Product 6: Anatomically Customized 3D Printed Pack
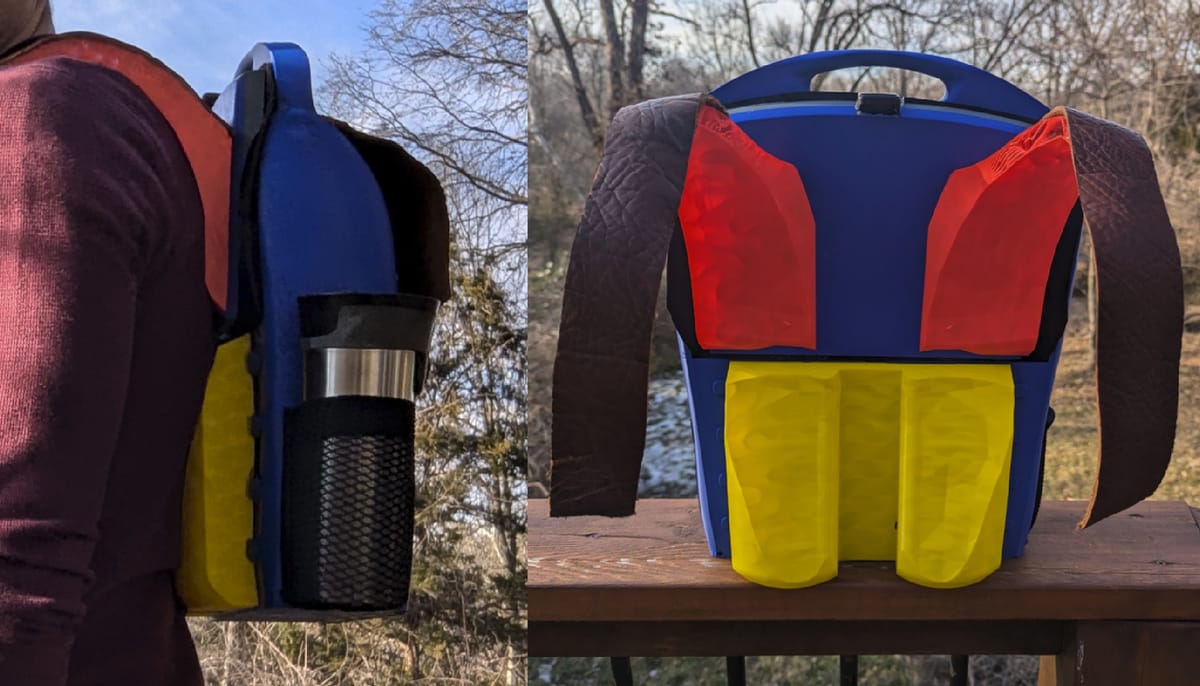
Do you have an idea or project that keeps coming back to you? I've been drawn to backpack concepts with printable, machined and/or customizable features for over a decade. This month's chapter yielded a mix of wins and failures--par for the course in time constrained, iterative product development.
Wins:
- A workflow for generating and converting a 3D scanned model of my body into customized printable shoulder straps and back cushion.
- Effective ways to permanently mate tensioned fabric to a rigid frame.
- Design and print of flexible, low density structures.
Fails:
- Didn't finish this newest version of the backpack in time for my trip to Mexico.
- An ironically uncomfortable set of customized cushions.
