Product 8: Custom Molds for Flex Silicones & Urethanes
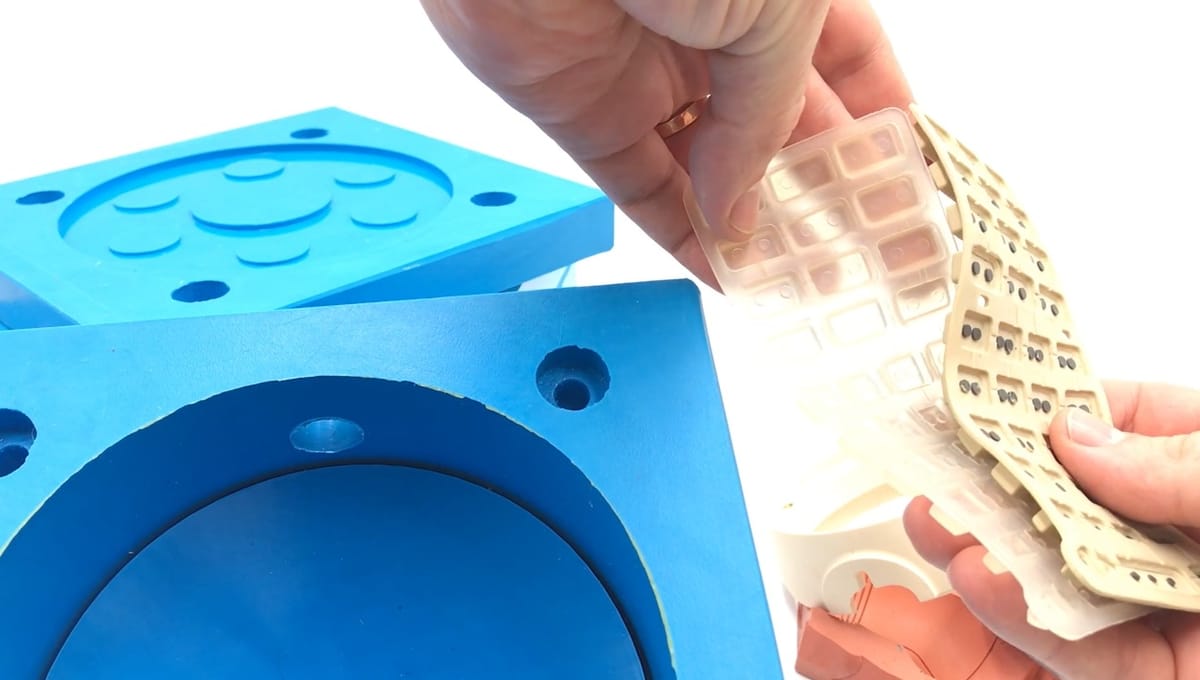
Additive manufacturing/3D printing (AM) is a powerful tool—no doubt about it. Even with all the progress in material options and cost efficiency, AM still often struggles with surface finish and geometric precision, especially for flexible materials.
Room Temperature Vulcanizing (RTV) thermoset resins, such as certain silicones and polyurethanes, are two-part liquid polymers. When these parts are mixed, they cure into durable solids—often within minutes or hours. Casting these materials can offer levels of precision, control over finish, and a WIDE range of material properties that 3D printing just can’t yet match, particularly for larger, flexible parts.
This month, I’m offering a custom design and fabrication service for molds to cast flexible parts. This includes design and production of the tooling needed to cast your geometry in a high-performance silicone or polyurethane. In addition, I'll review your design for moldability and help you select the right material, equipment needed for molding and post processing method.
Protip: BJB Materials is my favorite vendor of RTV Silicones and Polyurethanes. Their products are top quality, competitively priced, and they have the best tech help around.
