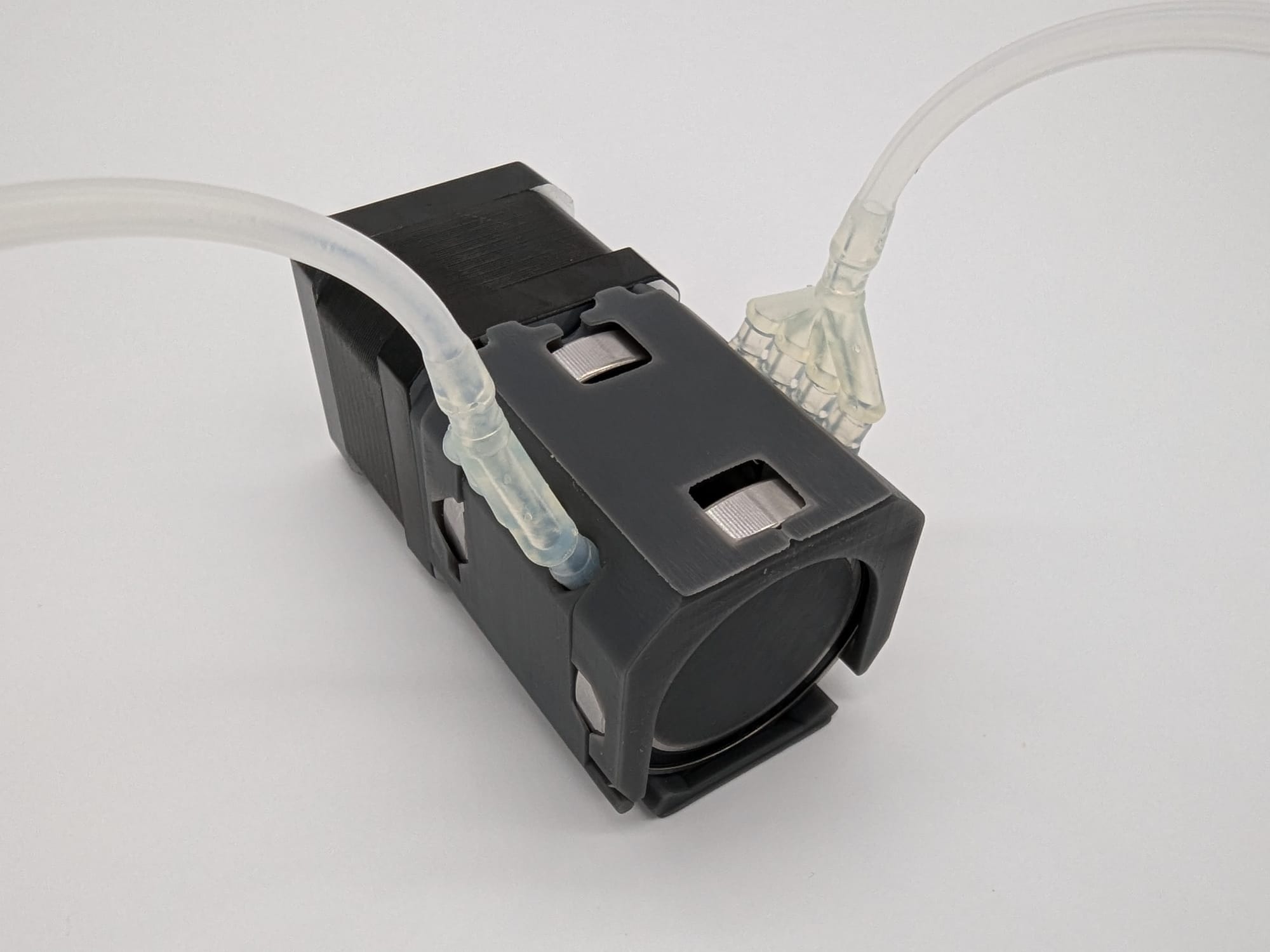
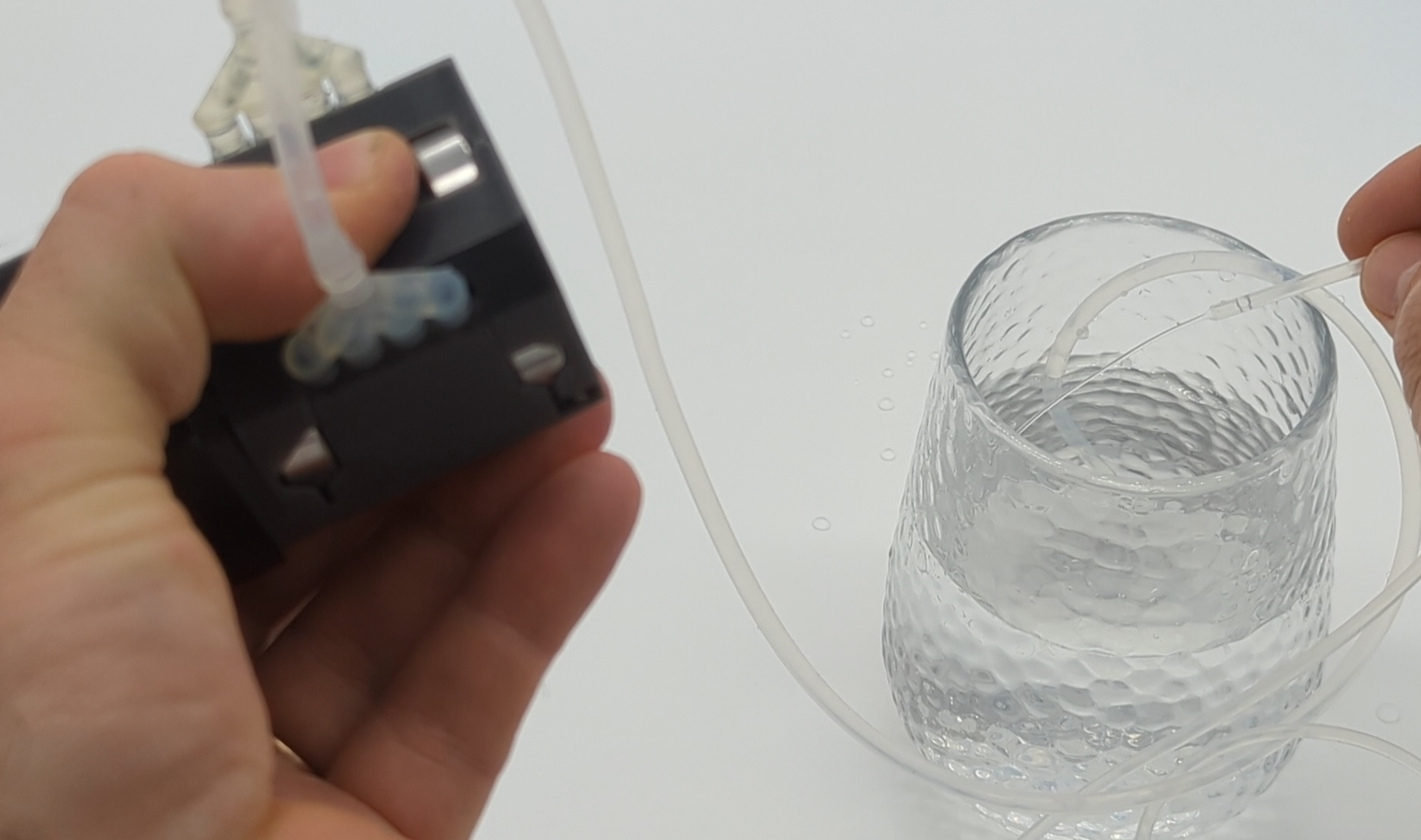
Now back to the beginning (8/1/2024):
Let's start the year off with something that everyone knows and loves: Peristaltic Pumps... I guess, nearly nobody knows about these. However, they can be very useful for moving a wide range of fluids continuously, at high precision, and while maintaining sterility!
Motivation: I have a couple products that I expect to reach later this year that will require precise pumping of fluids with a range of viscosities, flowrates and pressures. Since I'll need custom pumps, I imagine other projects and labs may need some too. If that sounds like you, feel free to send me an email at hello@joshadams.io, to introduce yourself and tell me about your problems.
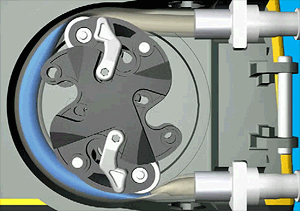
Before digging into uninformed design, I'm opening a couple week period to do deeper research around what exists in the market, and do my best to have Mom Test approved conversations with folks in the peristaltic know/need.
I have found a few great open source/design projects:
- Umut Civici's Design:
https://www.youtube.com/watch?v=4LBqCxvwyrU&ab_channel=UmutCivici
https://github.com/umutcvc/Open-Pump - FAST Pump Academic Paper, multichannel:
https://www.sciencedirect.com/science/article/pii/S2468067220300249 - Patty's Lab, youtuber:
https://www.youtube.com/watch?v=2UYmvd_jUCE&ab_channel=PattysLab
https://www.thingiverse.com/thing:5409562 - iGem Micro fluidics:
https://www.youtube.com/watch?v=FVY1cF4h9LI&ab_channel=iGEMAachen
https://www.instructables.com/Open-Source-Peristaltic-Pump/
8/15/2024 Update: Initial research complete and performance specifications outlined:
Initial conversations with engineers and peristaltic pump users
1. Dr. Madi Babaiasl, Assistant Professor of Robotics, Saint Louis University. Discussion of Robotic actuators, coding control, motion planning, soft robotics, assistive robots, cobots, teaching/learning robotics – August 5th.
2. Dr. Jenna Gorlewicz, Associate Dean of Research and Innovation at Saint Louis University. Discussion of robotic applications, specifically: Telerobots, rehabilitative robots, robots in the workplace, wearables, venture capital/startups, university admin perspectives on robotic education – August 5th
3. Grace Yost, recent Biomedical Engineering MS graduate. Discussion of her experimentation in cellular stimulation utilizing peristaltic pumps in conjunction with Additively Manufactured(PolyJet) fixtures – August 7th
4. Phil Langhorst Founder of Invention House and inventor of the Raphael 4040, an automated coating solution for the conformal coating of PCB's. Discussion of the Raphael 4040 and how it uses peristaltic pumping to precisely meter, mix and apply liquid coatings – August 7th
5. Khamhbawihum Cenhrang, PhD candidate in Chemistry studying effects and methods of measurement of shear stress on cellular expression (Article on his research). Discussion of his research and the peristaltic pumps used his lab – August 14th
6. Stuart Diller CEO of ESTAT, an engineering start up producing high performance eletroadhesive clutches – August 15th
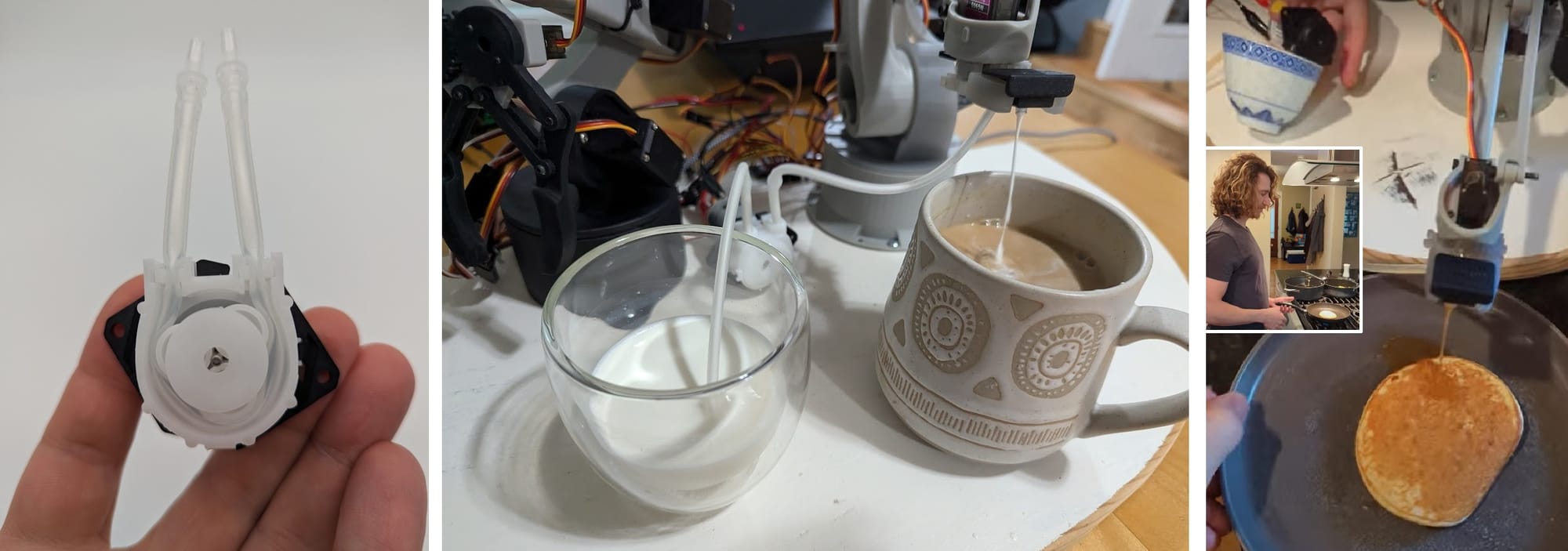
Takeaways from conversations and testing of the low cost pumps:
1. Cleaning/Clogging can be an issue for the maintained use and reuse of tubing.
2. If Air bubbles are introduced they can cause significant issues in pump performance and downline processes.
3. There was a lack of complaints about pulsatory flow. I had expected the pressure waves generated by the pump to cause issues for users, I didn't hear any one having issues with that.
4. Ease of tube replacement. The tubes have a limited useful life (weeks to years).It's important that they are easy to swap out for higher frequency changeover applications.
5. Preference was expressed for pneumatic (air) over hydraulic (liquid) actuation of soft robots. Dr. Babaiasl also recommended a number of papers, of which, Soft Actuators and Robots Enabled by Additive Manufacturing was my favorite.