- Significant overwork between my regular business, this month's project, and a new start up I've cofounded that's courting VC investment.
Backstory

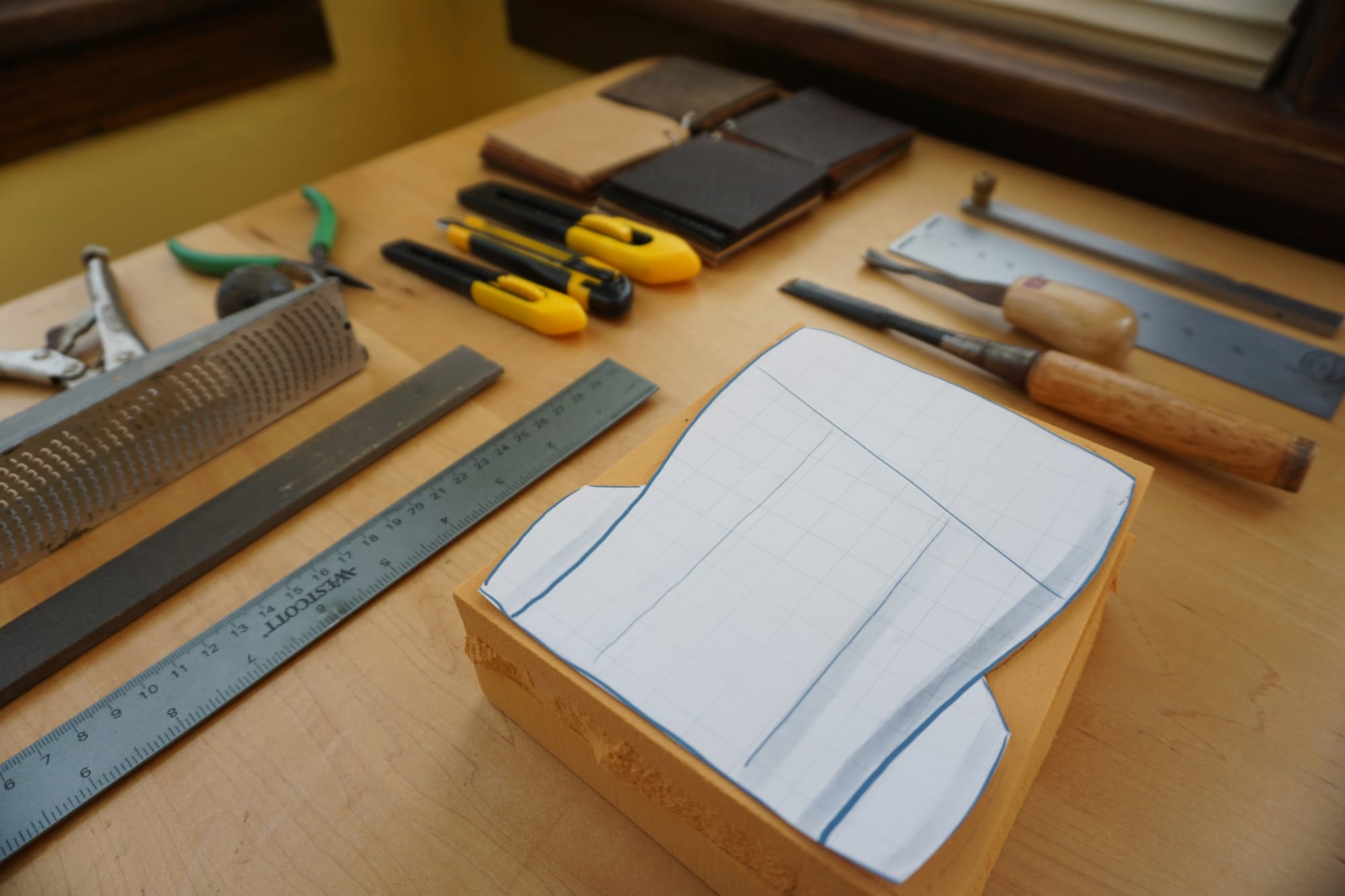
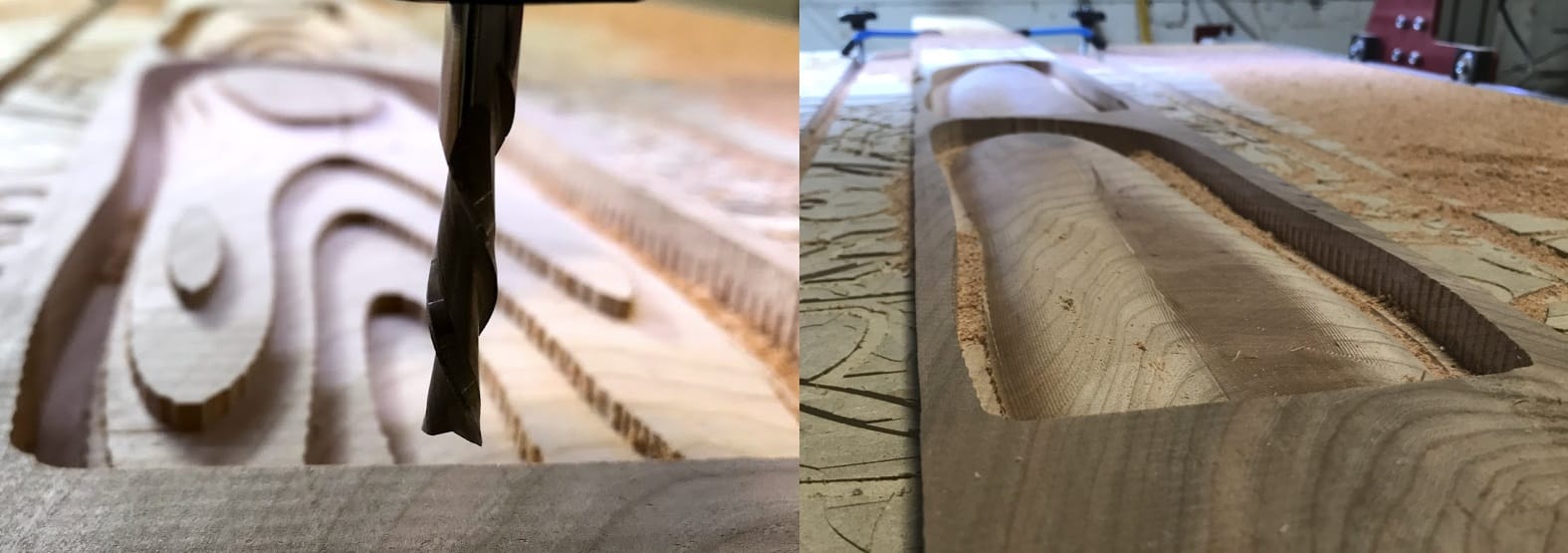
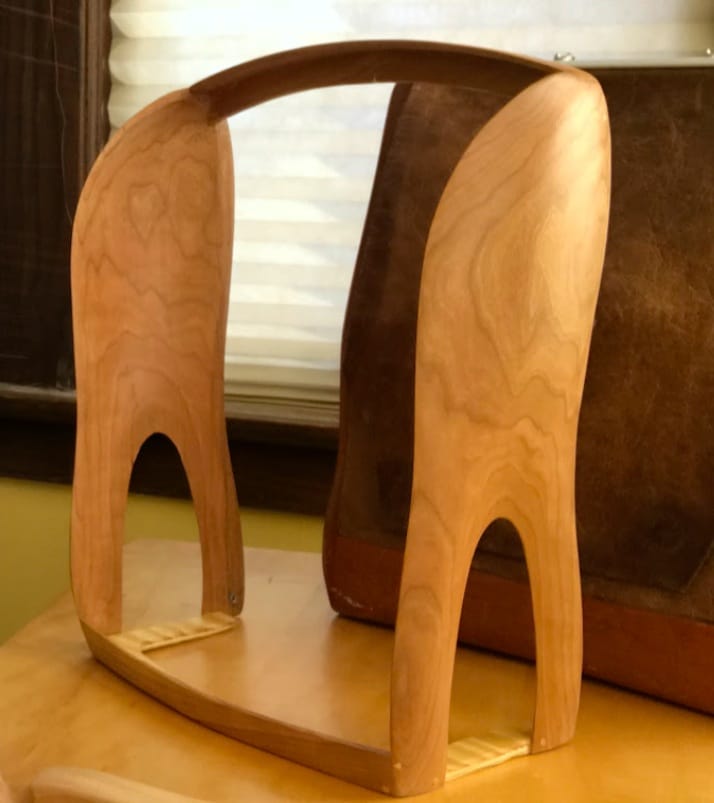
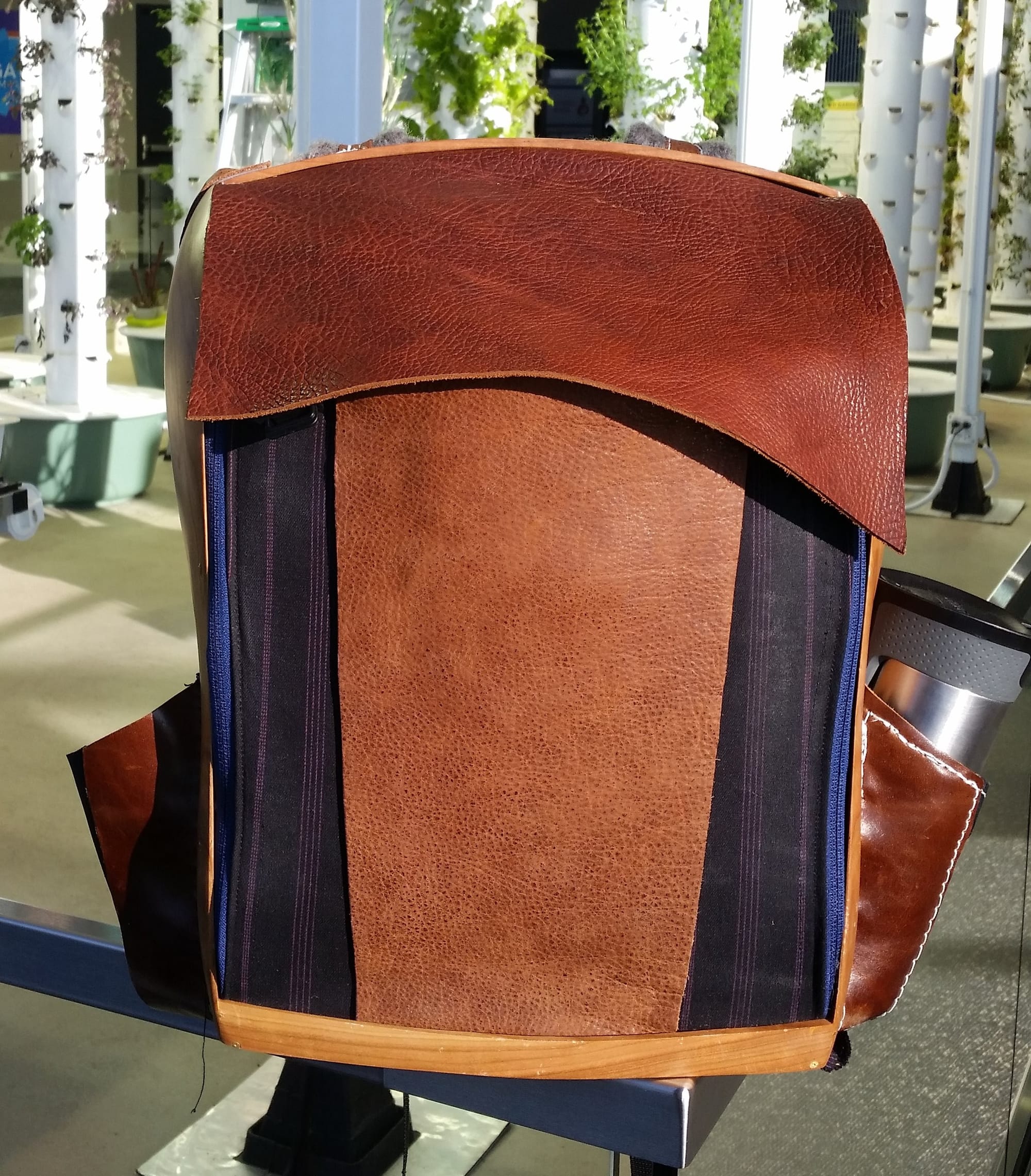
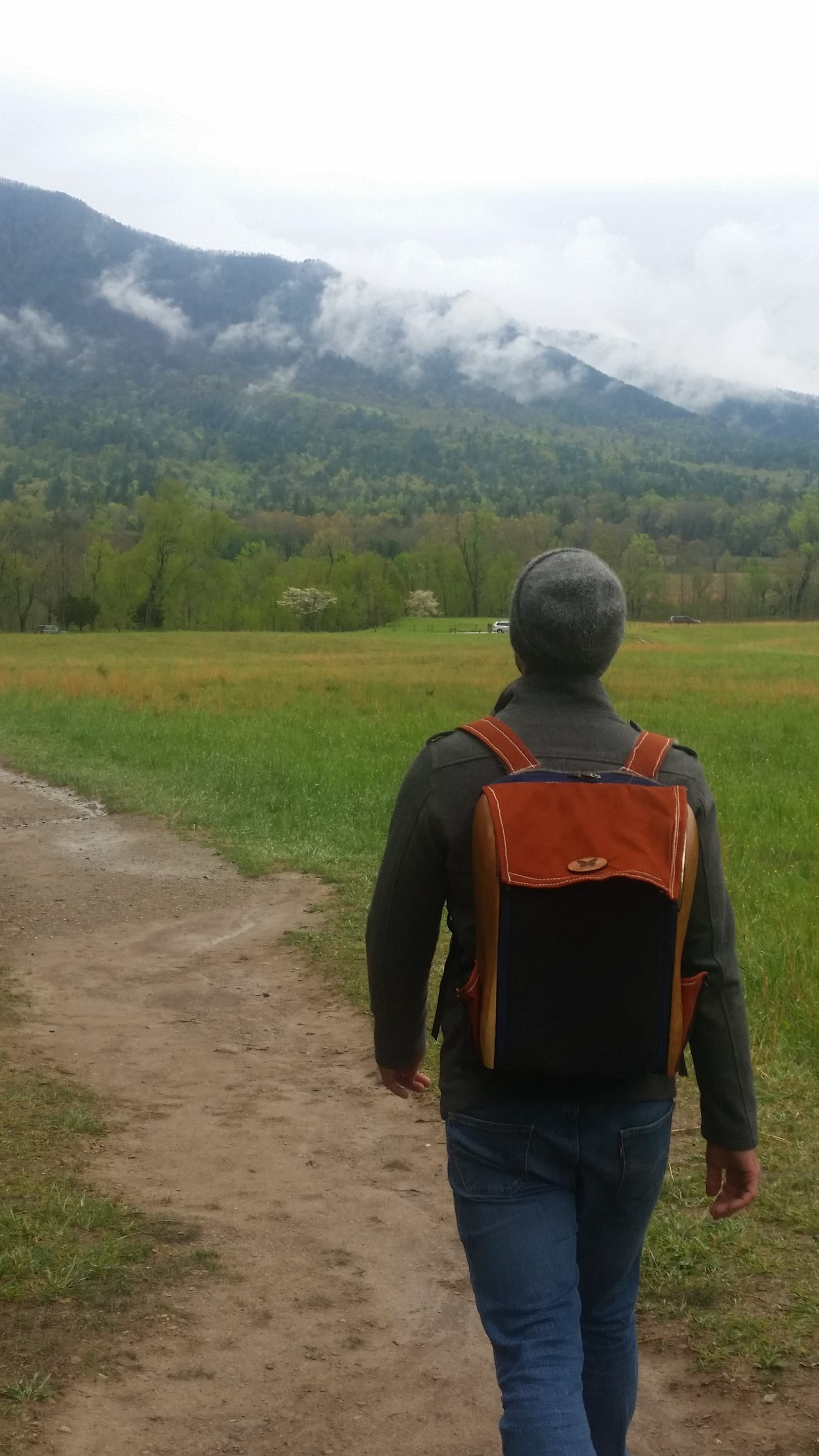
2017: My first build-in-public project with a group of best friends. We converted that first wood and leather backpack into a lighter version with CNC machined wood sides and the intent to manufacture for sale.
This month's concept
A small, daily carry backpack with printable structures including anatomically customized cushions, straps and main body.
I started with a 3D model of my body captured with Zozofit and imported to SolidWorks.
Next came an exploration of infill geometry and TPU test prints. This video shows gyroid infills at 5% density(right) and 2% density(left).