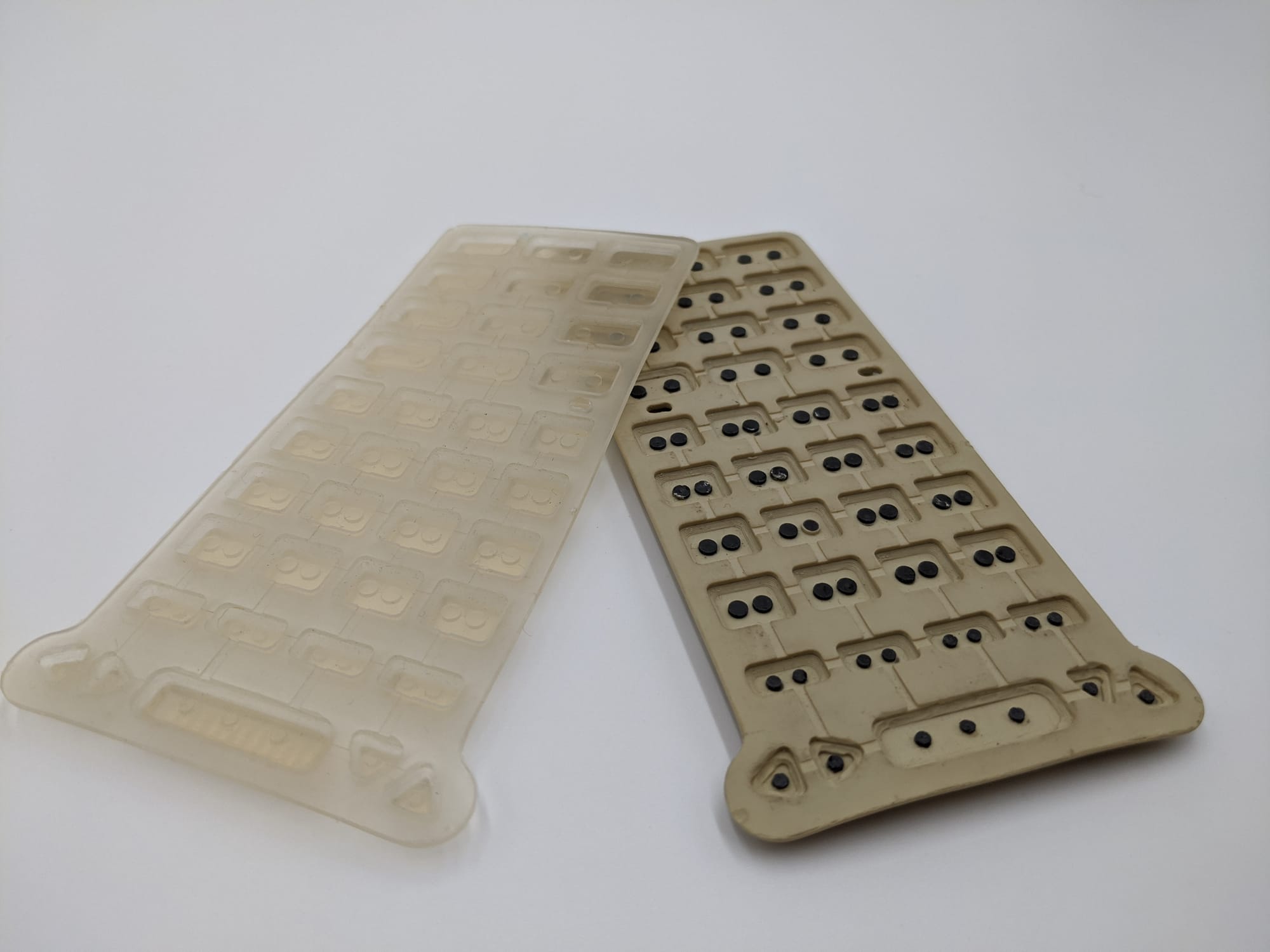