6. In each of the cheap pumps I purchased, the smooth motor shaft was used to directly drive the surface of the rollers (which acted like planetary gears) that then compressed the silicone tubing.
7. Length of soft tubing on the inlet side greatly effects the pumps ability to pump. EG. pumps were capable of generating necessary suction for vertical lift of water or half and half to a 6"+ height, however, fluids with greater viscosity like honey could not be suctioned up any height and required a primed (fluid filled) tube in order to move any volume.
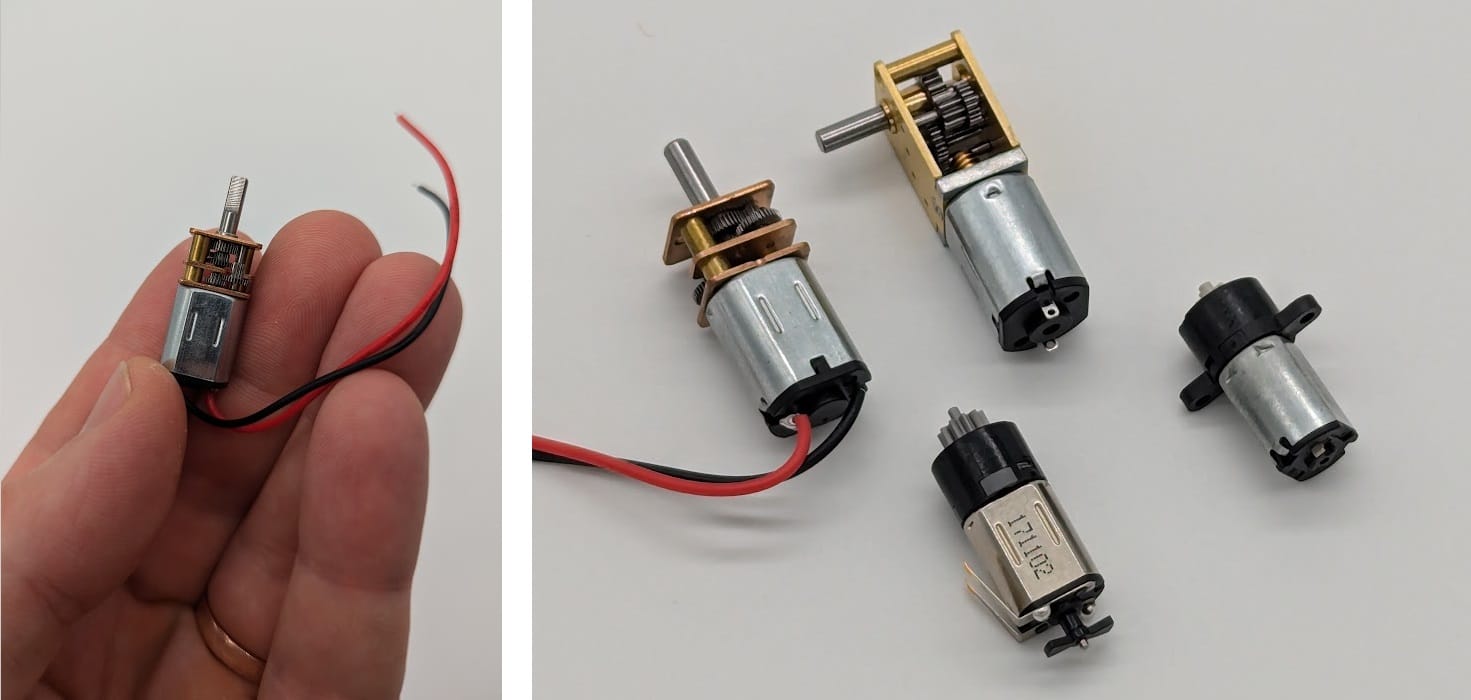
Formfactor Specifications for the Pump(s) I'll release:
Application 1: Smooth, low volume, high precision flow
Rough Product Specifications:
i. Pressure: 10+ psi
ii. Fluid: Low viscosity liquids in the 1-150 centipoise range (roughly the viscosity of water to light maple syrup)
iii. Flow rate: 0.5 to 25 mL/Min
iv. Size/weight/special requirements: Requires tubing to be UV light blocking, otherwise flexible.
Application 2: (STRETCH Goal A) Multichannel pump for mixing 10:1 2-part Silicone
Rough Product Specifications:
i. Pressure: Ideally 70+ psi
ii. Fluid: 10 part material is 100,000-150,000 centipoise the 1 part material is 400-1500 centipoise.
iii. Flow rate: 500+ mL/min
iv. Size/weight/special requirements: Multichannel mixing for a variety of ratios from 1:1 to 10:1, tubing that does not interact with either part of platinum cure silicone (this may rule out silicone tubing), otherwise flexible.
Application 3: (STRETCH Goal B) Light/small air pump for soft robotics
Rough Product Specifications:
i. Pressure range: pull at least a 3 psi vacuum (below atmospheric pressure) and compress 20+ psi
ii. Fluid: Air (bonus if it's also compatible with fluids like water/oil)
iii. Flow rate: 100+ mL/Min
iv. Size/weight/special requirements: As small and light as possible for wearable/small robotic applications. Ideally requiring 5v power supply.
9/1/2024 Development to Product launch!
It's been a wild ride over the last two weeks, crushing through 12 whole prototypes--that's nearly 1 new version every day. The daily routine started with post processing the batch of parts that printed overnight, testing and redesigning in SolidWorks while placing any new orders for items like bearings, screws, motors, silicone tubing and electronics, and then hitting print before calling it a day.
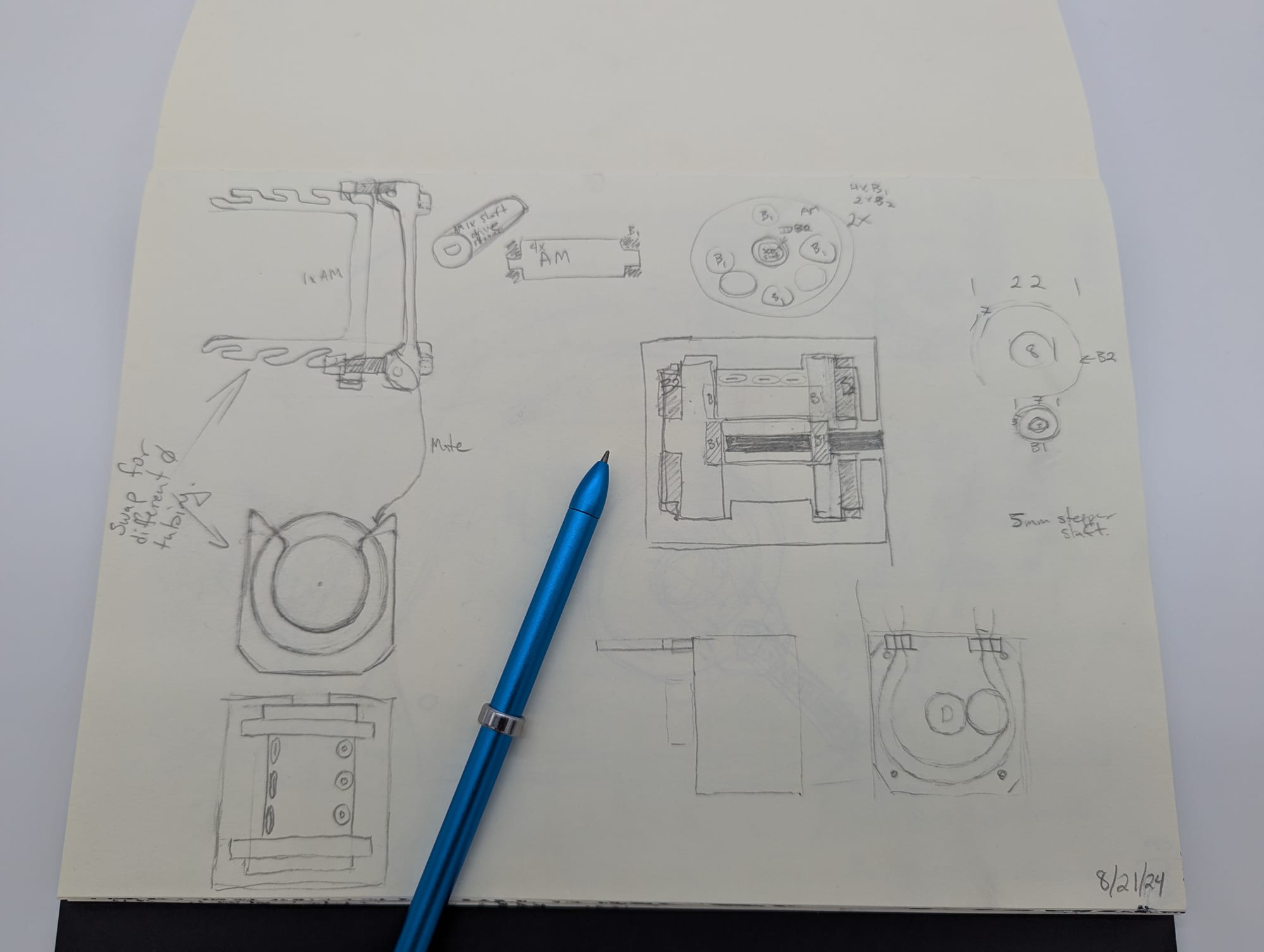
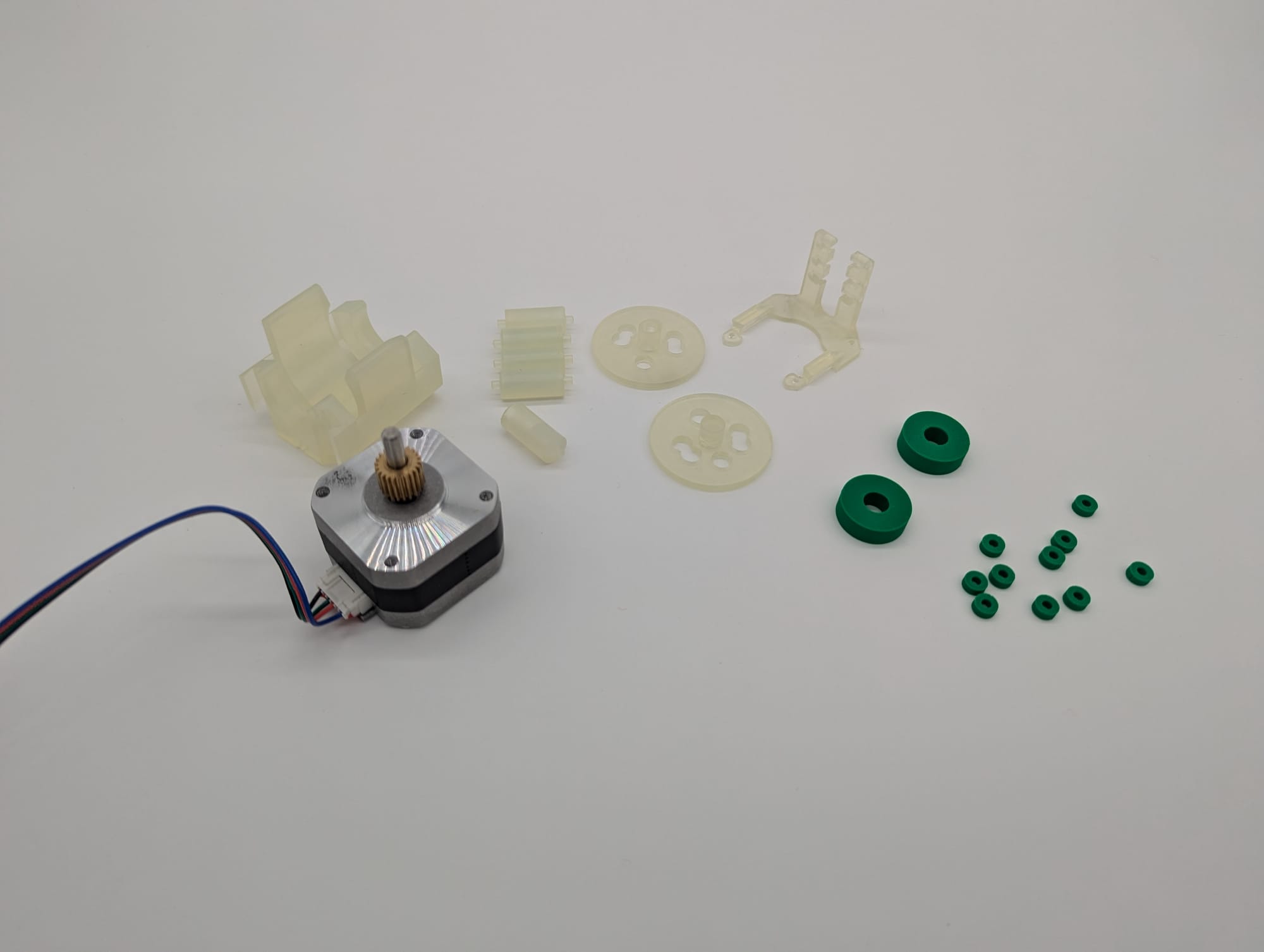
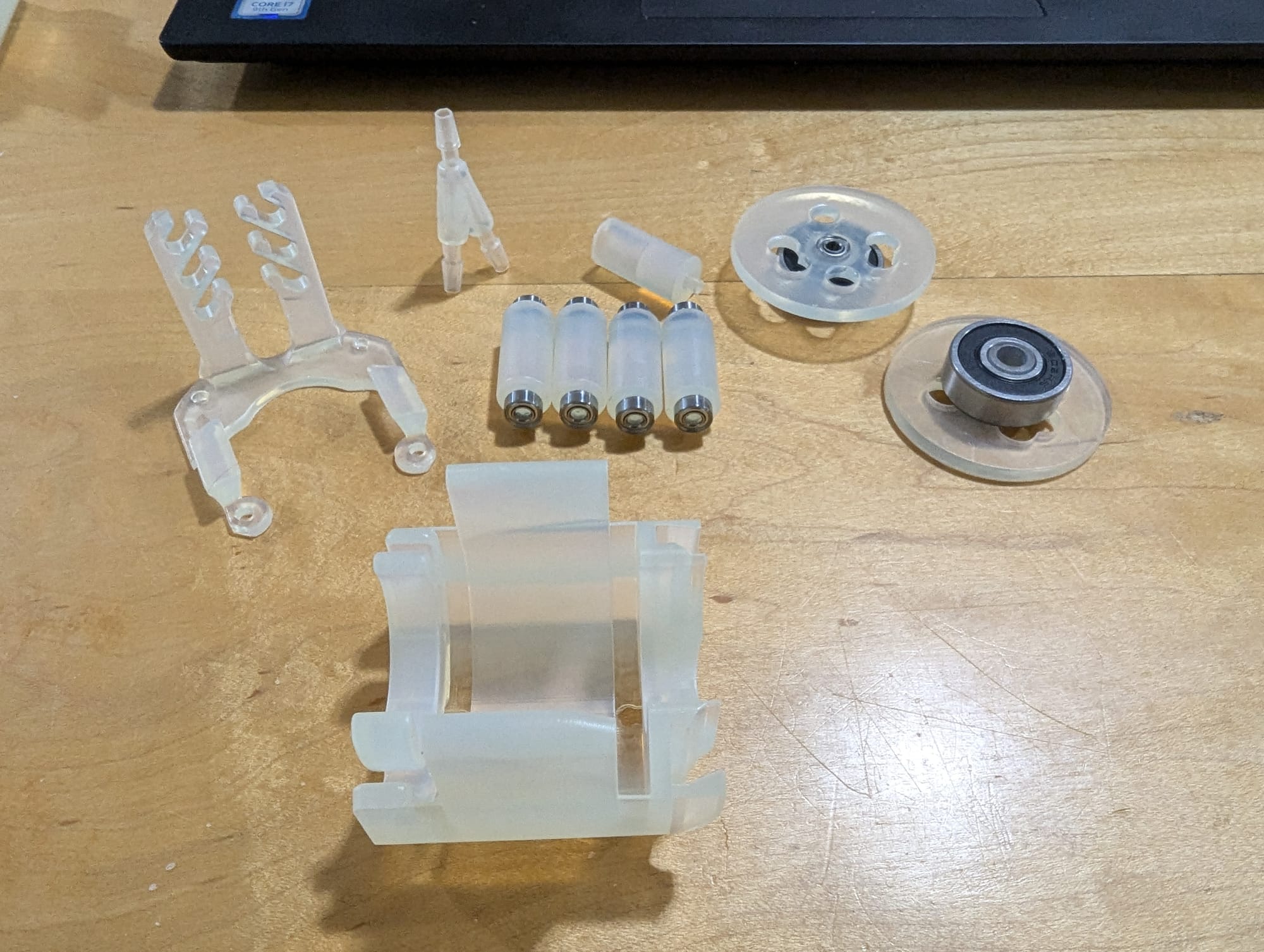
There's something satisfying in sketching out a functional mechanism. I love how it feels to design in my mind, on paper, in CAD and with my hands--it can such an engaging and creatively alive process!