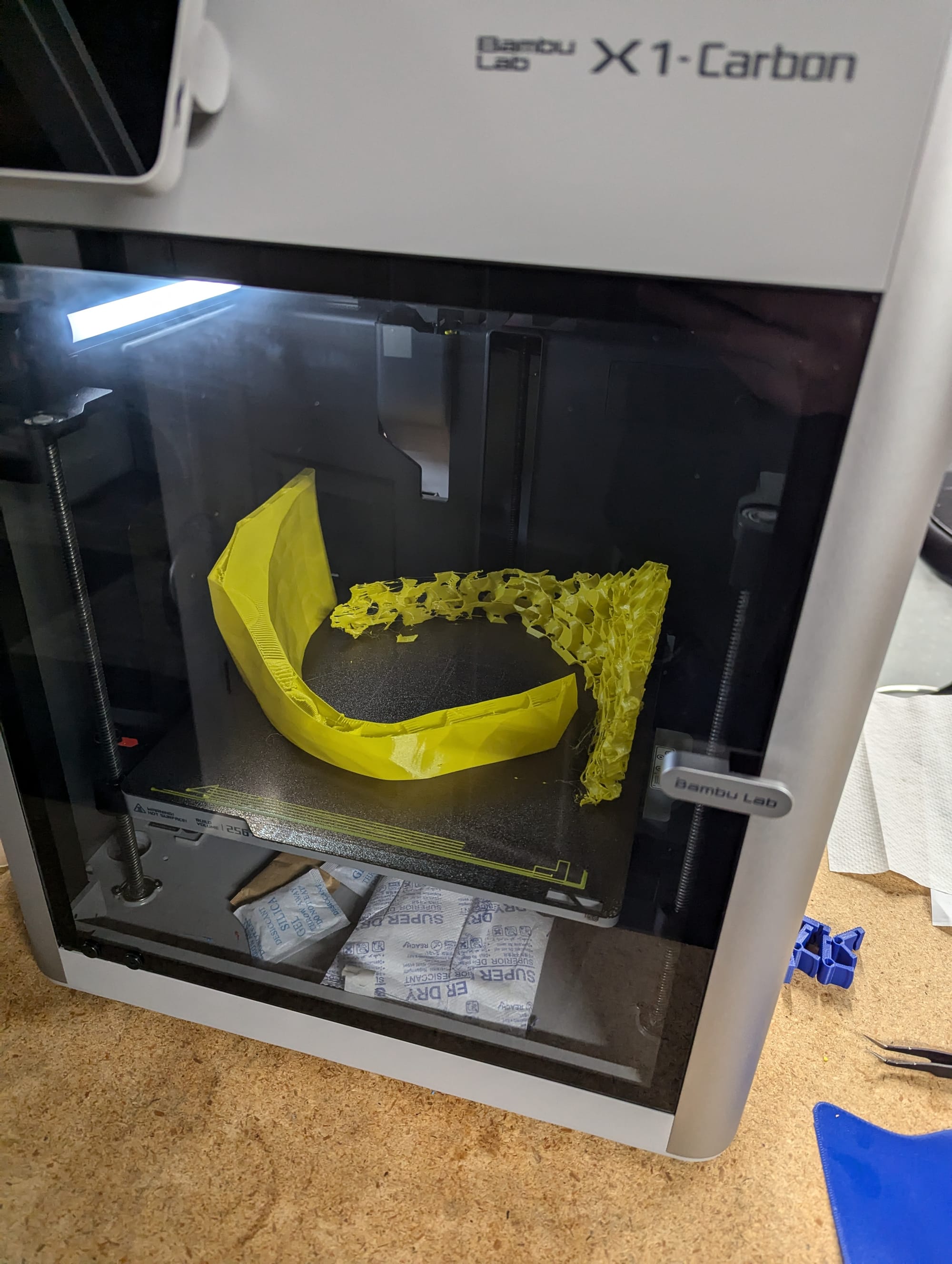
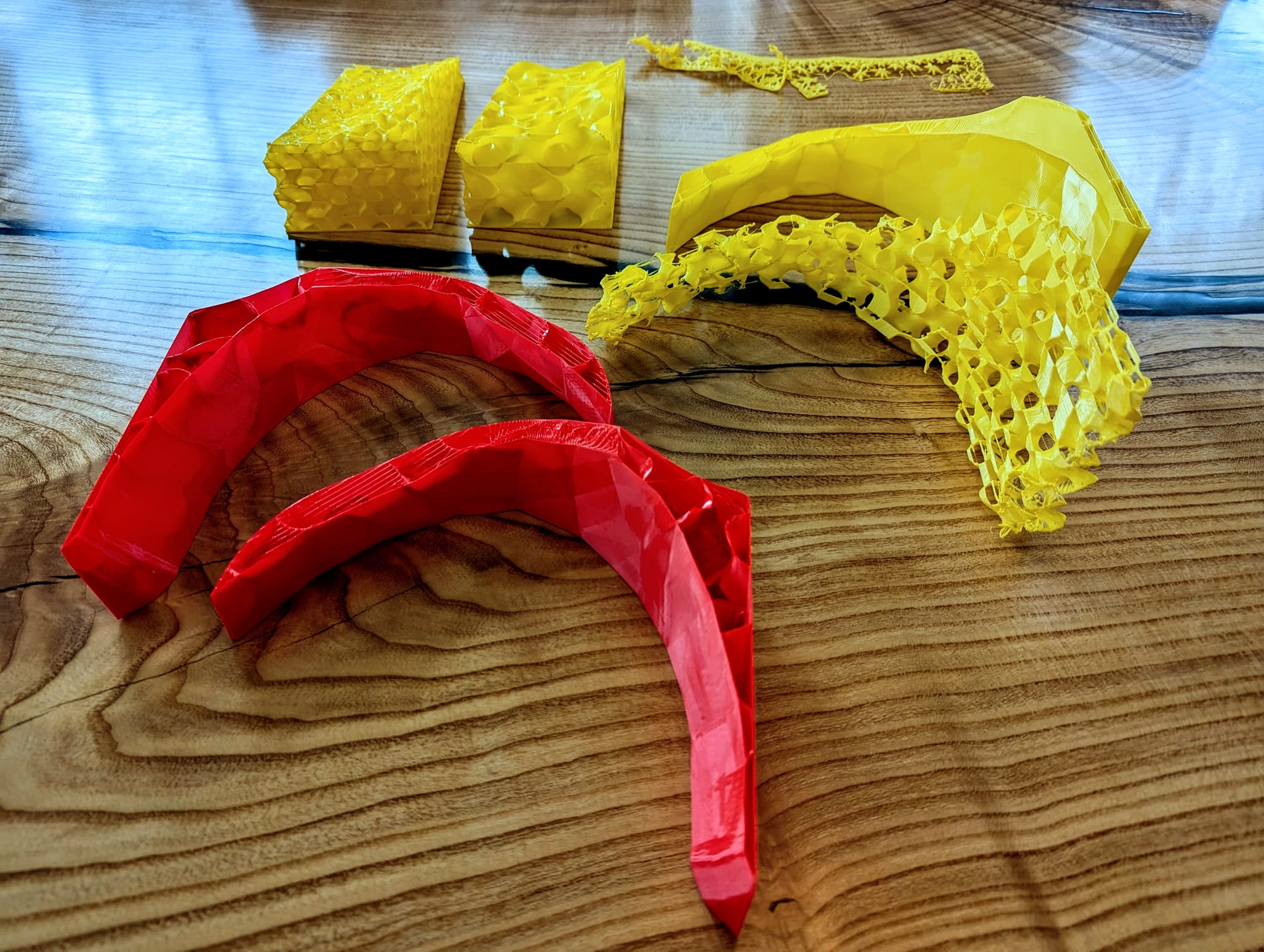
Additional cushion tests in yellow and red BambuLab AMS compatible TPU.
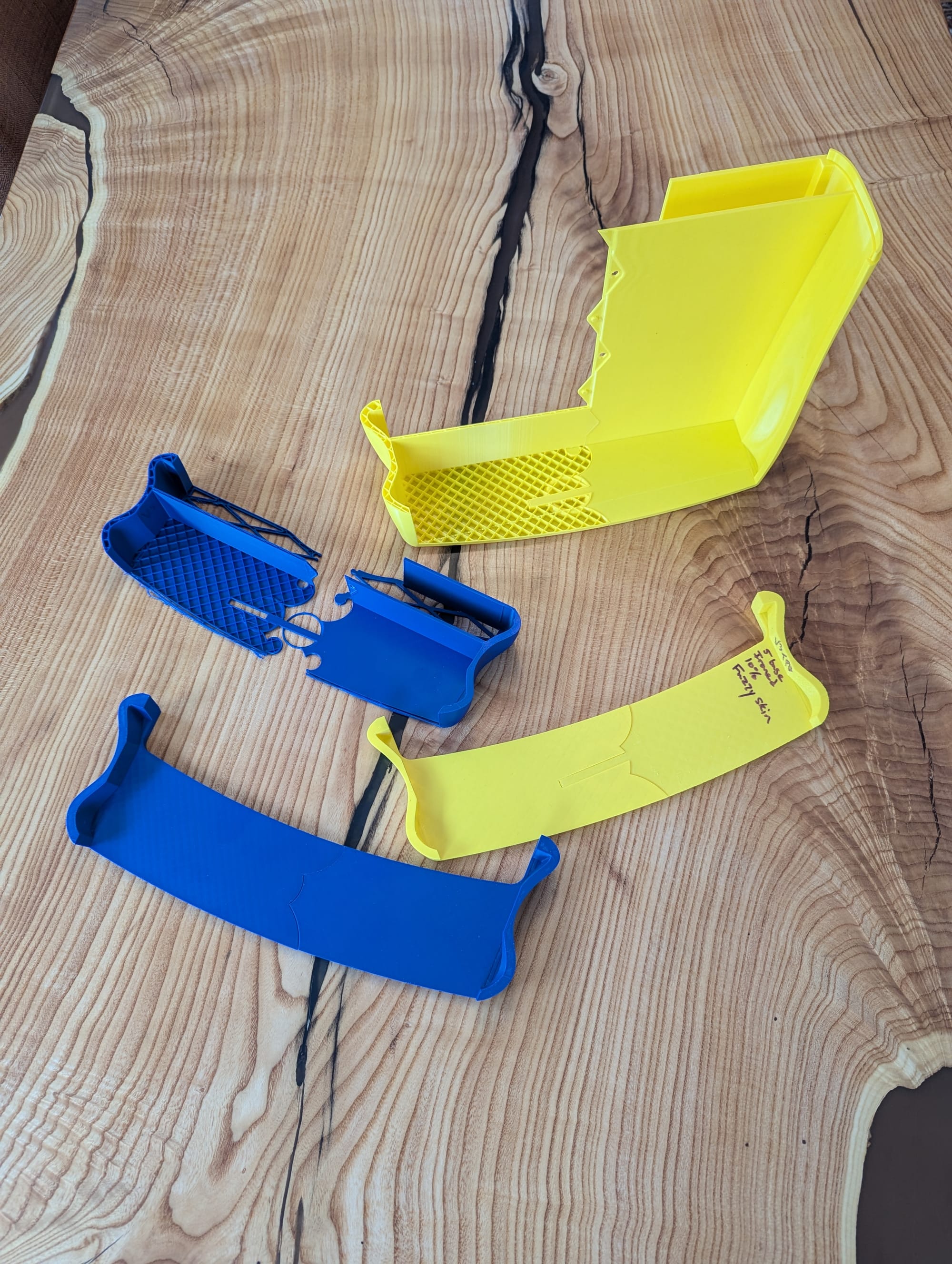
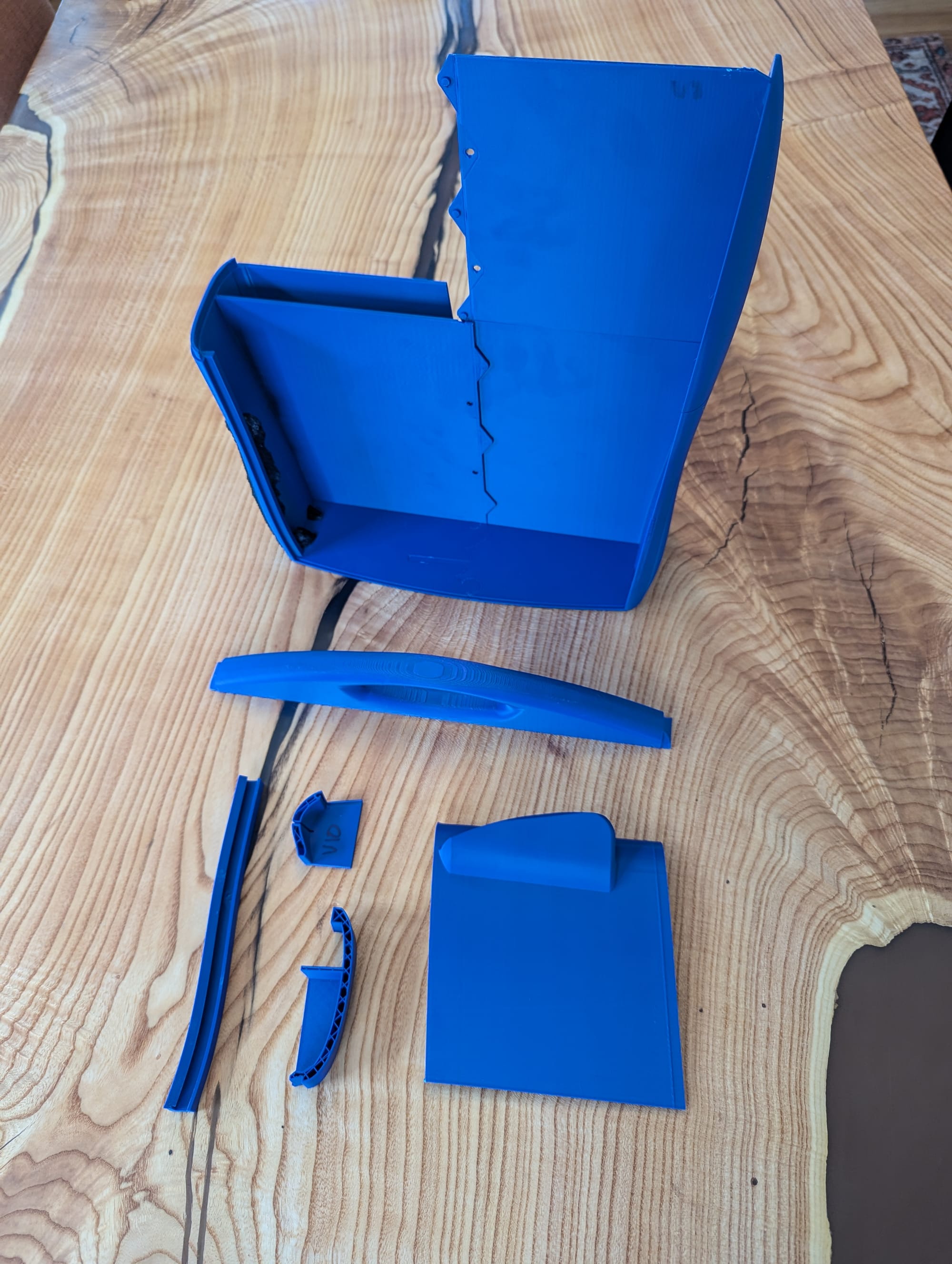
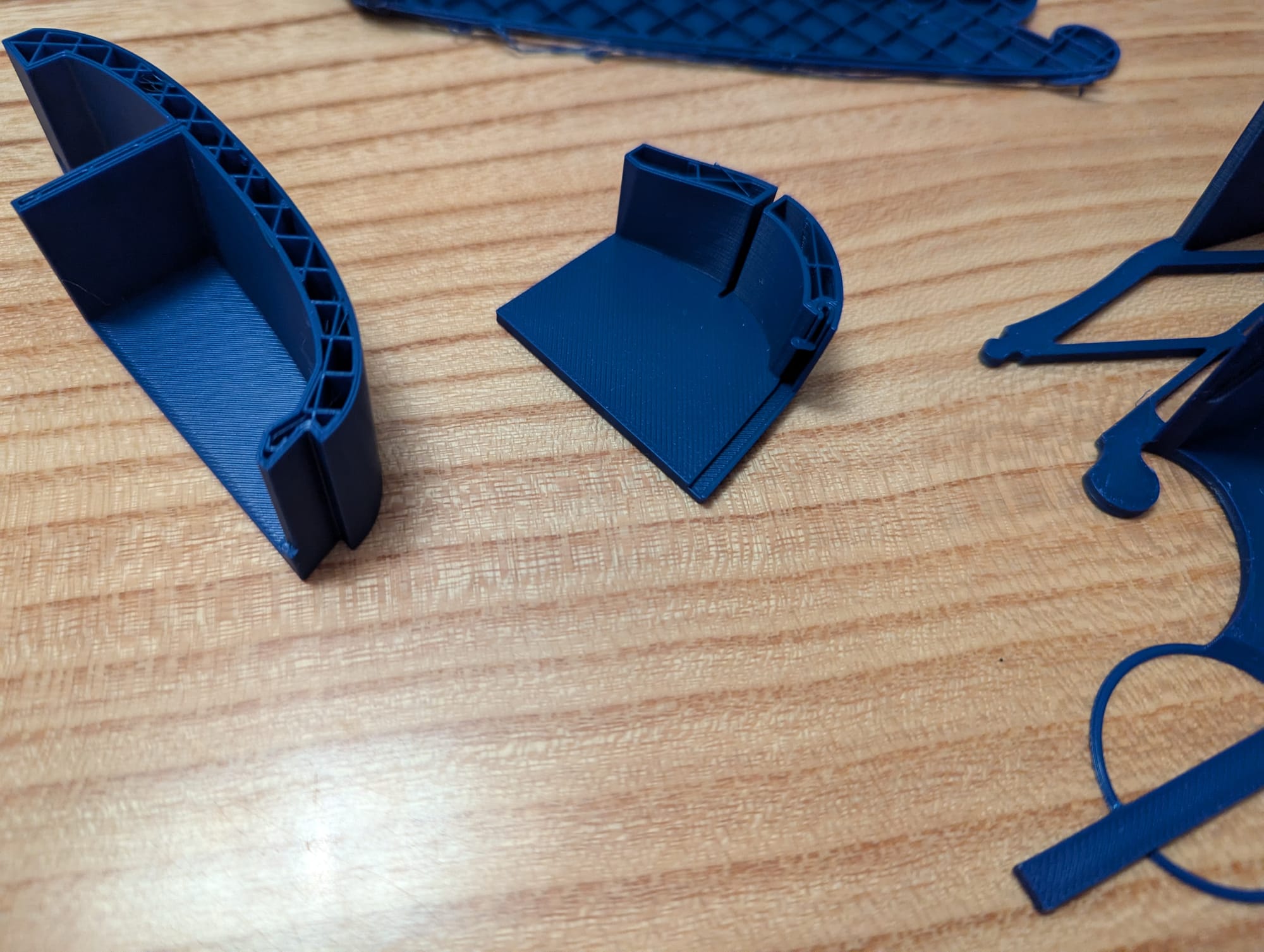

Iterative design of components starting small and getting larger to ensure fit and function. Blue parts printed in Bambu Lab PETG HF.
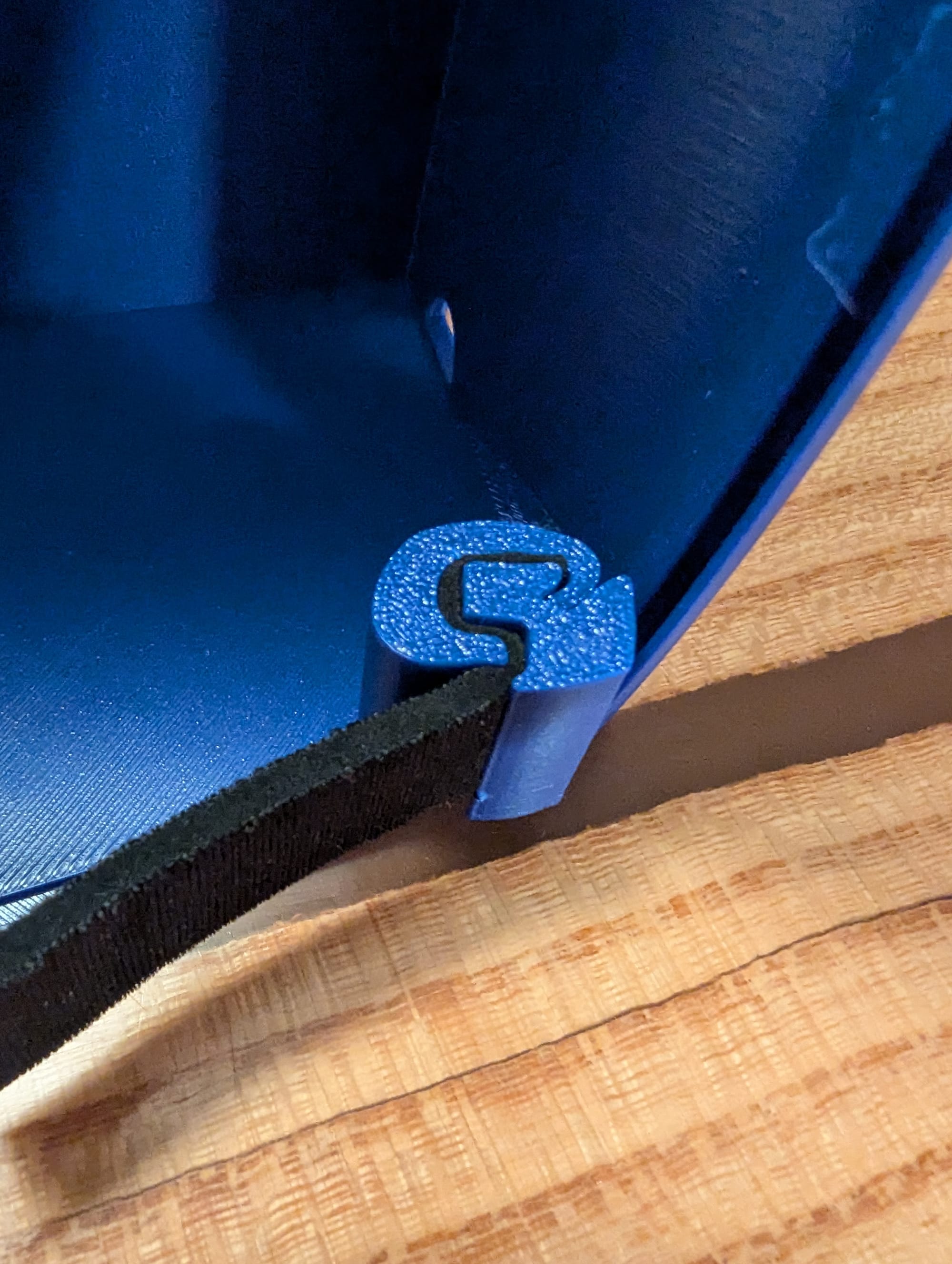