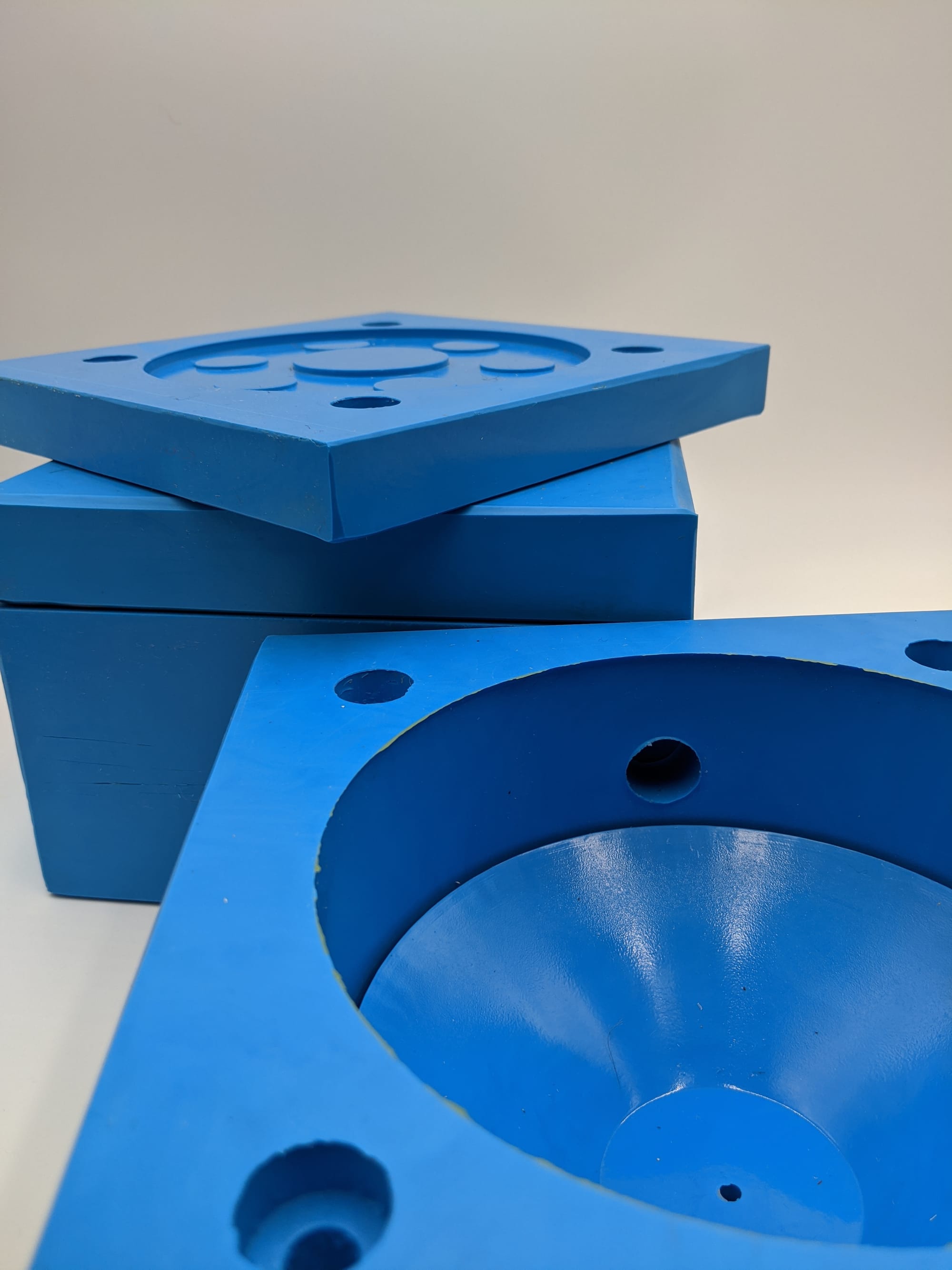