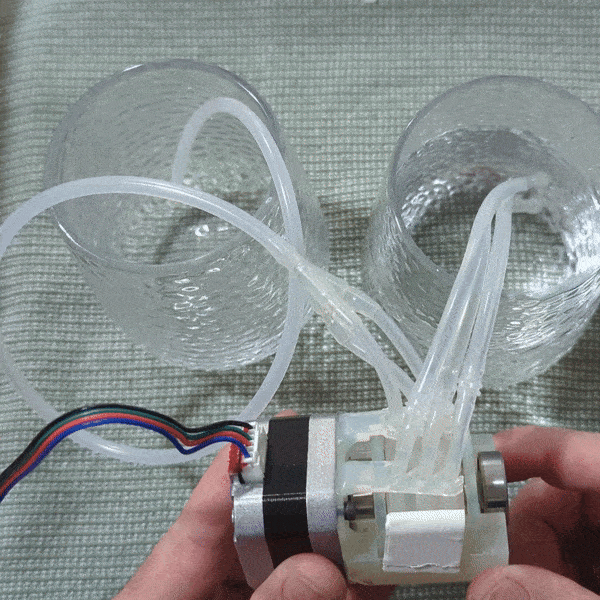
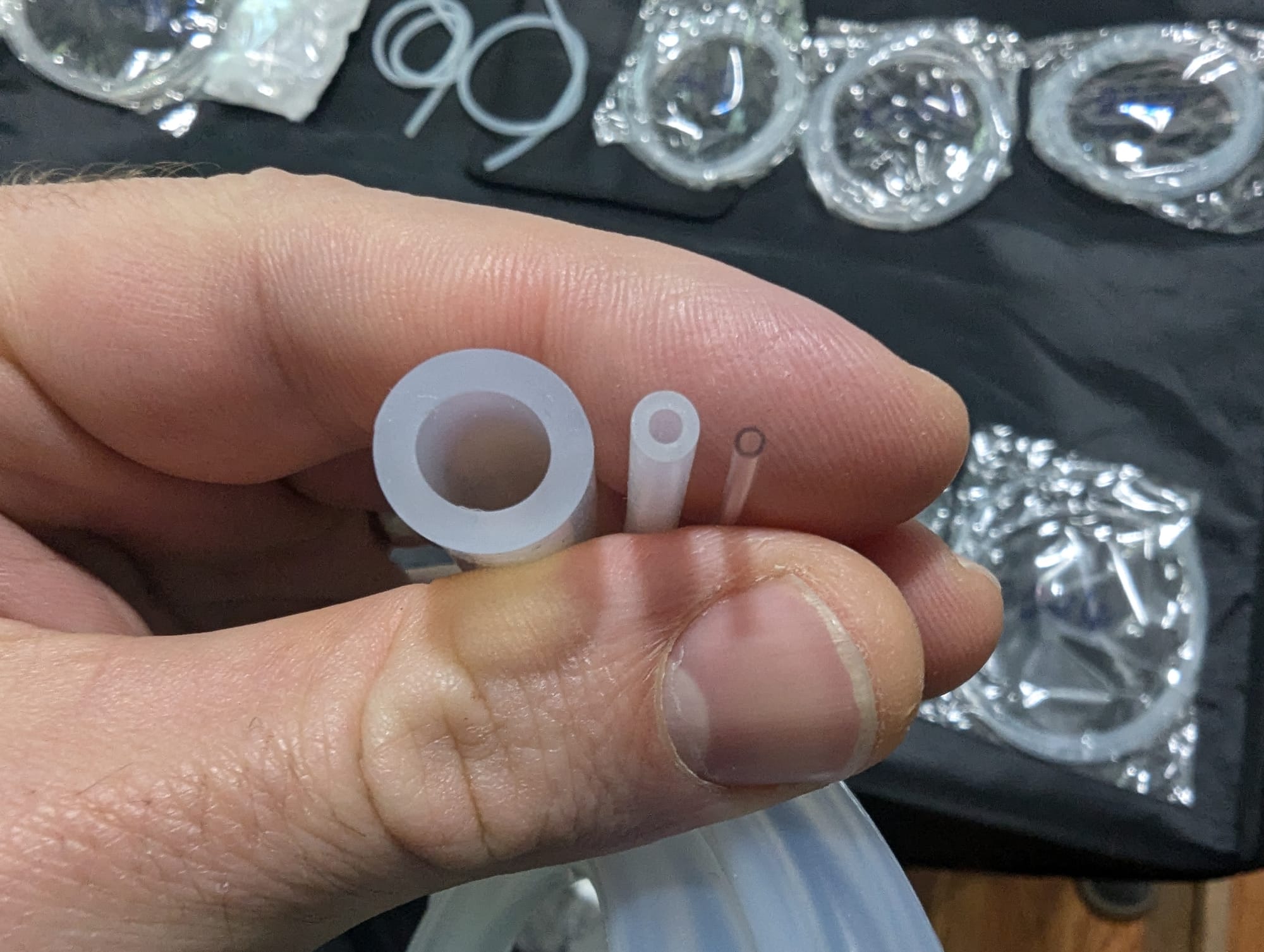
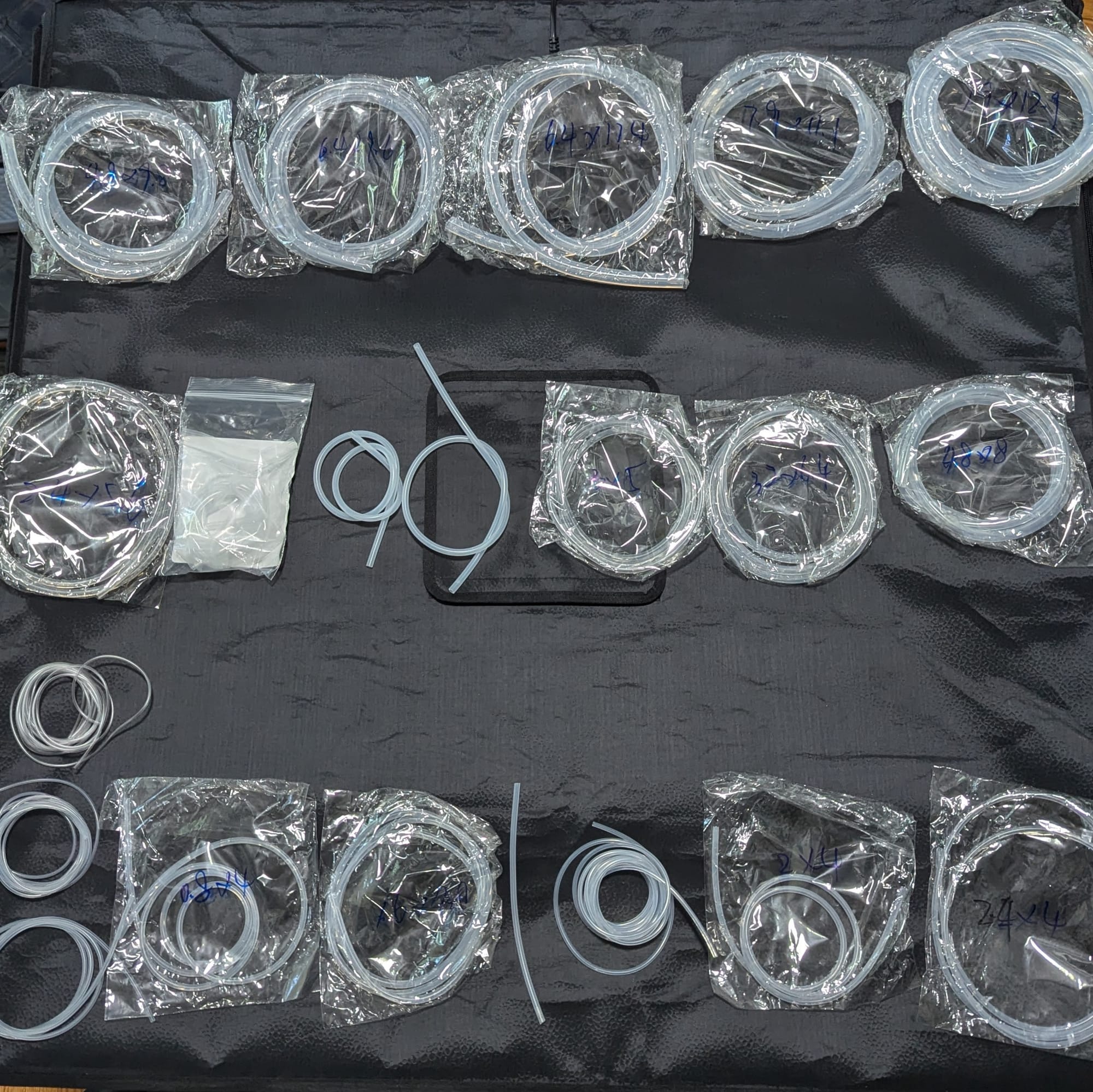
Procured a wide range of Silicone (and one PVC) tubing for testing, since ID/OD dimensions and elastic rebound are crucial for the fit and performance. I ended up proceeding with 2mmIDx4mmOD for this version.
After printing the first 8 versions in the translucent Durable resin from Formlabs, I discovered that it just wasn't quite stiff enough to pump well. So I pivoted over to the grey Tough 2000, an ABS like standby in many of my projects.