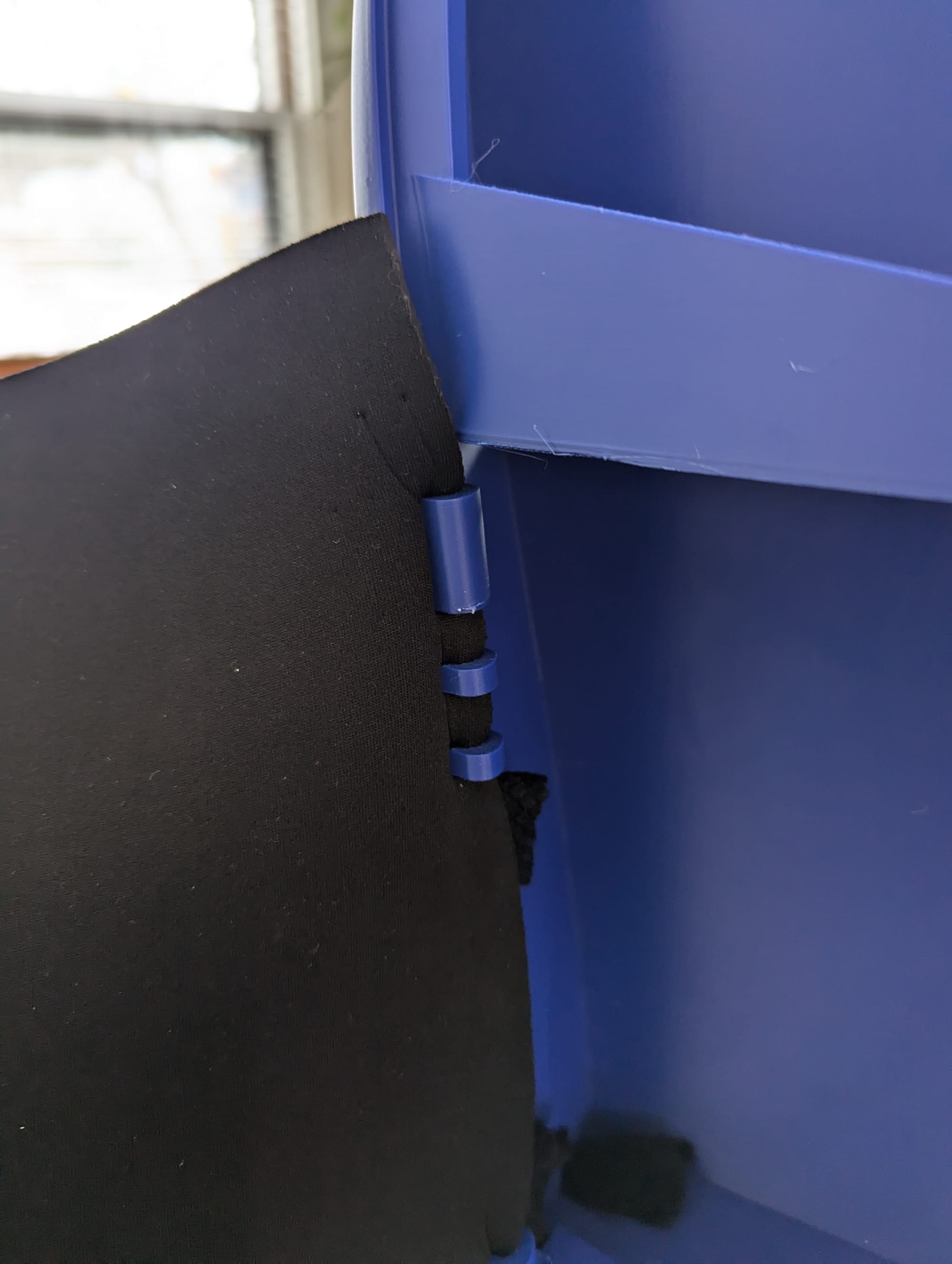
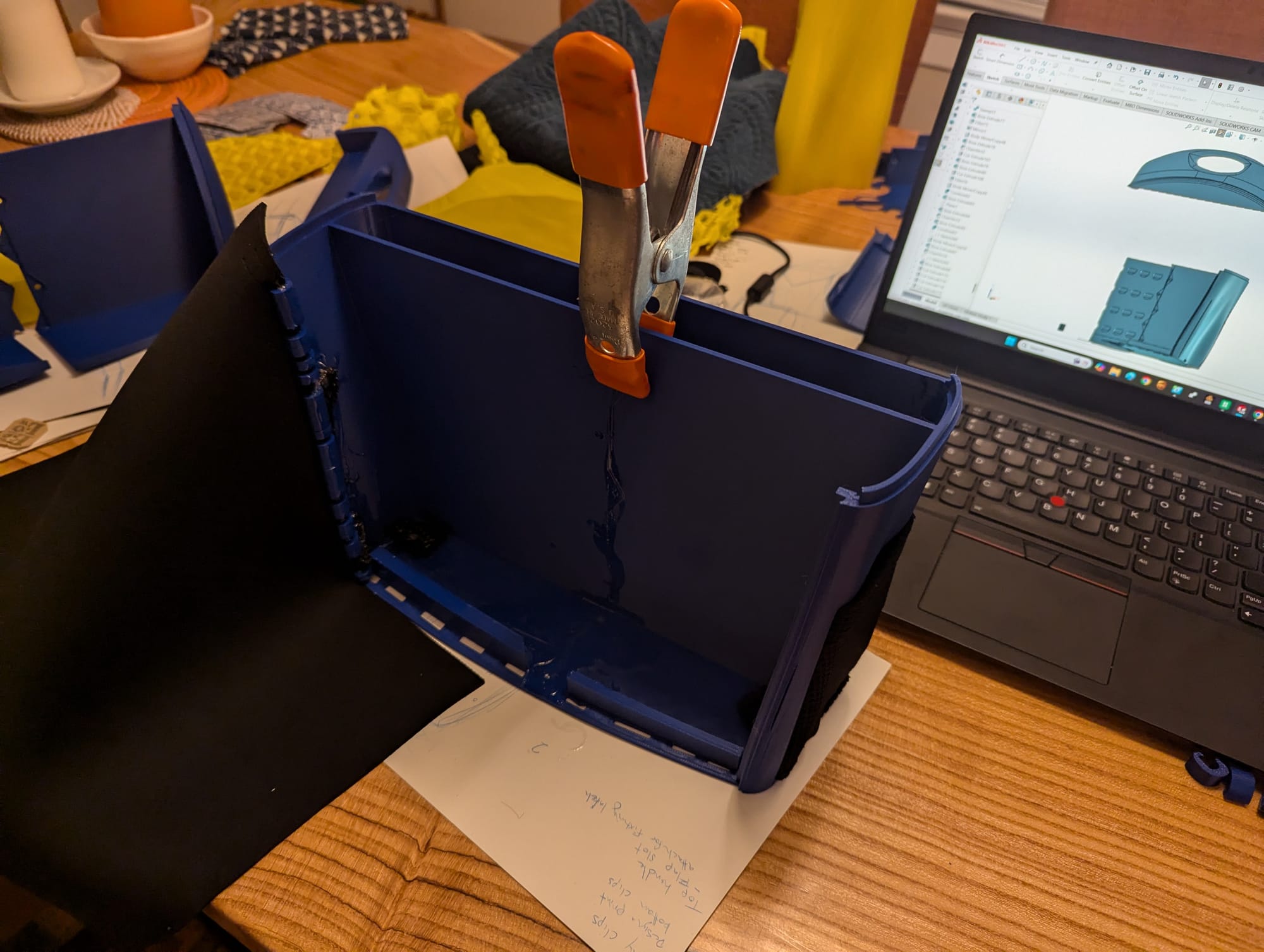
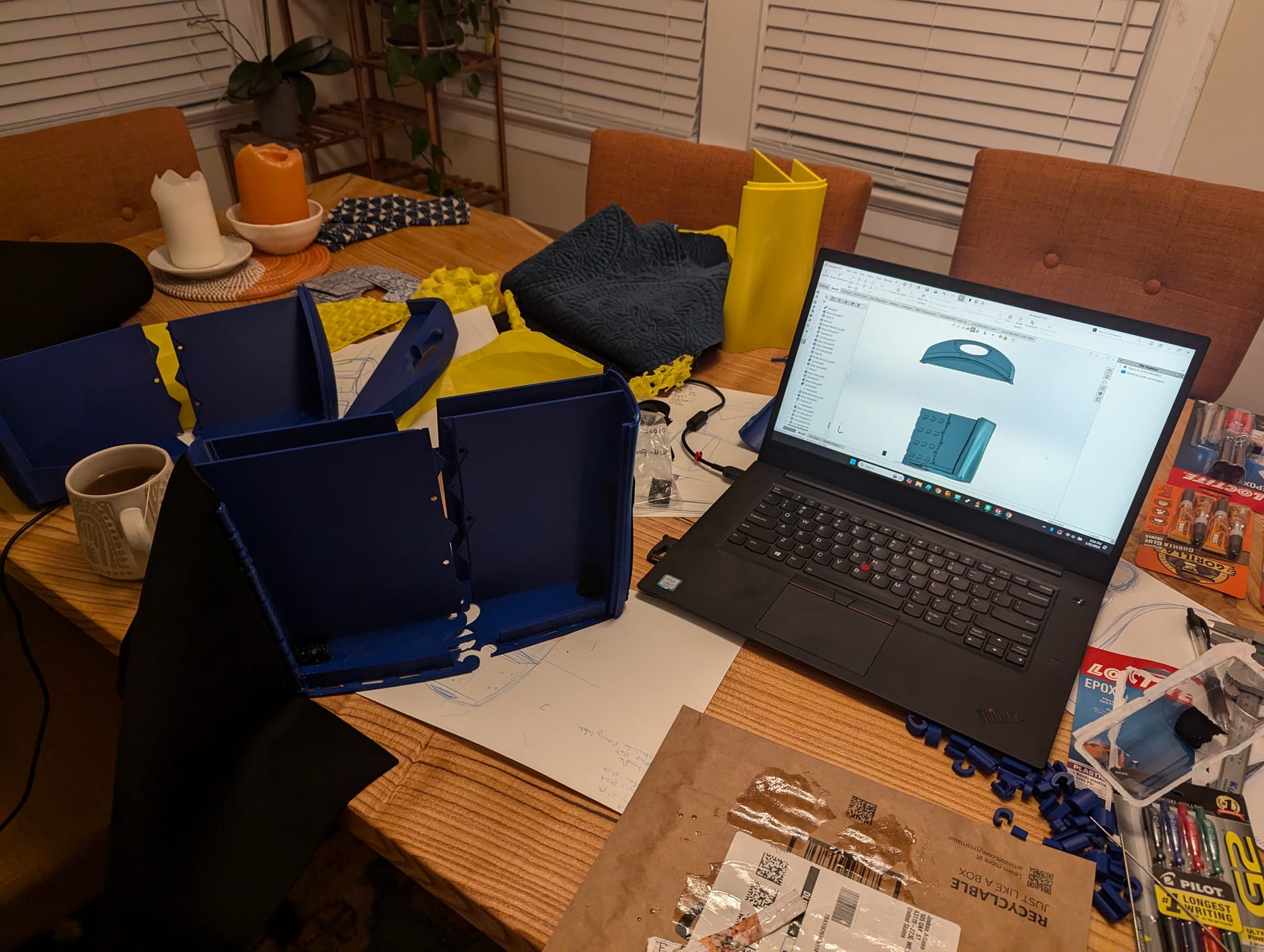
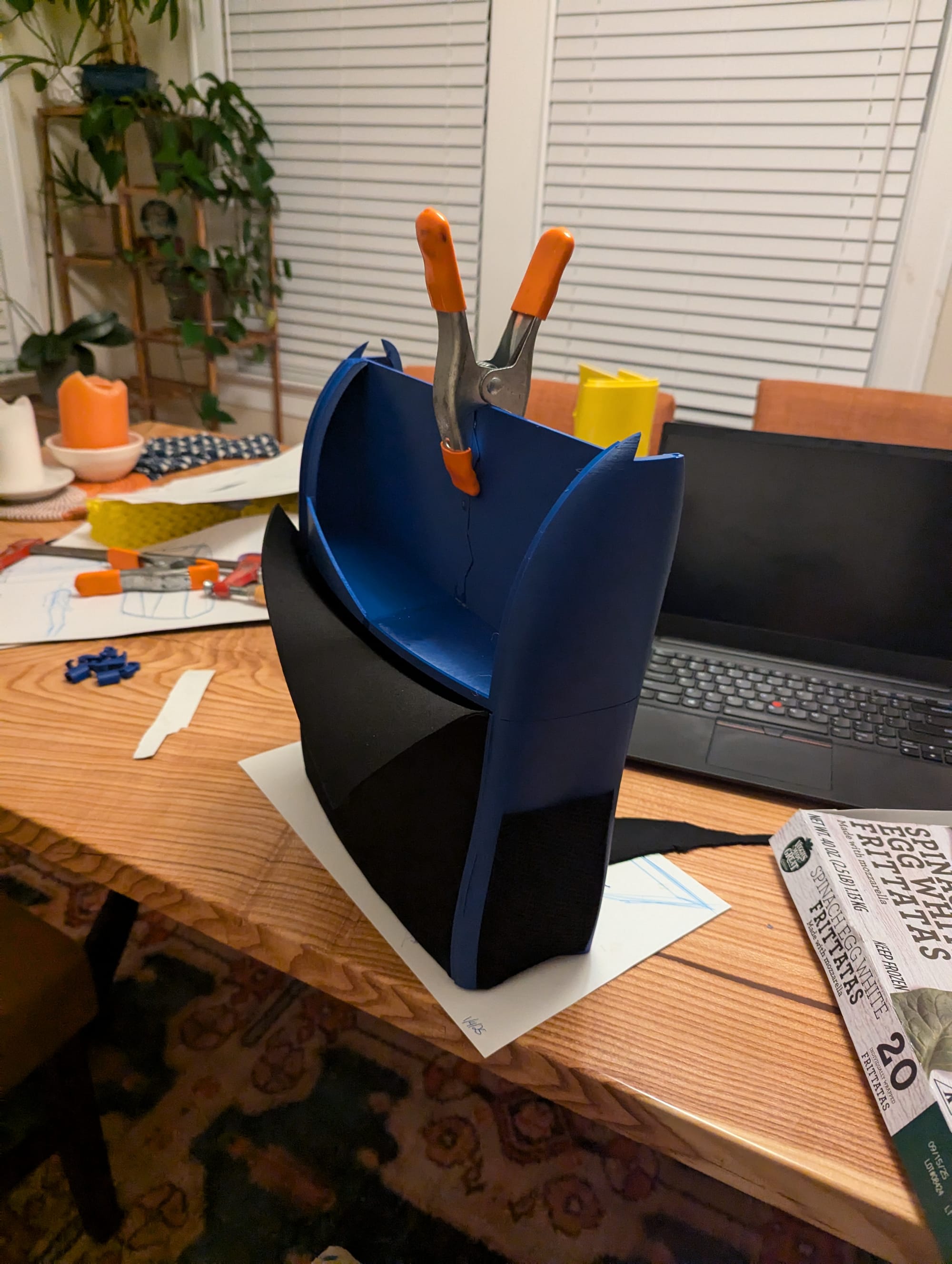
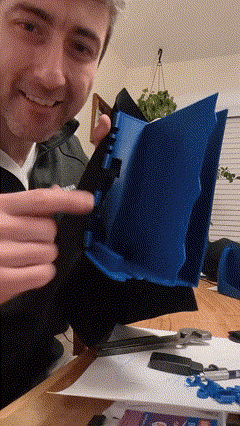
After the week and a half of designs, test prints, and extra work priorities popping up, assembly was coming down to the wire--starting around midnight with a 7:55am departure time for the airport.