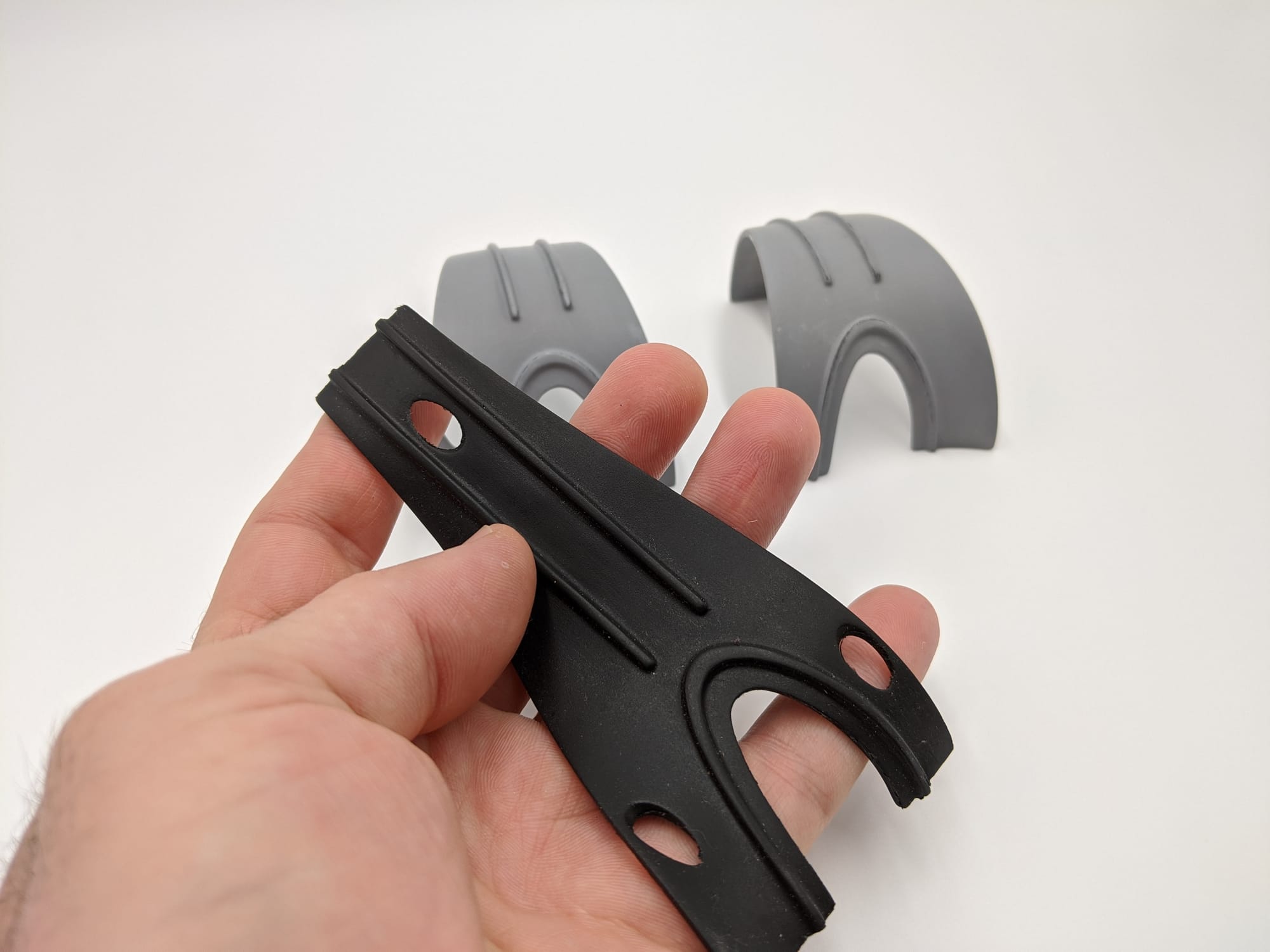