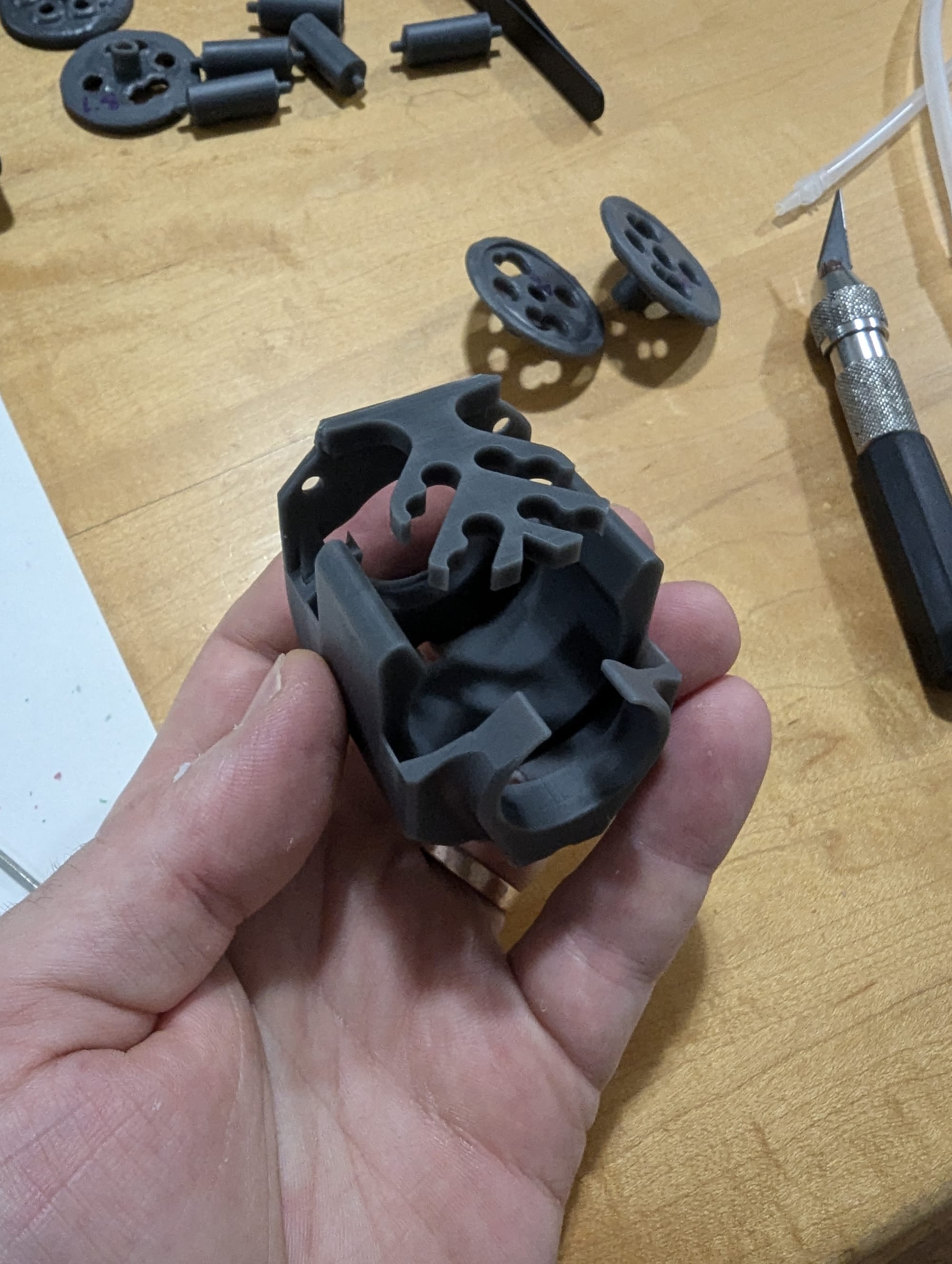
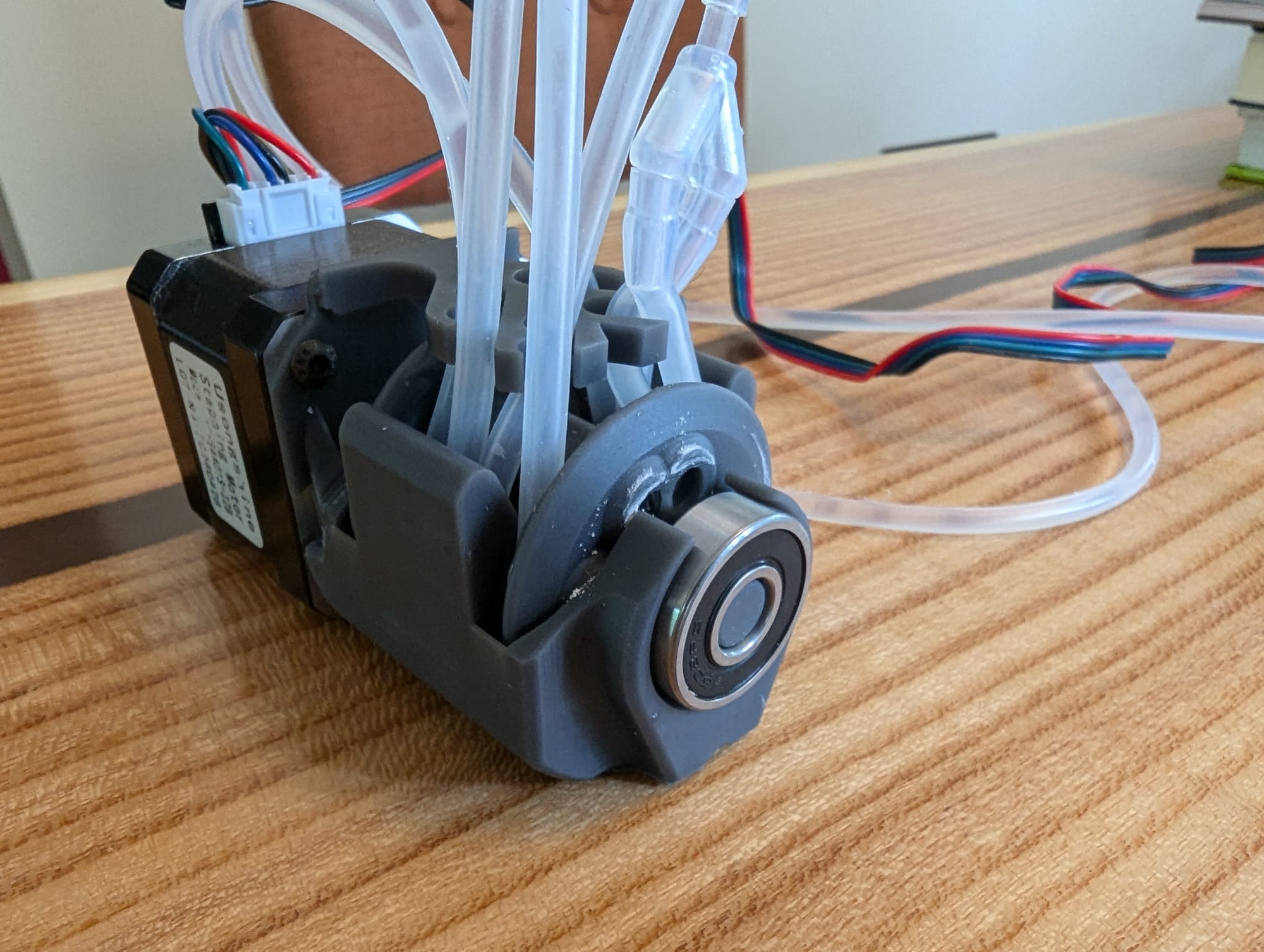
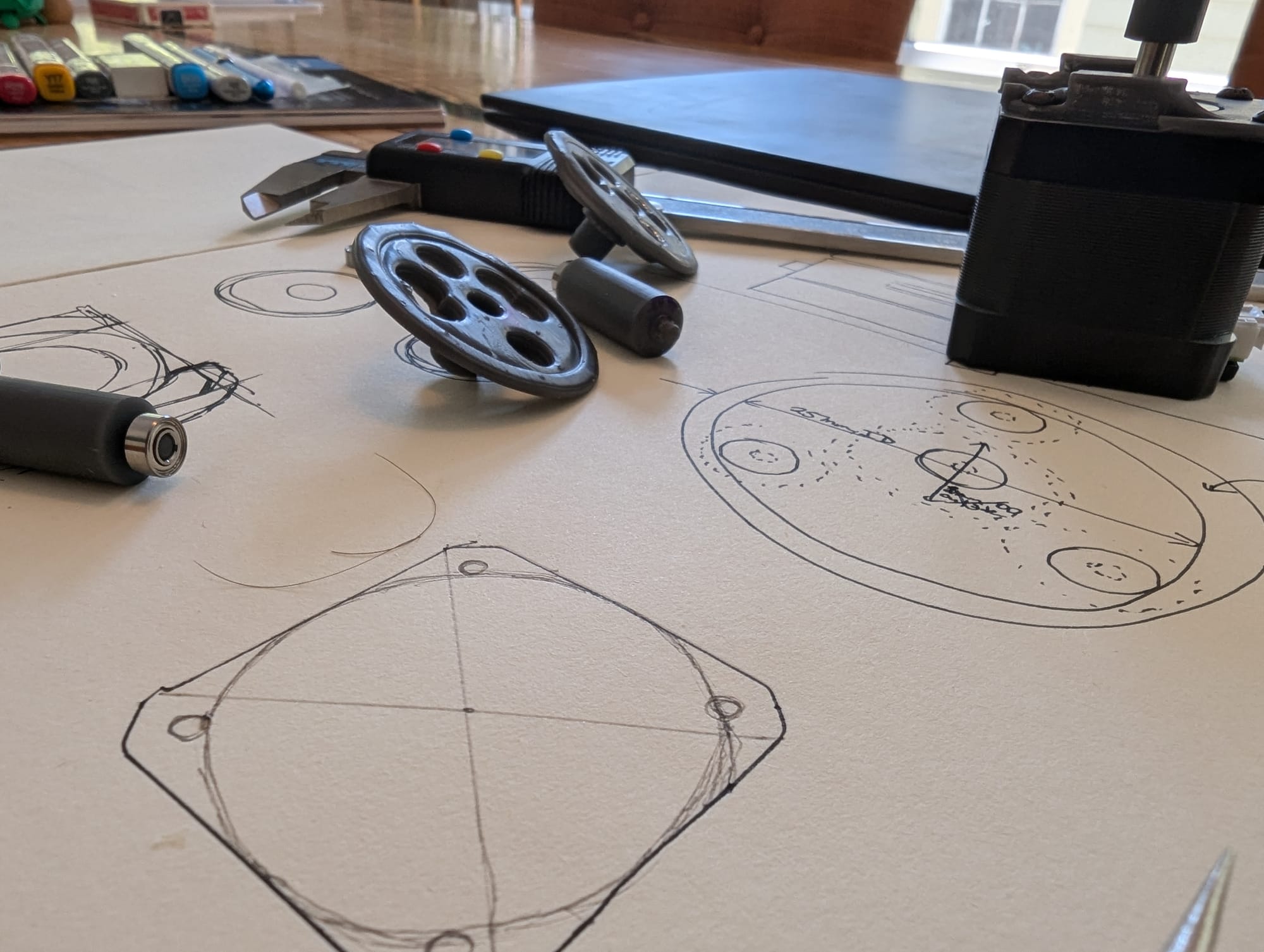
The Tough2000 proved suitable, however, a number of areas showed issues with rubbing, and I ended up needing to upgrade to larger bearings to carry some of the load for increased stiffness and locating components precisely.
A constraint I put on the project was compatibility with NEMA 17 stepper motors and a profile that doesn't extend beyond the 42mm square profile--luckily I found some beautiful, smooth rolling bearings with 37mmID and a 42mmOD. I also found that the Durable Resin was a great fit for printing custom manifolds for the silicone tubing I'm using.