I did my best to progress steadily without the type of rushing that costs more time than it saves. 1:00am to 7:50am were productive hours, with all remaining parts designed, printed and assembled. However, with 5 minutes till departure and the last epoxy joint still curing, it was not road ready (and far from a quality job). So, I defaulted back to my original wood and leather pack for the trip leaving the overnight work a big mess.
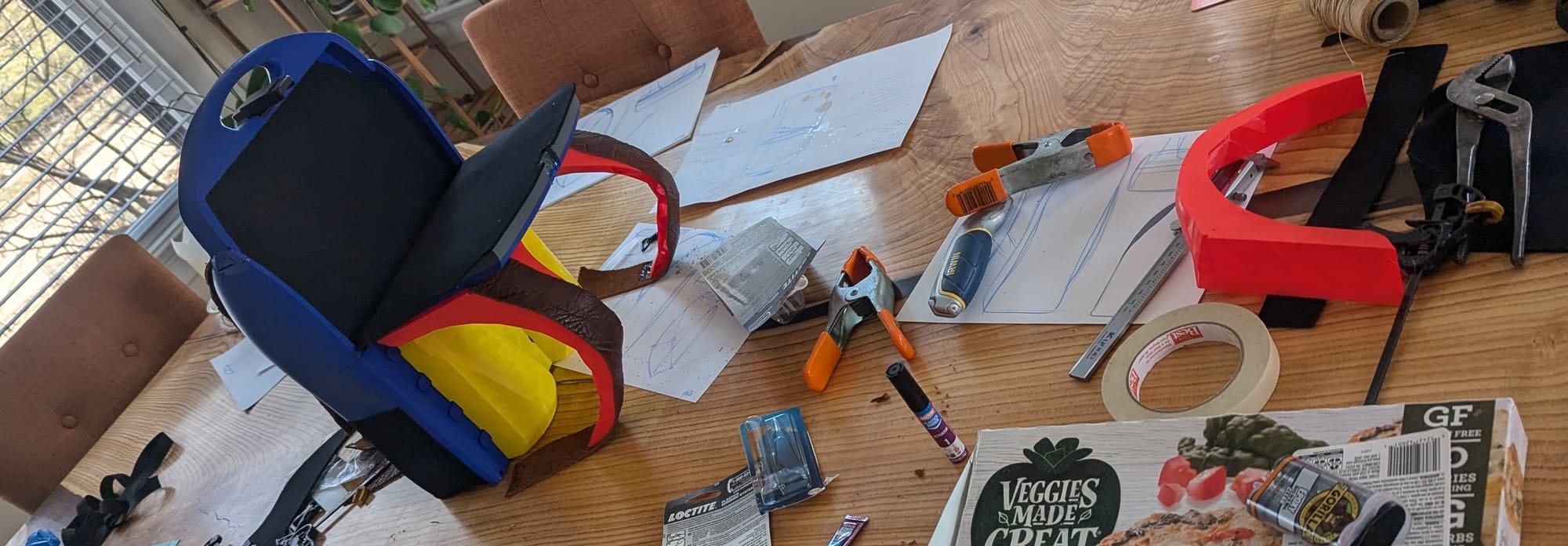
I'll leave this version in the rough (and honestly ugly) state it's in, since I like the wood sides much better, and I think more traditional cushions are actually more comfortable and functional. With that said, it was a fun (though stressful due to time constraint) project for the month. My largest take-away is actually around work scoping and how much better my life is when it's invested in work that doesn't come down to the wire.