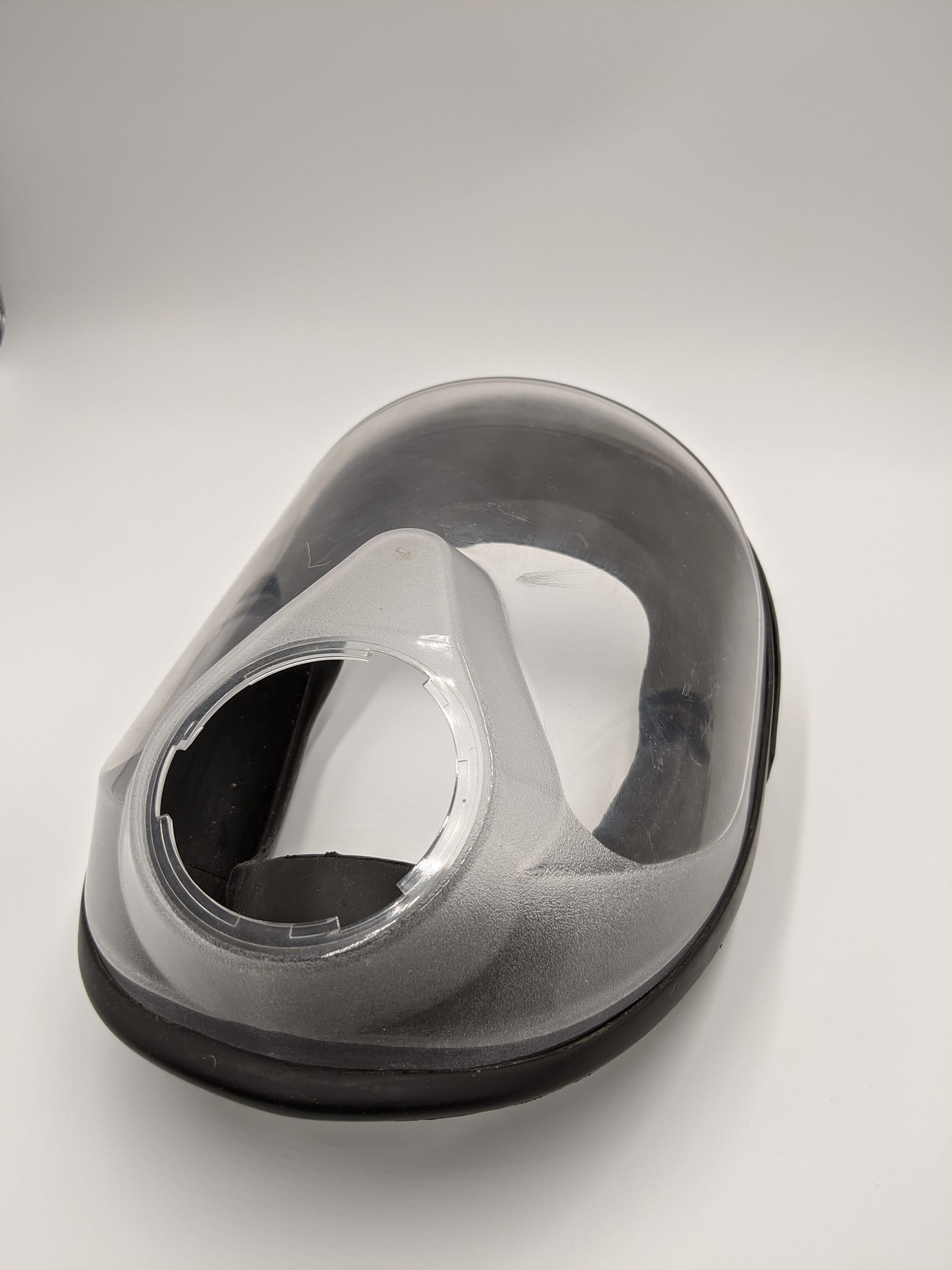