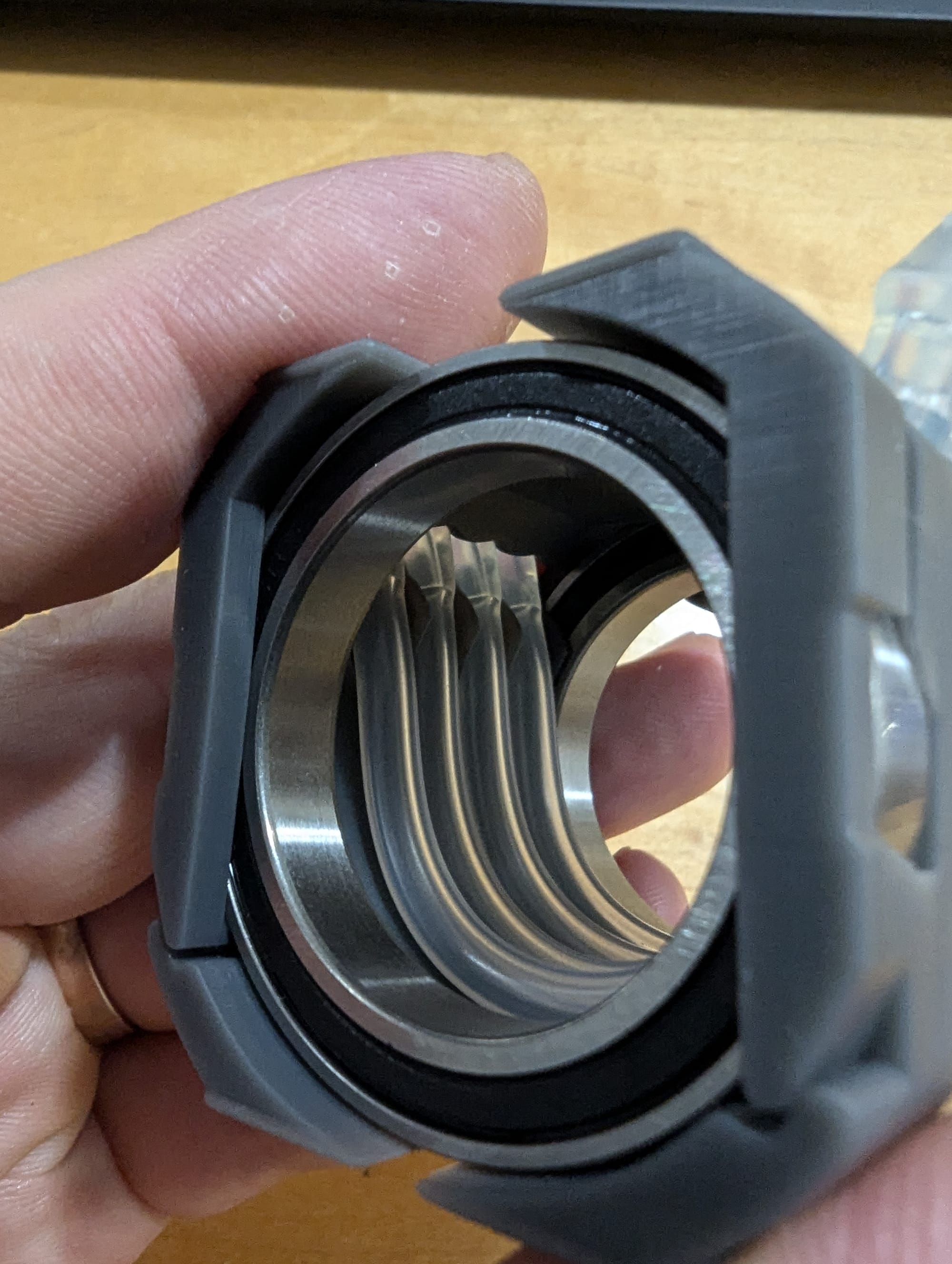
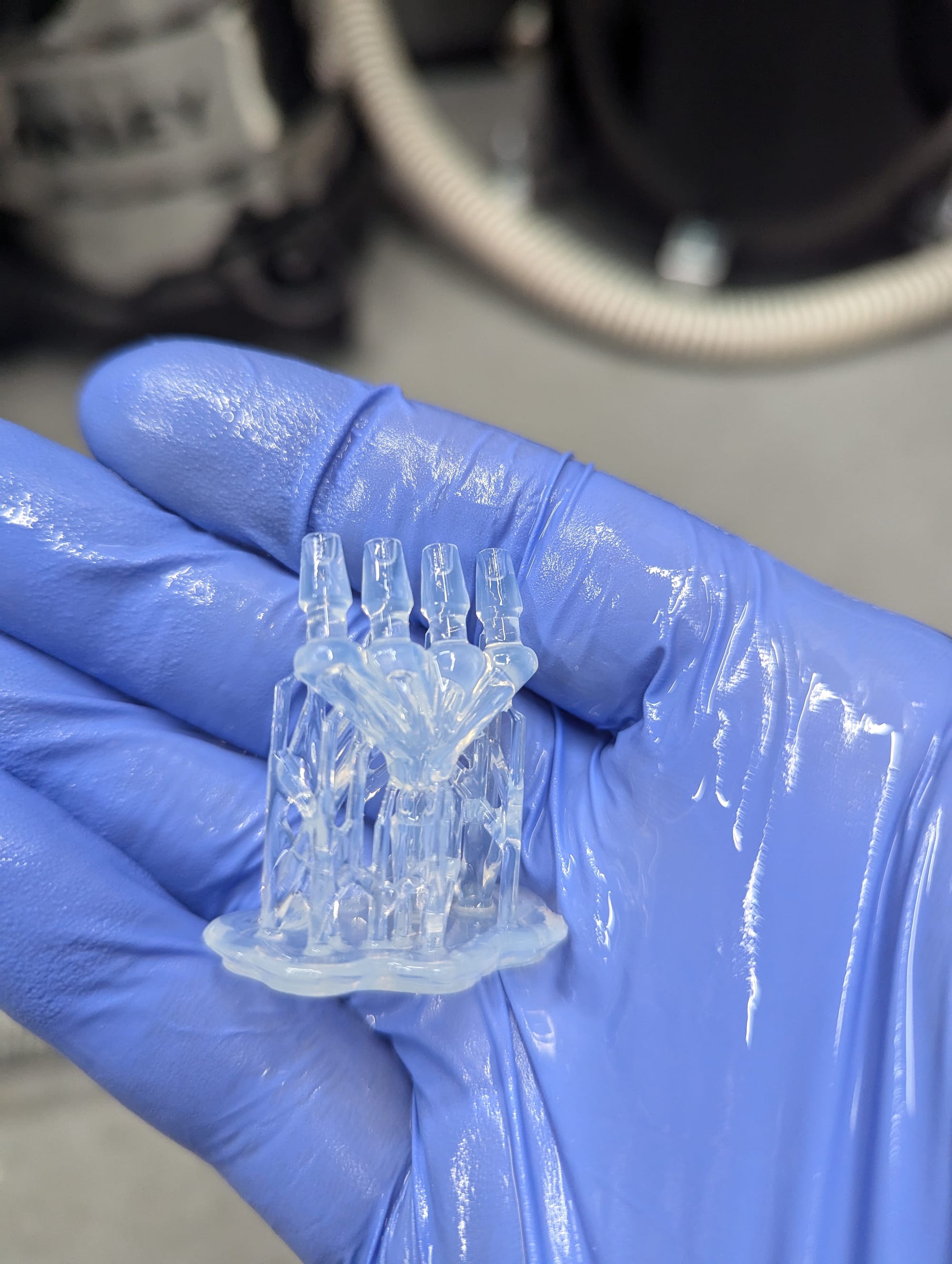
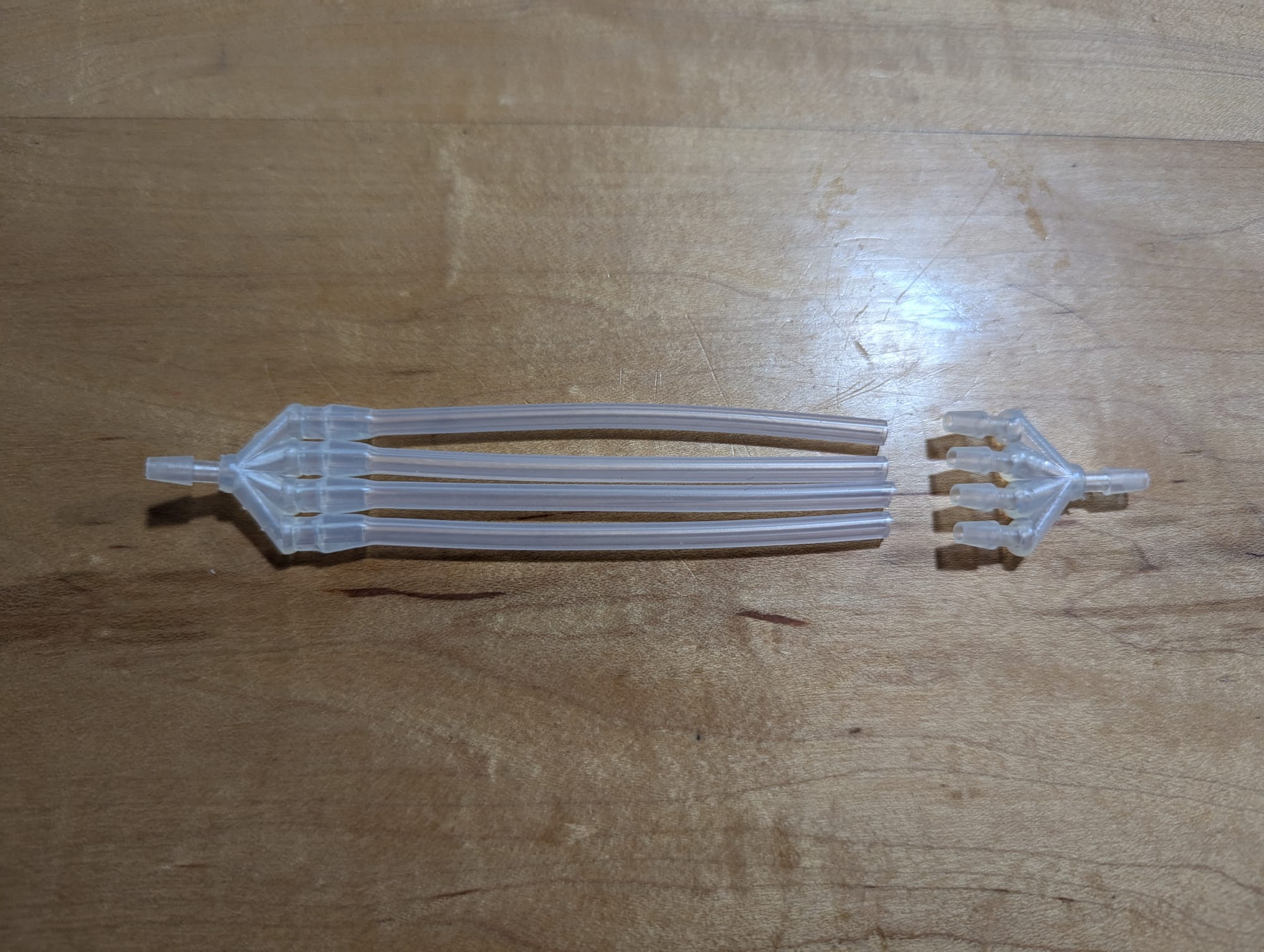
Having multiple tubing channels running through the pump was an intentional choice, specifically to pursue an idea I had around reducing the pulsatile flow inherent to peristaltic pumping while also giving a boost to our max flowrate with the same motor rpm.
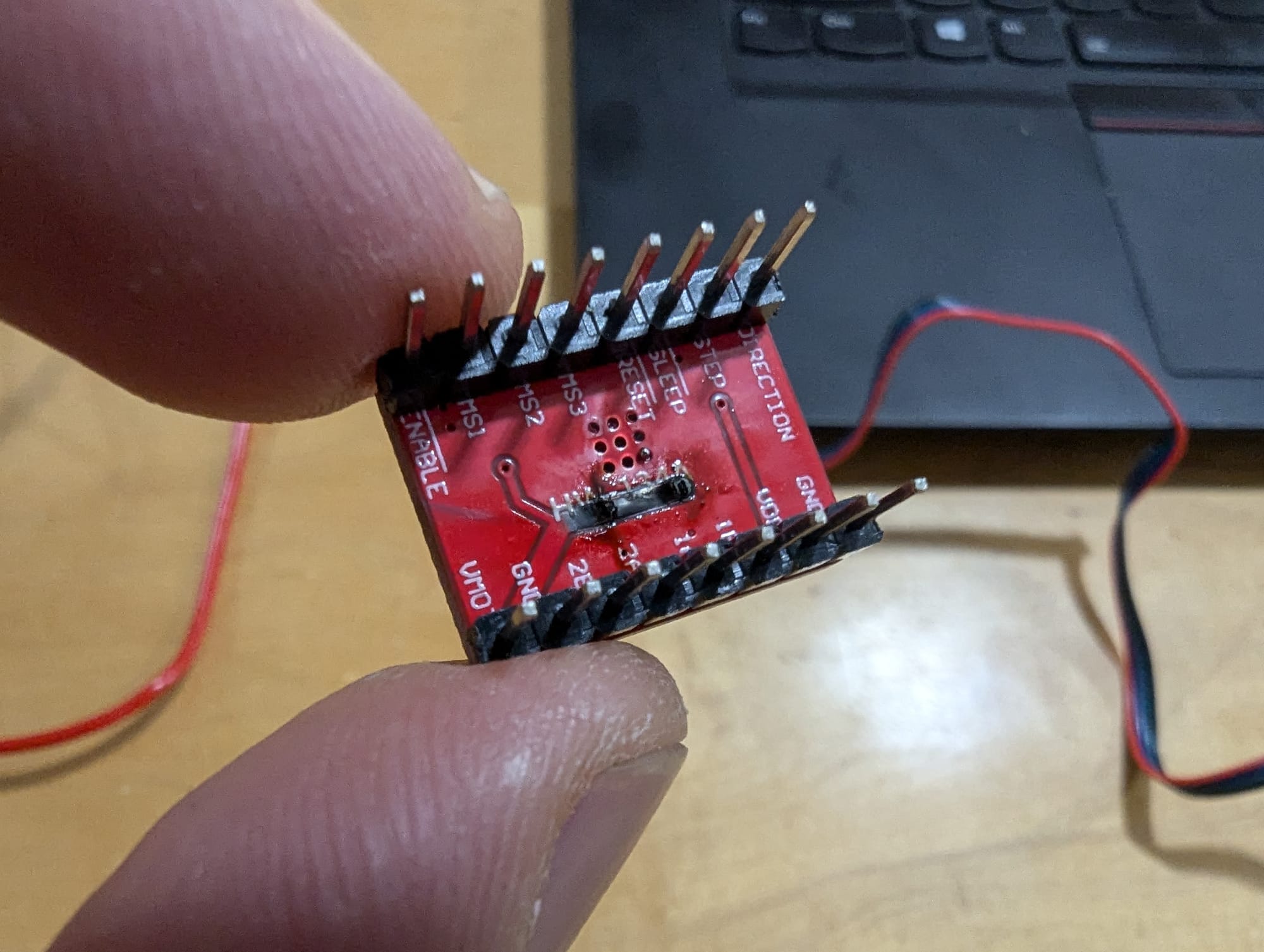
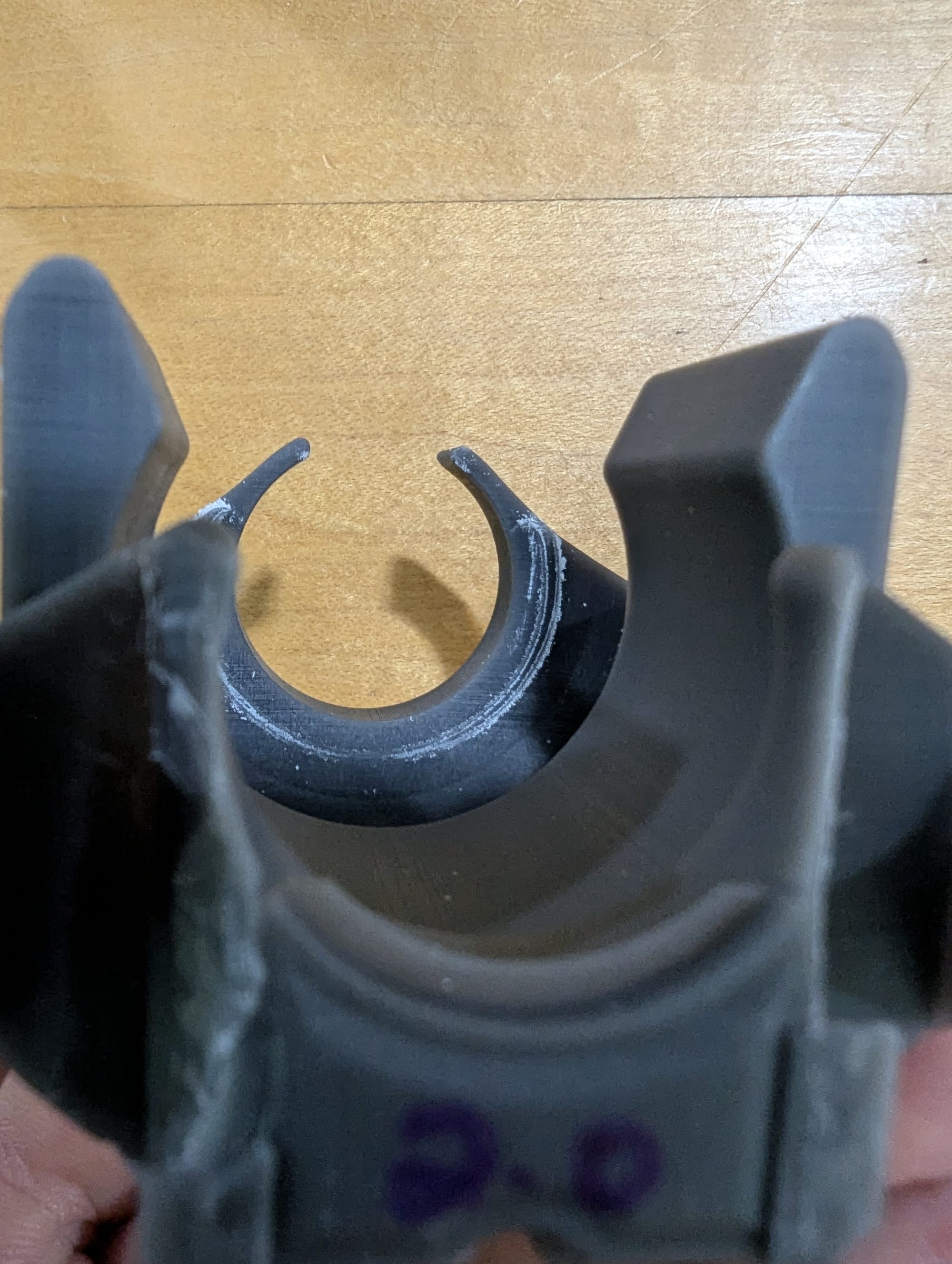
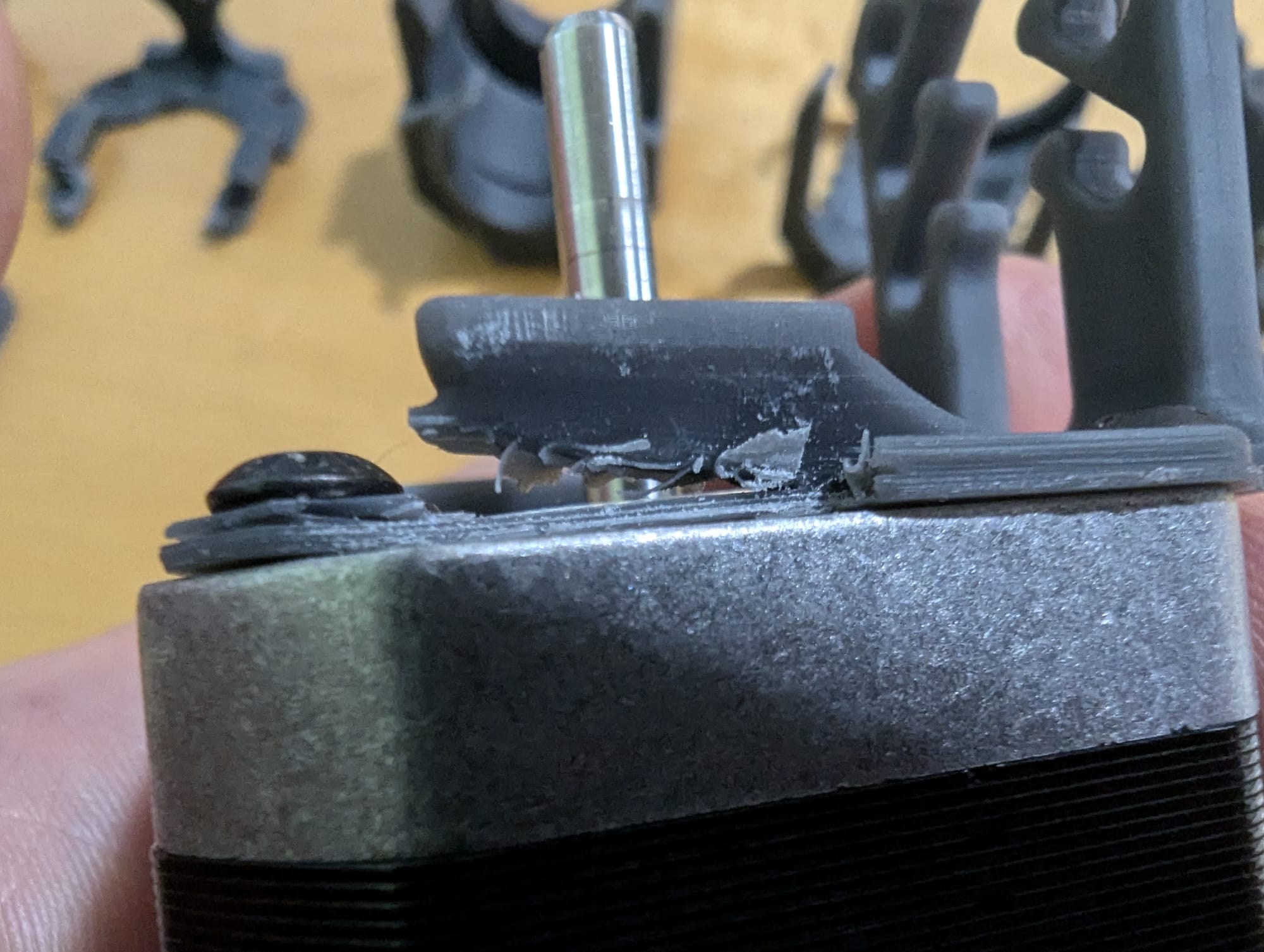
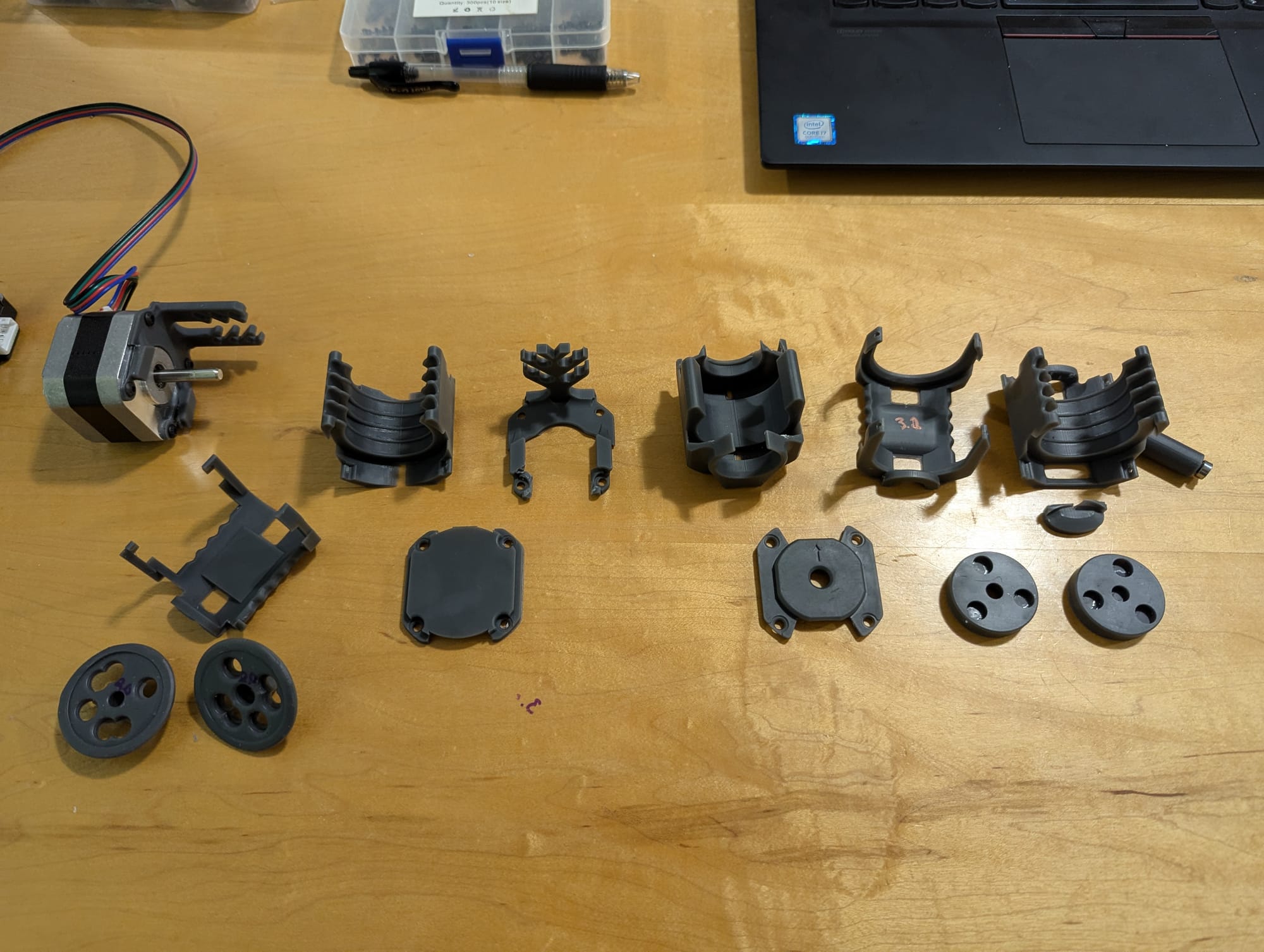