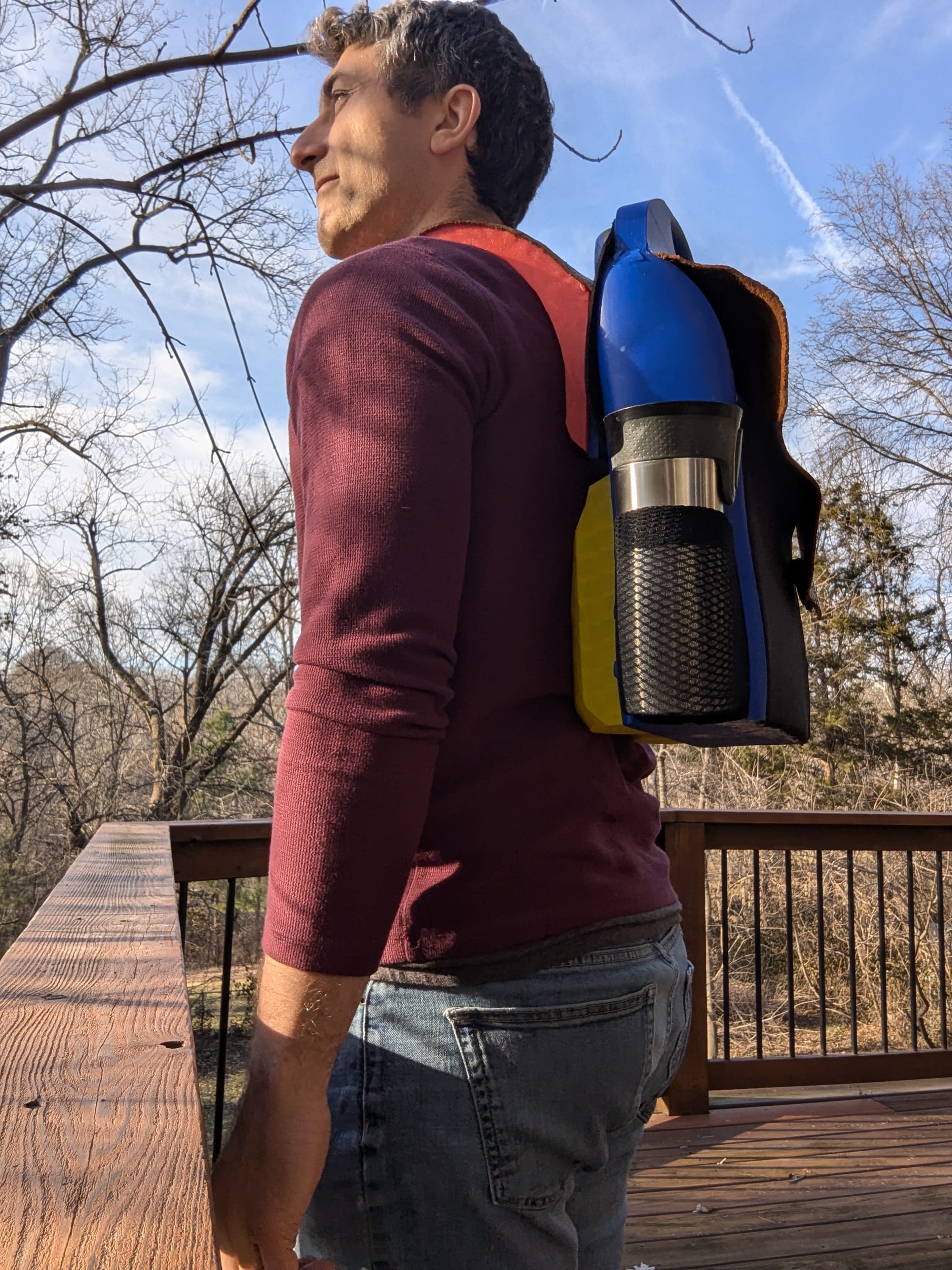
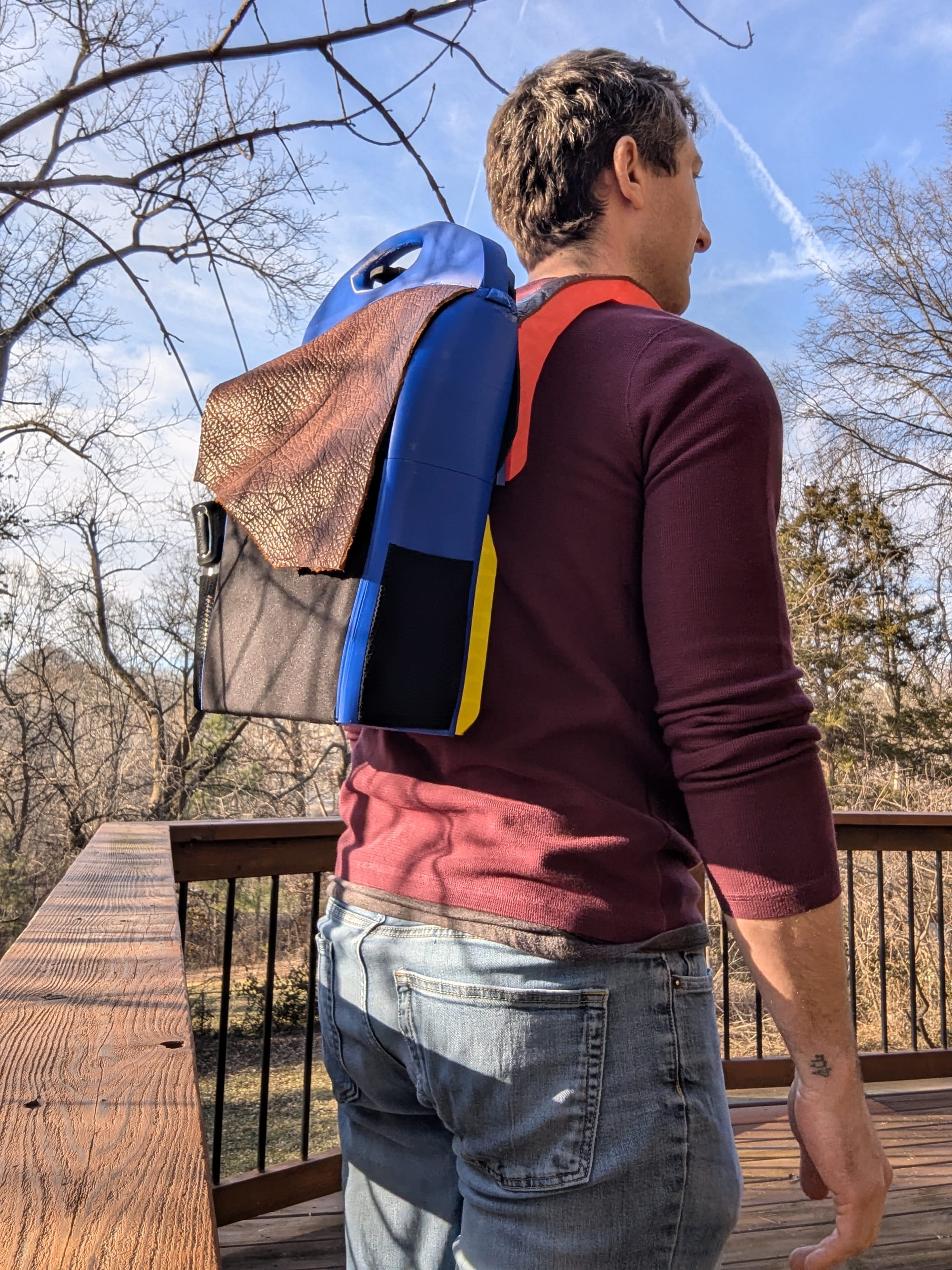
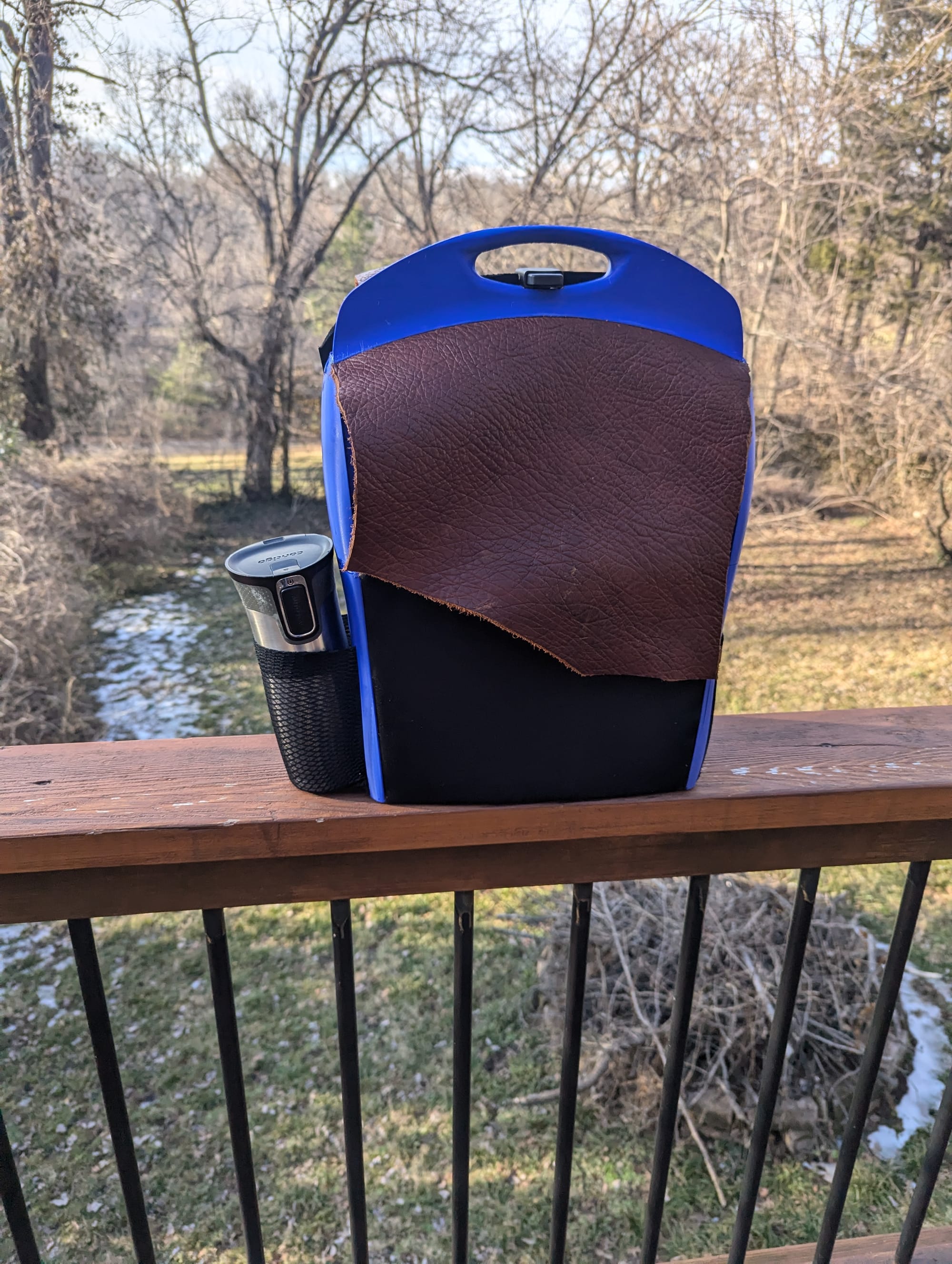
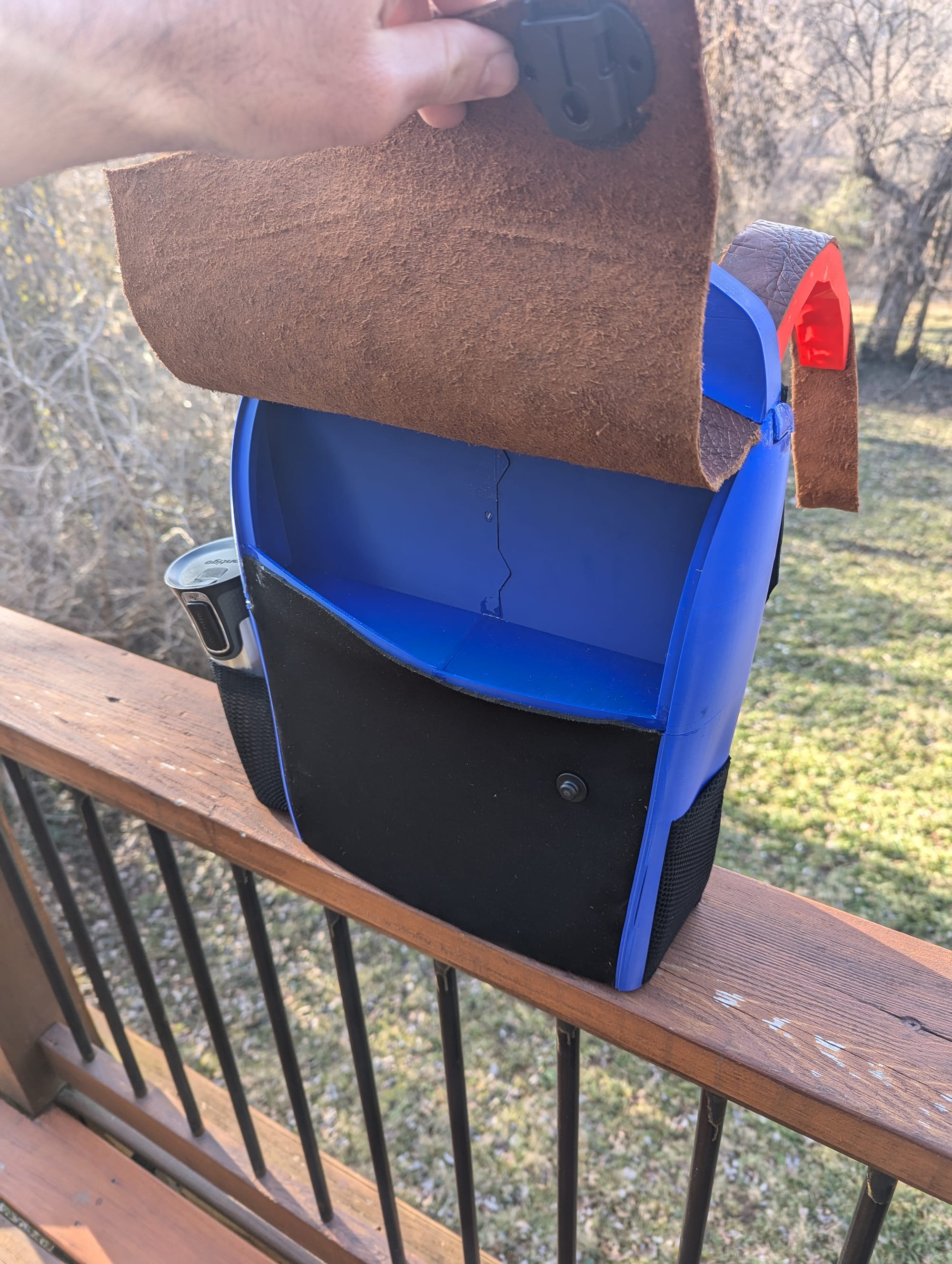
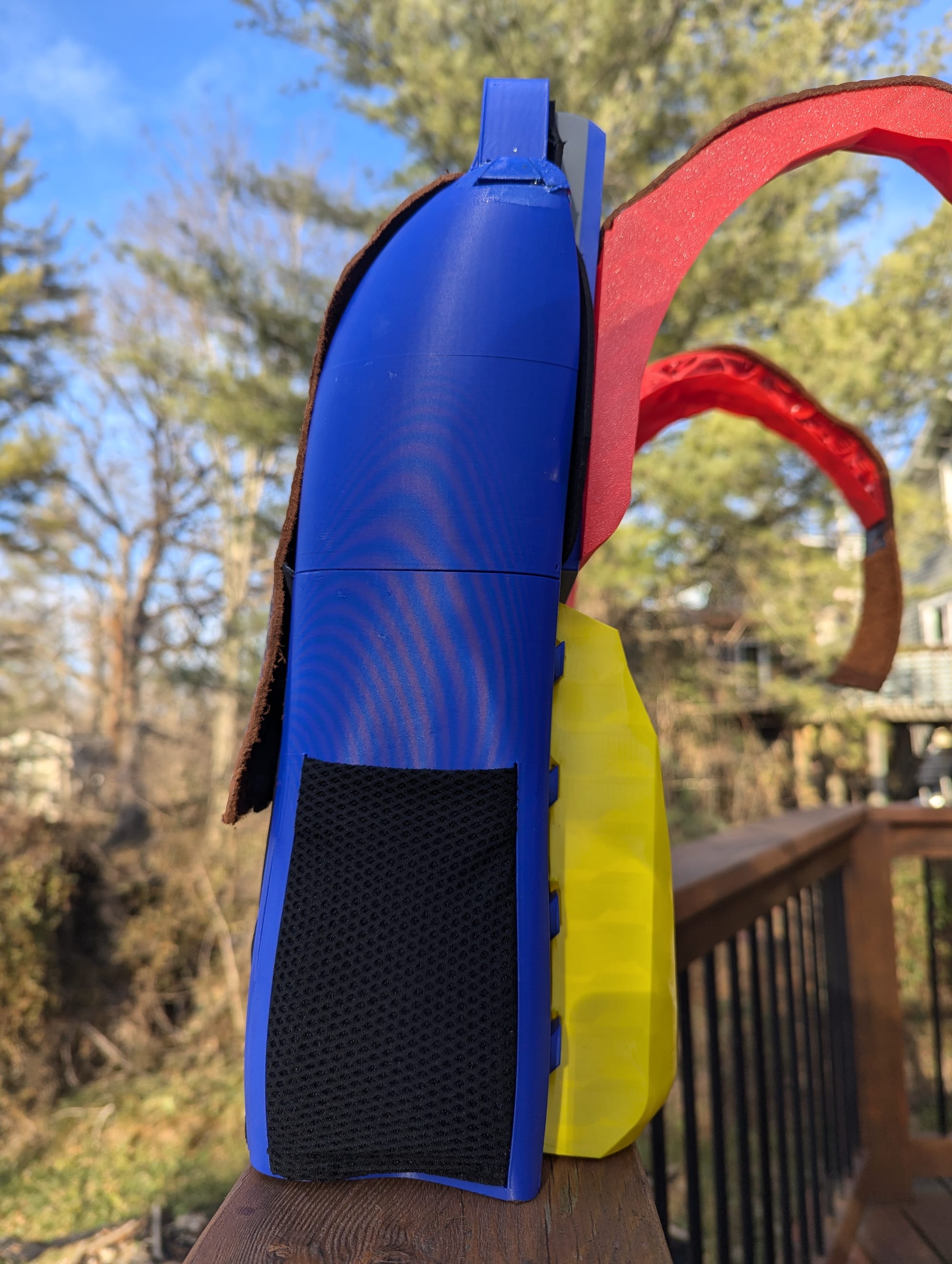
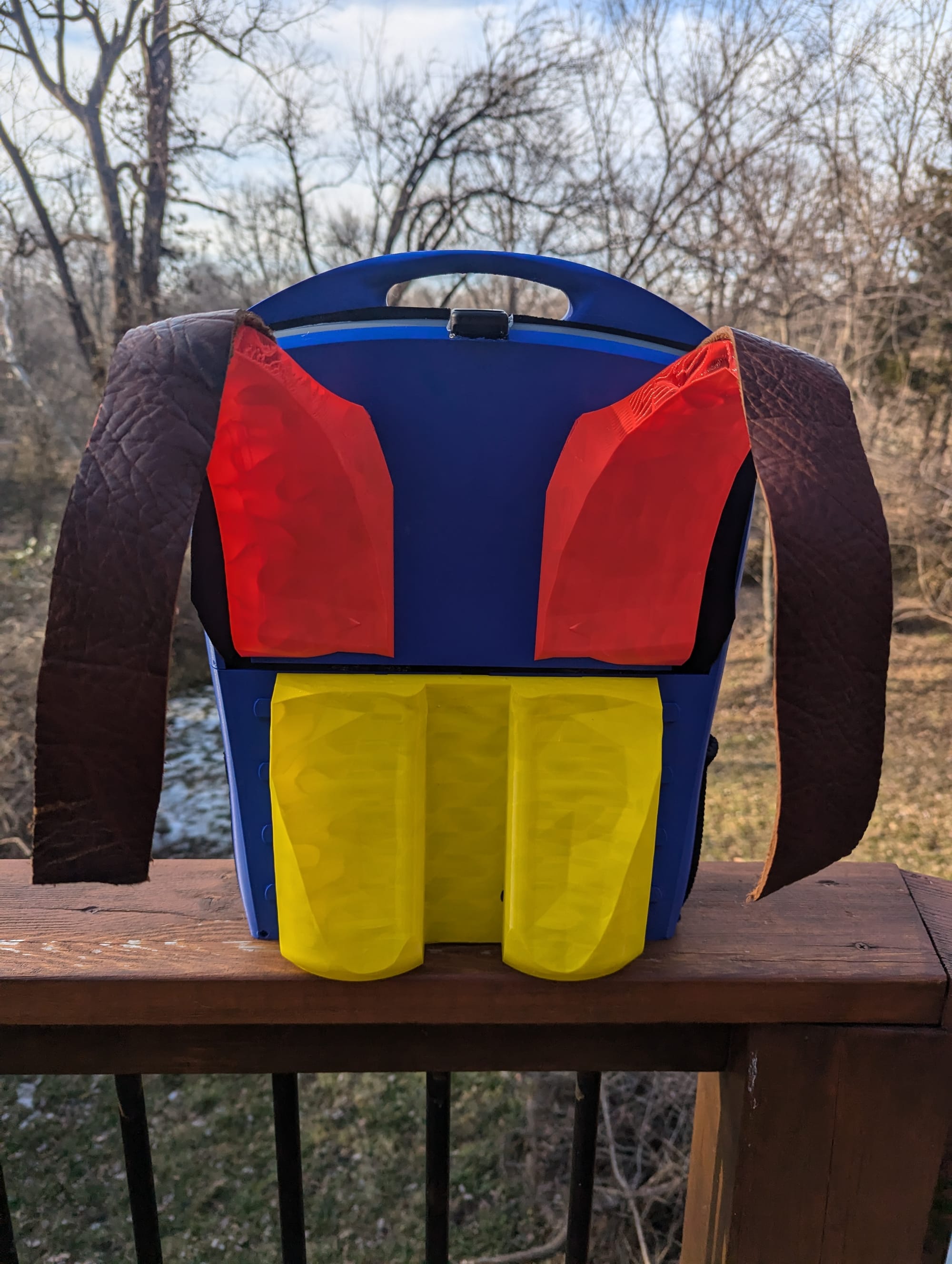
Feel free to reach out to me at Josh@JoshAdams.io if you have interest or needs in custom backpacks, or anatomically personalized projects. I'd love to hear from you and learn about what you're working on.
Since you made it this far, here's the very first bag I made in 2012 with another best friend. Concept for 3d printable custom pockets (perforated stainless steel with cherry sides and faux leather insert)
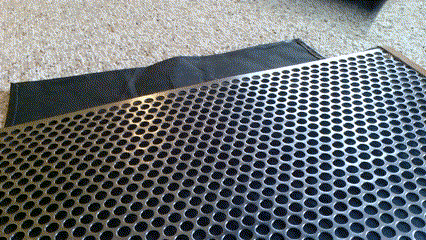