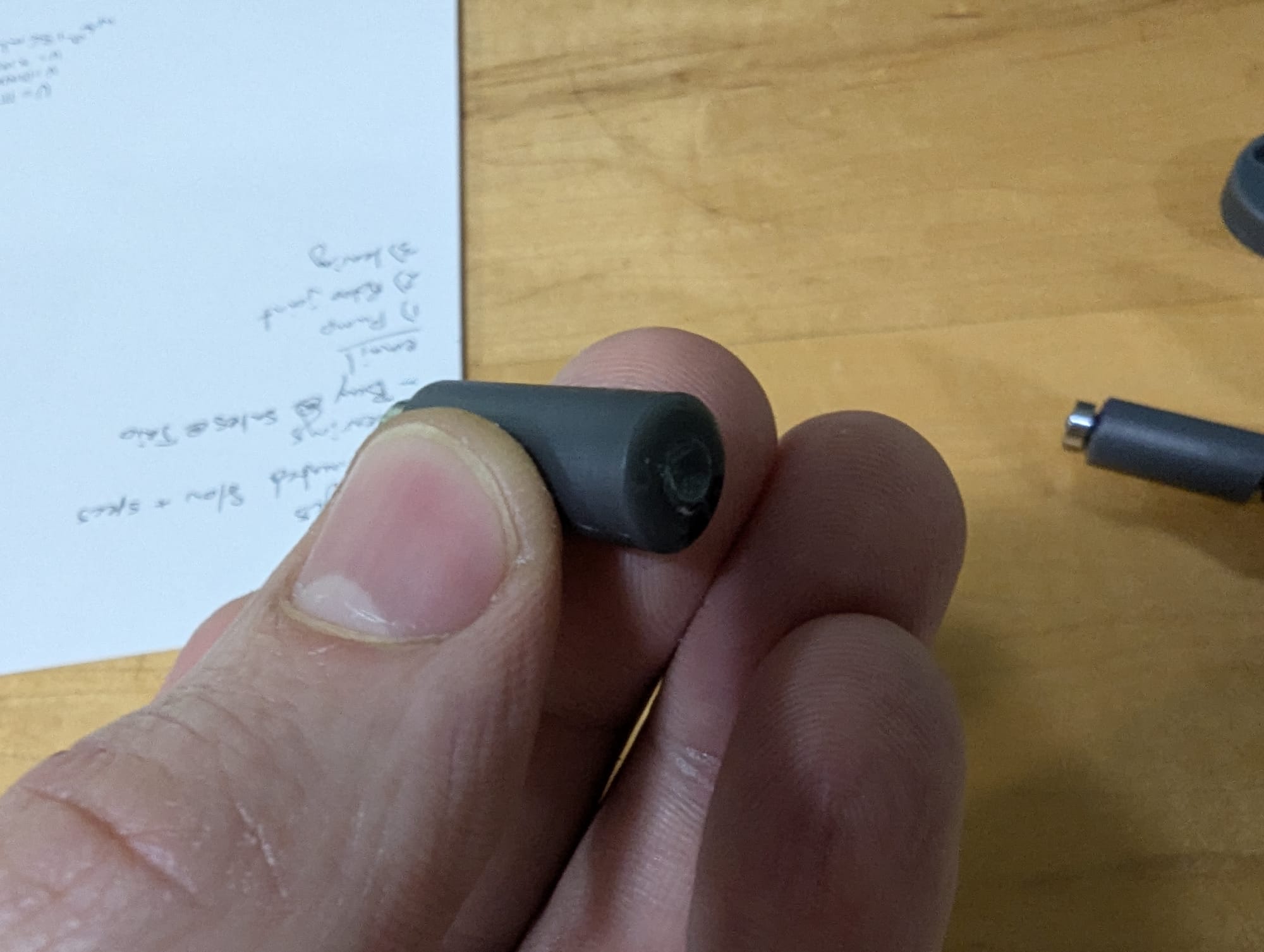
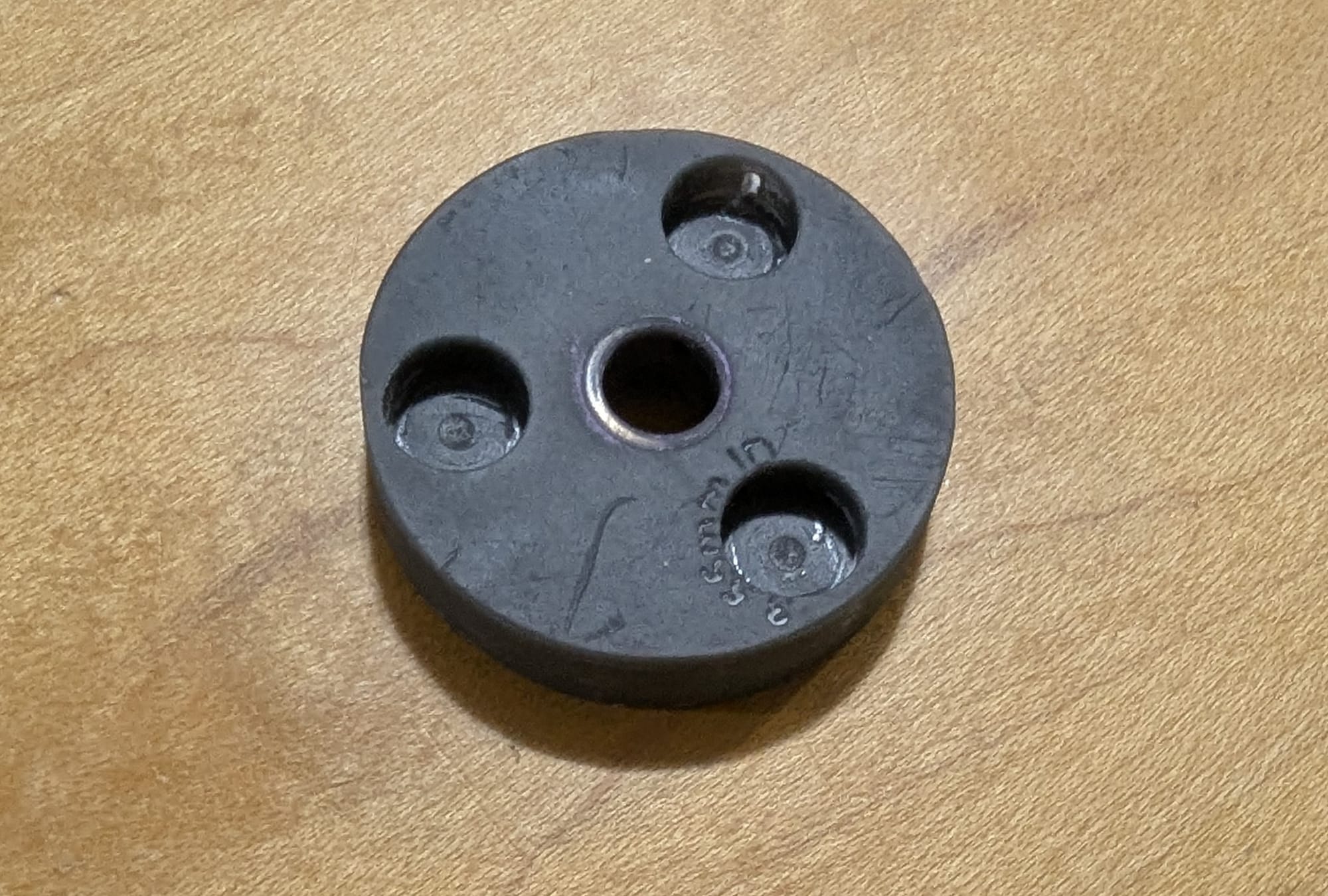
Finally after burning up a motor driver, and troubleshooting the many wear and printability issues over the course of 65 unique printed components, I give you the PrecisionFlow 1743! (I love a good naming convention: the 17 = the NEMA17 motors this pump is compatible with; 4 = the number of tubes; 3=number of rollers. I'll try to keep with this conventions so it's easy to understand this pump line at a glance)
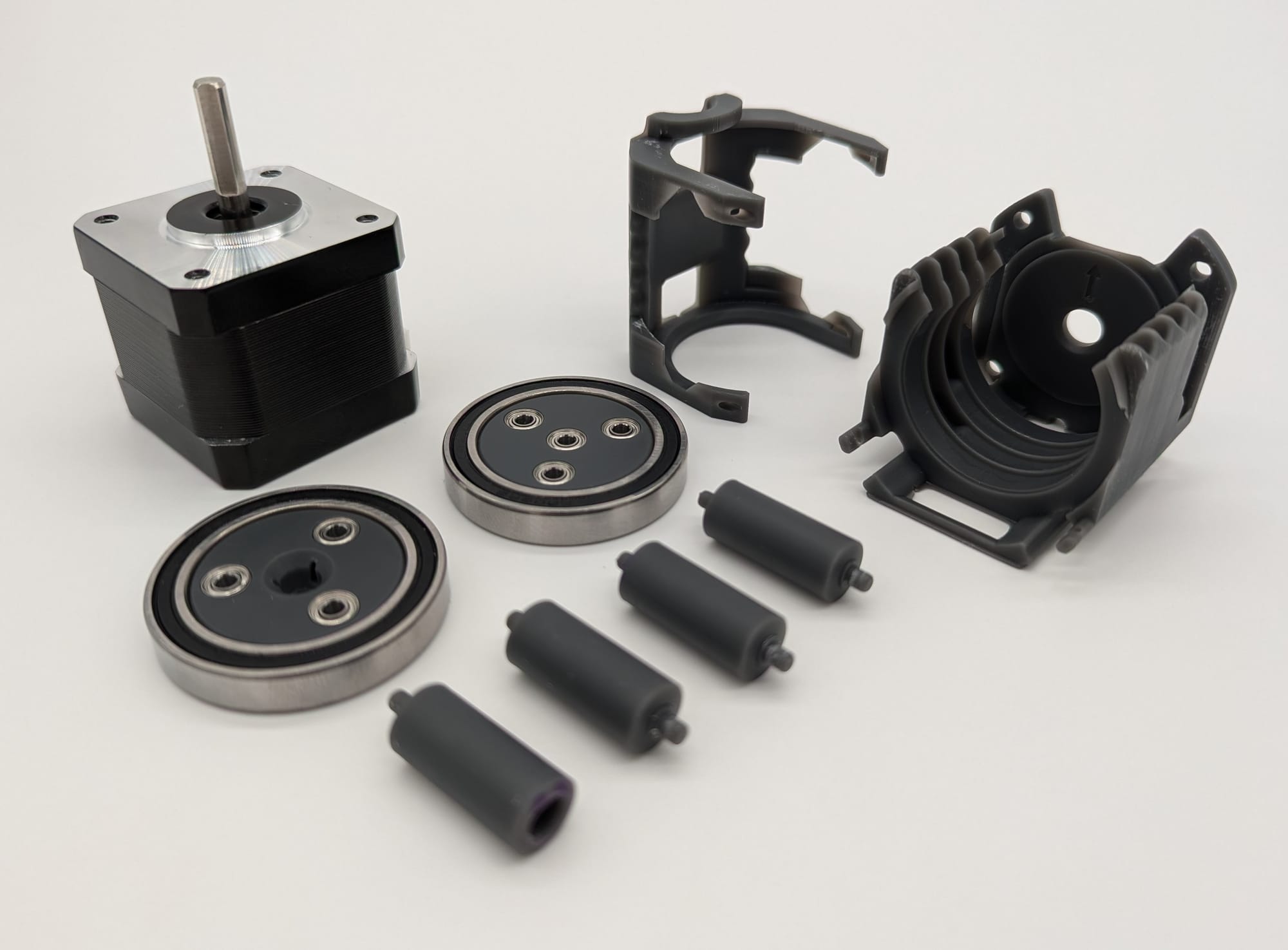
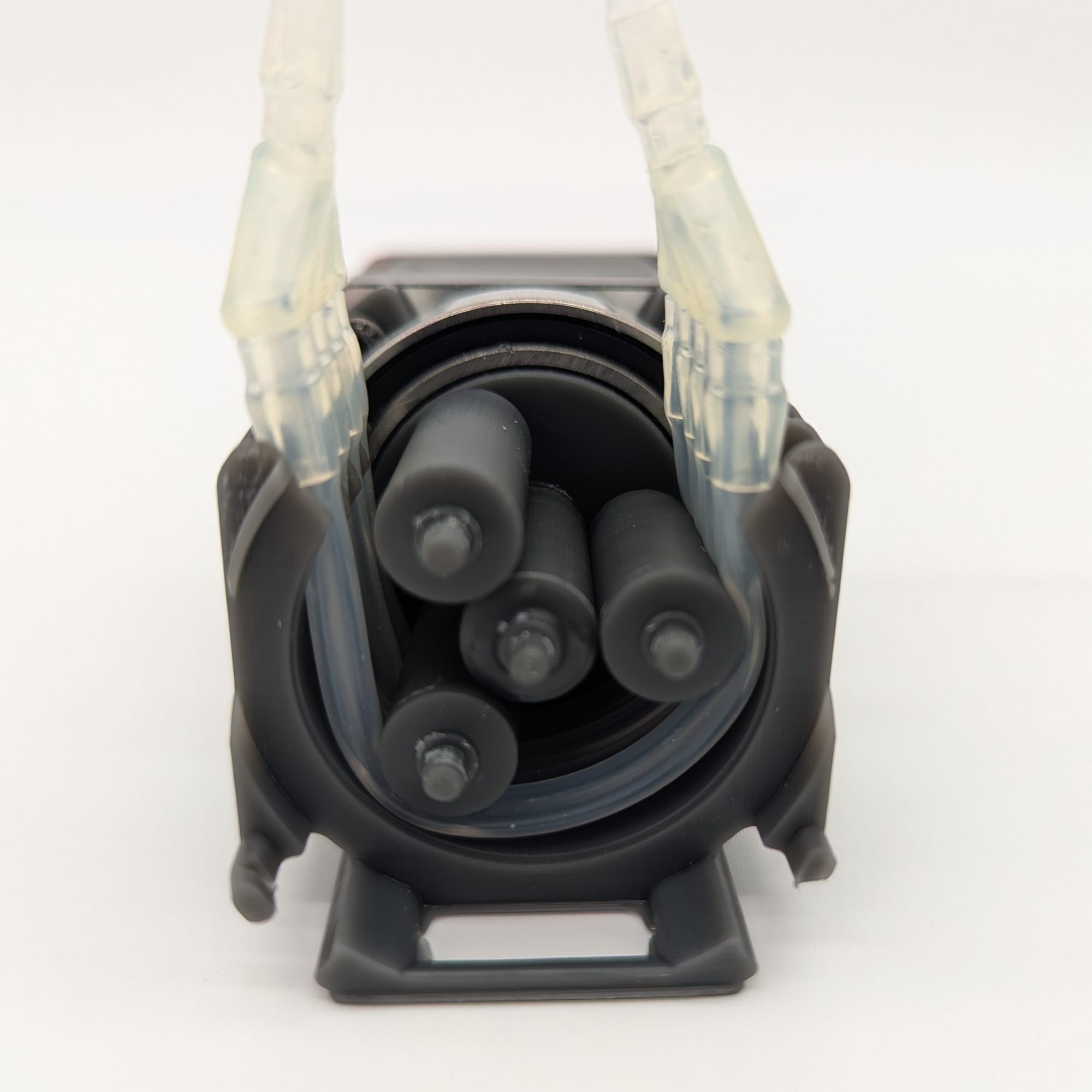
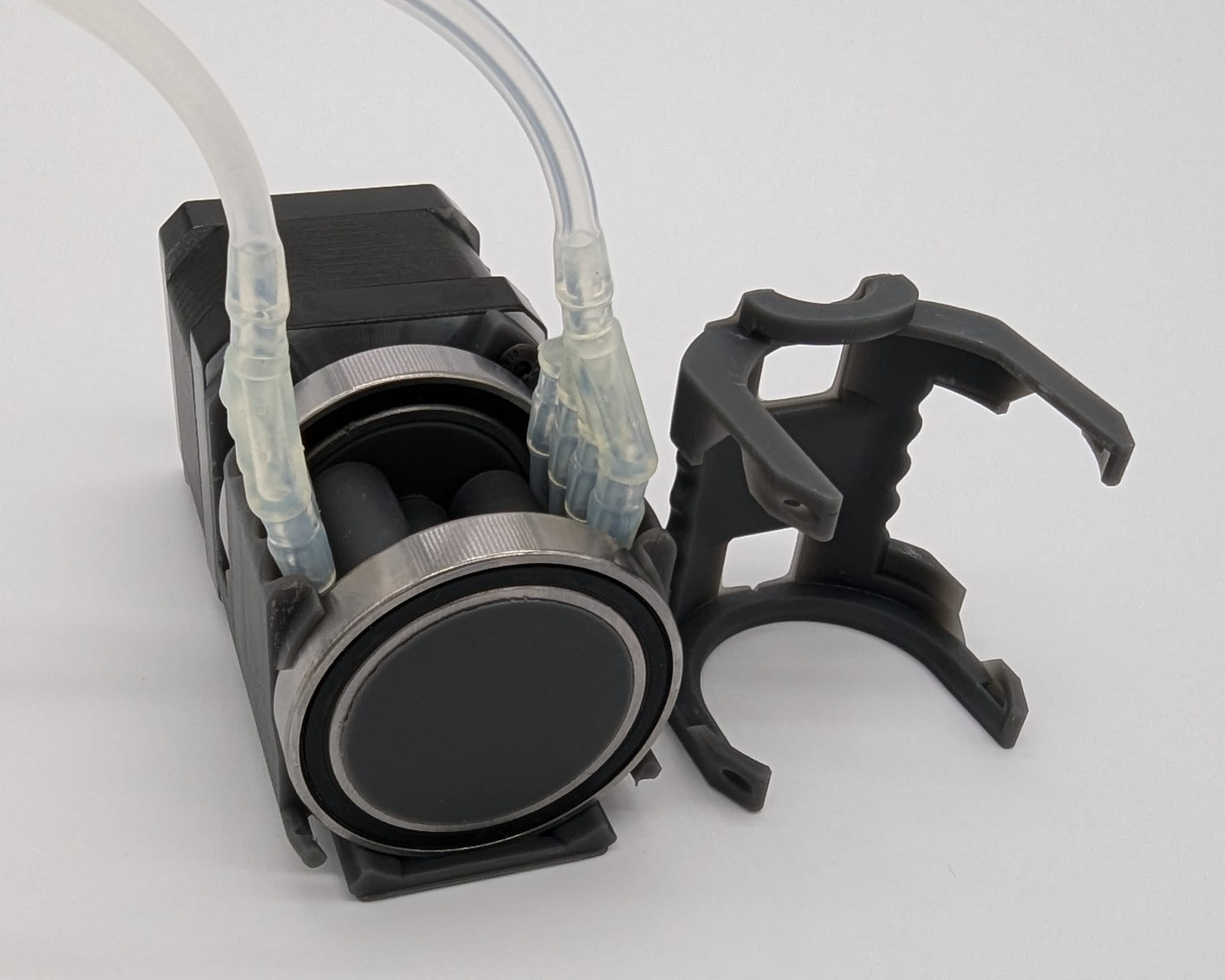
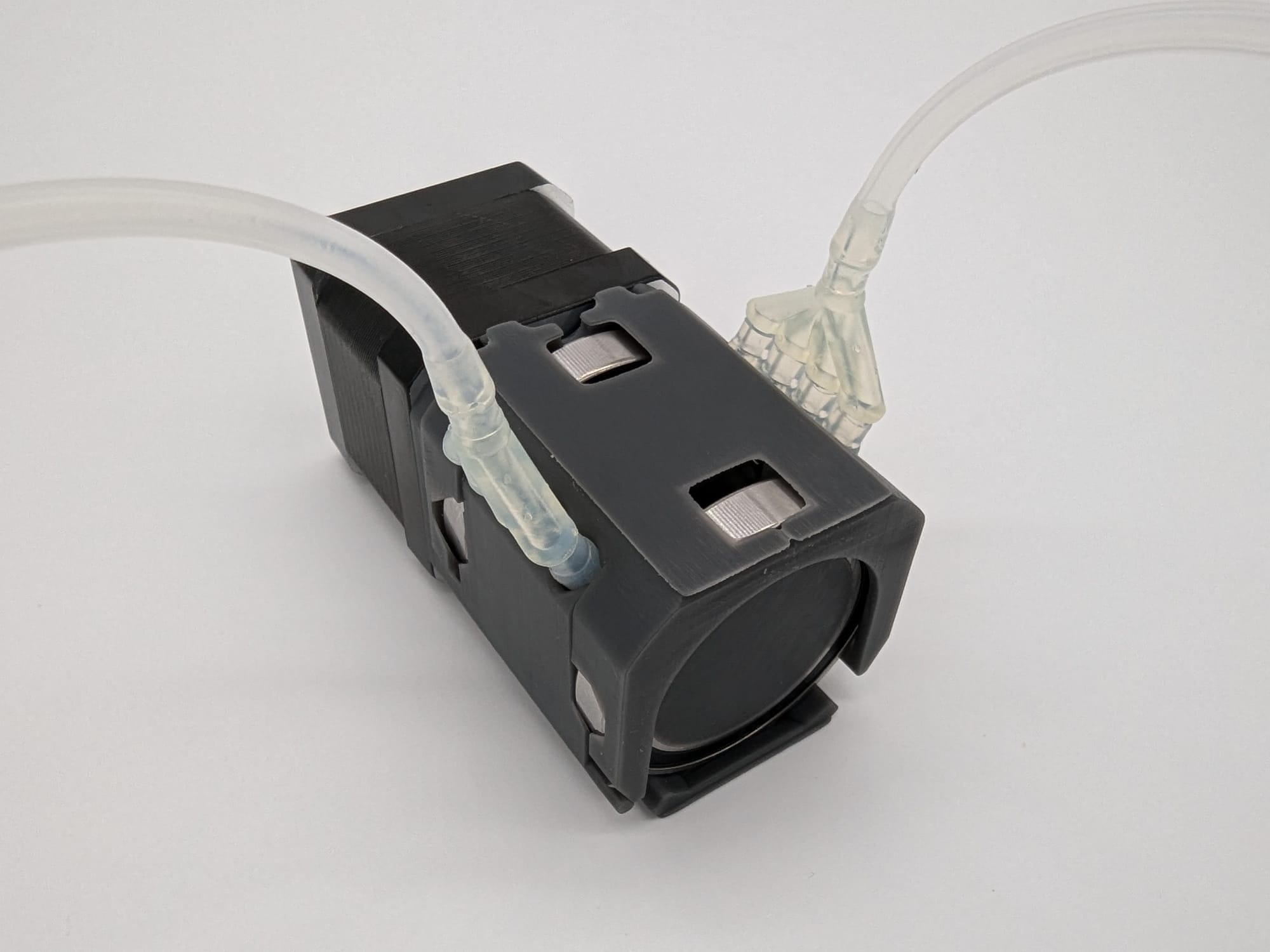
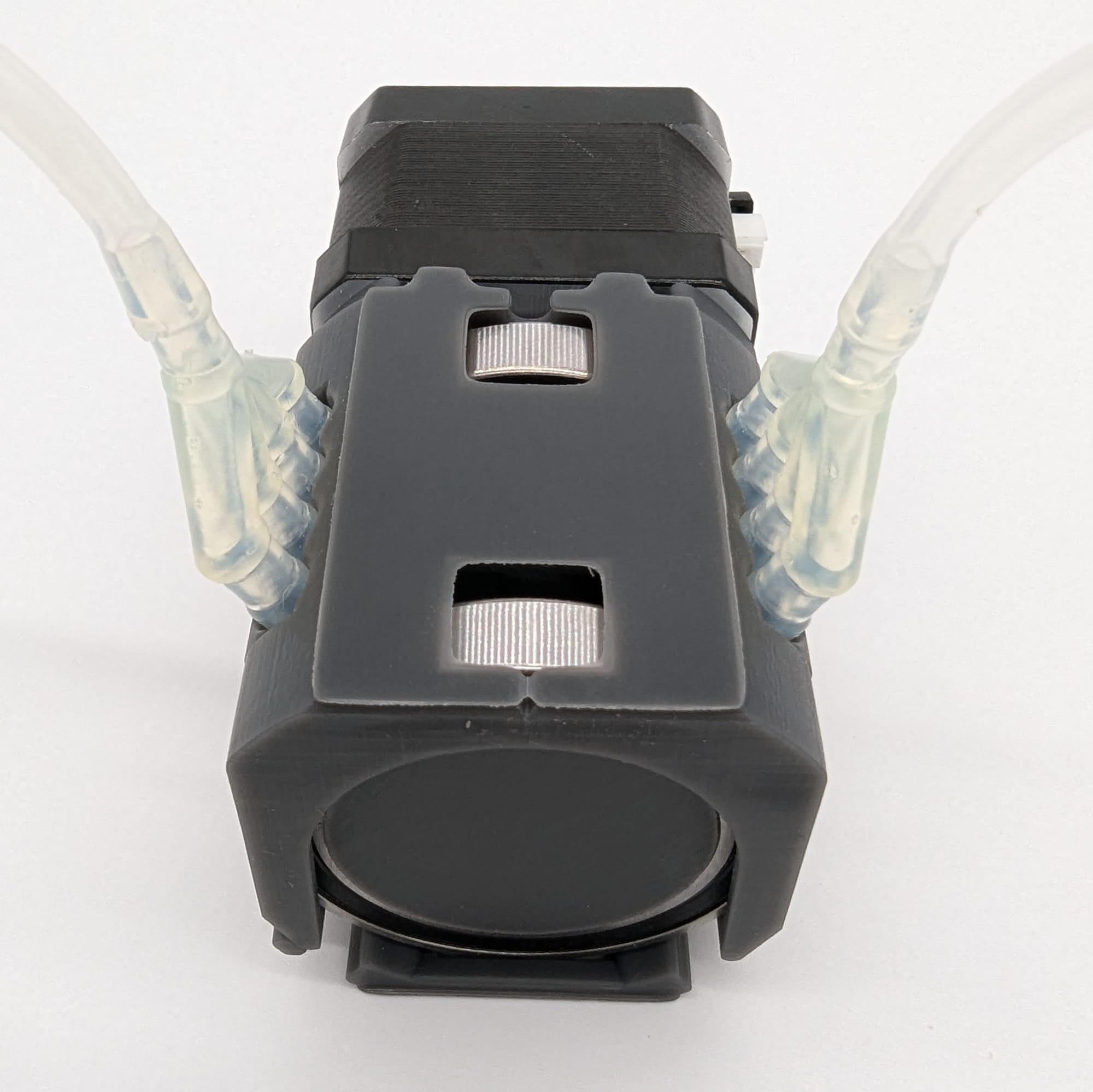
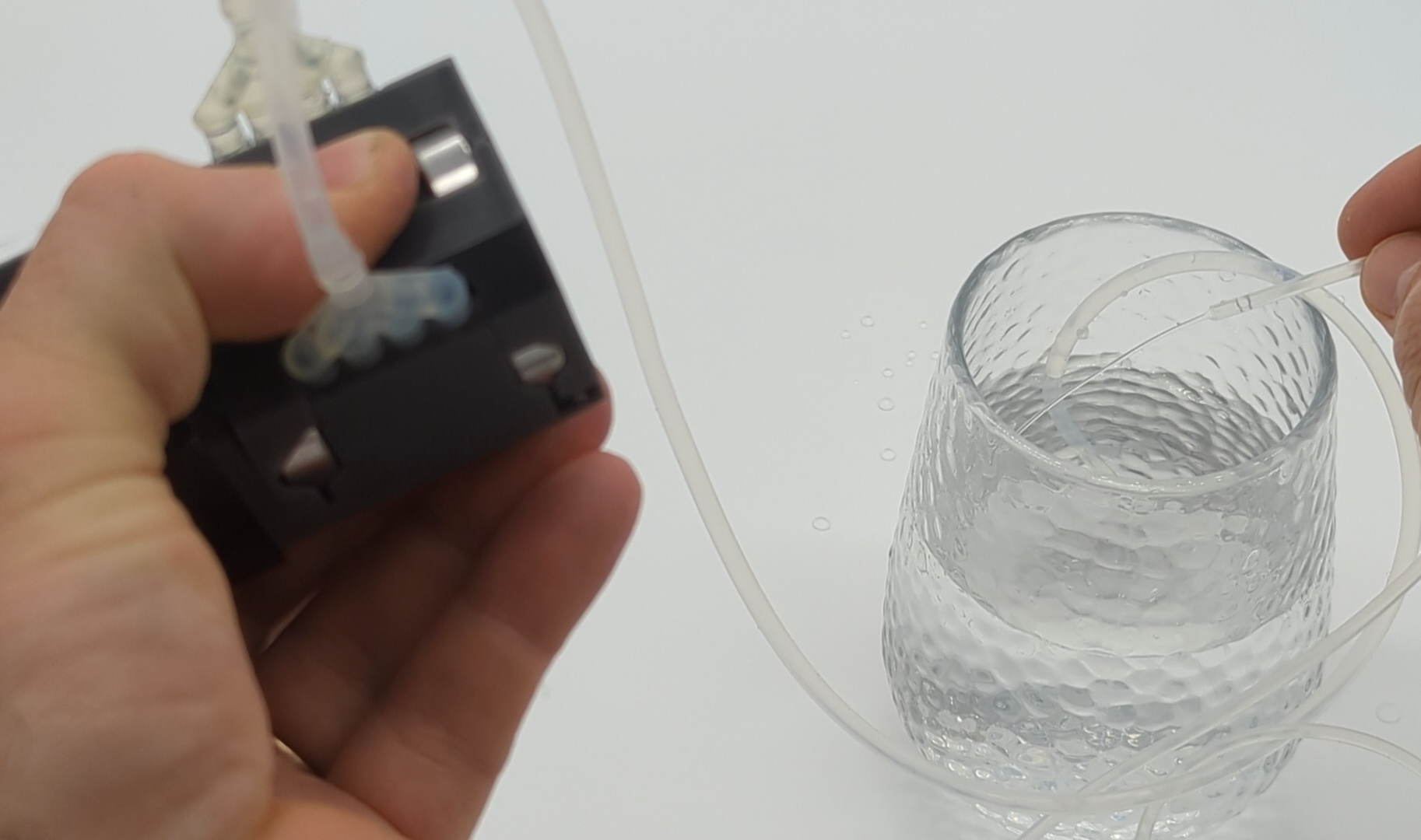
A few learnings to leave you with since you've made it to the end :)
1. Iterative design is powerful. My favorite design process is rapid turn, iterative development. It's a heavy lift each time you make a brand new part, but if the design was structurally sound, you can really build on even rudimentary starting points.
2.Documentation and clear naming conventions! Wow, making so many similar small parts which in some cases were visually indistinguishable gets confusing fast. Even though marking parts, or even individual features can take time (done in CAD, on the printed part with a marker), it pays for its self with clarity and saved time looking for a specific component.
3. Engineering is Art. Although engineering isn't typically considered an artistic pursuit, it can be a cathartic expression of beauty and passion.
“Nothing useless can be truly beautiful”
~William Morris
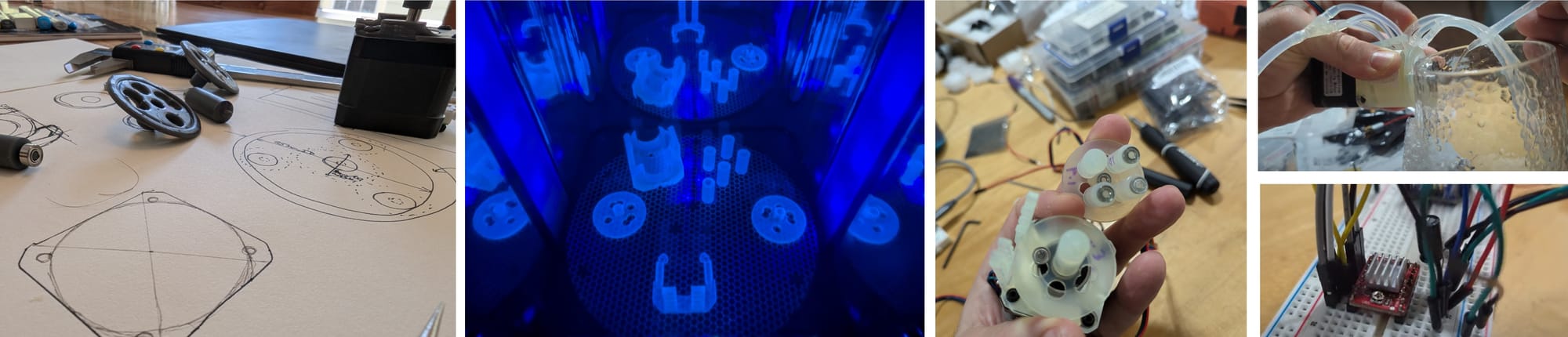