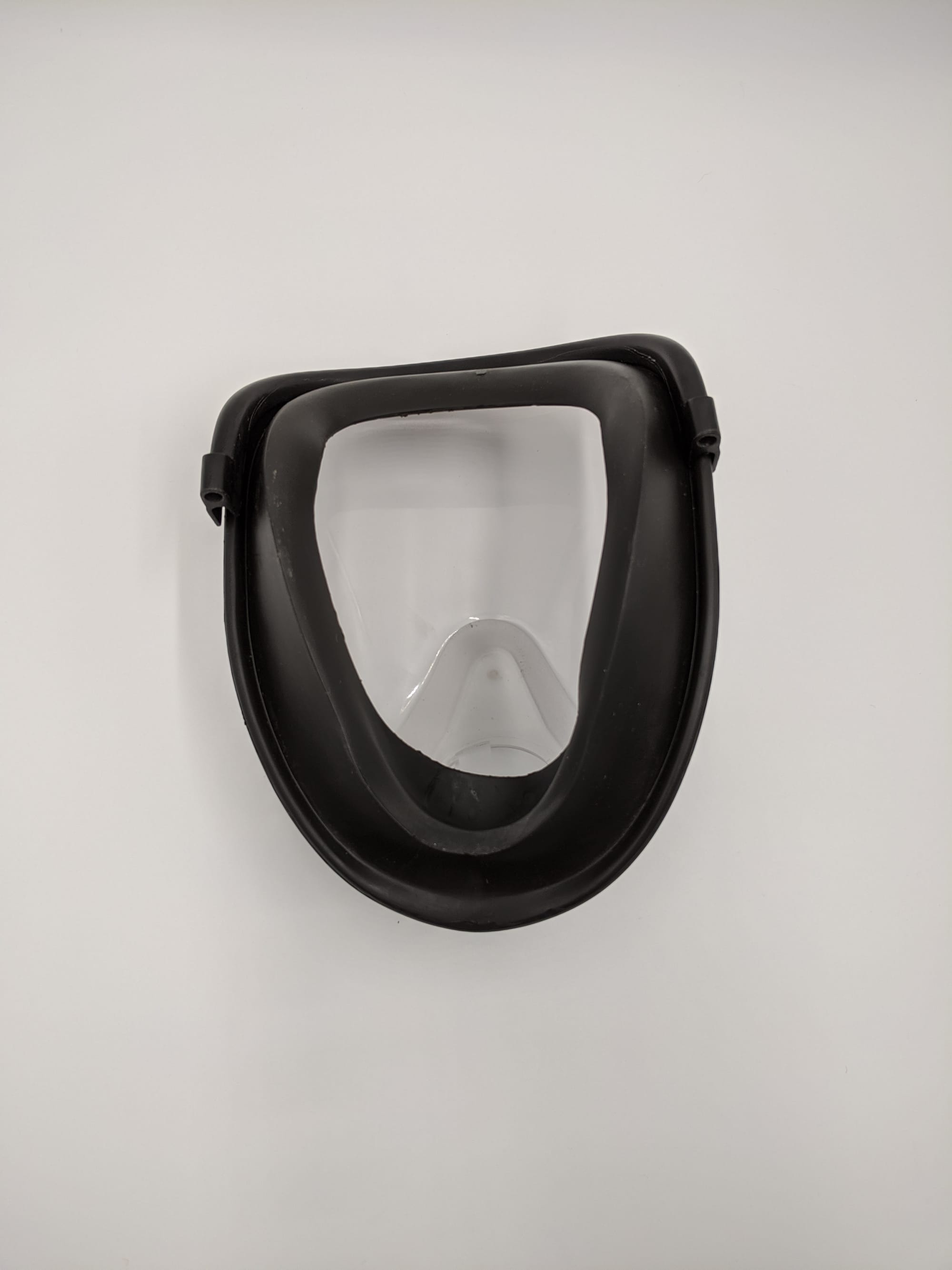
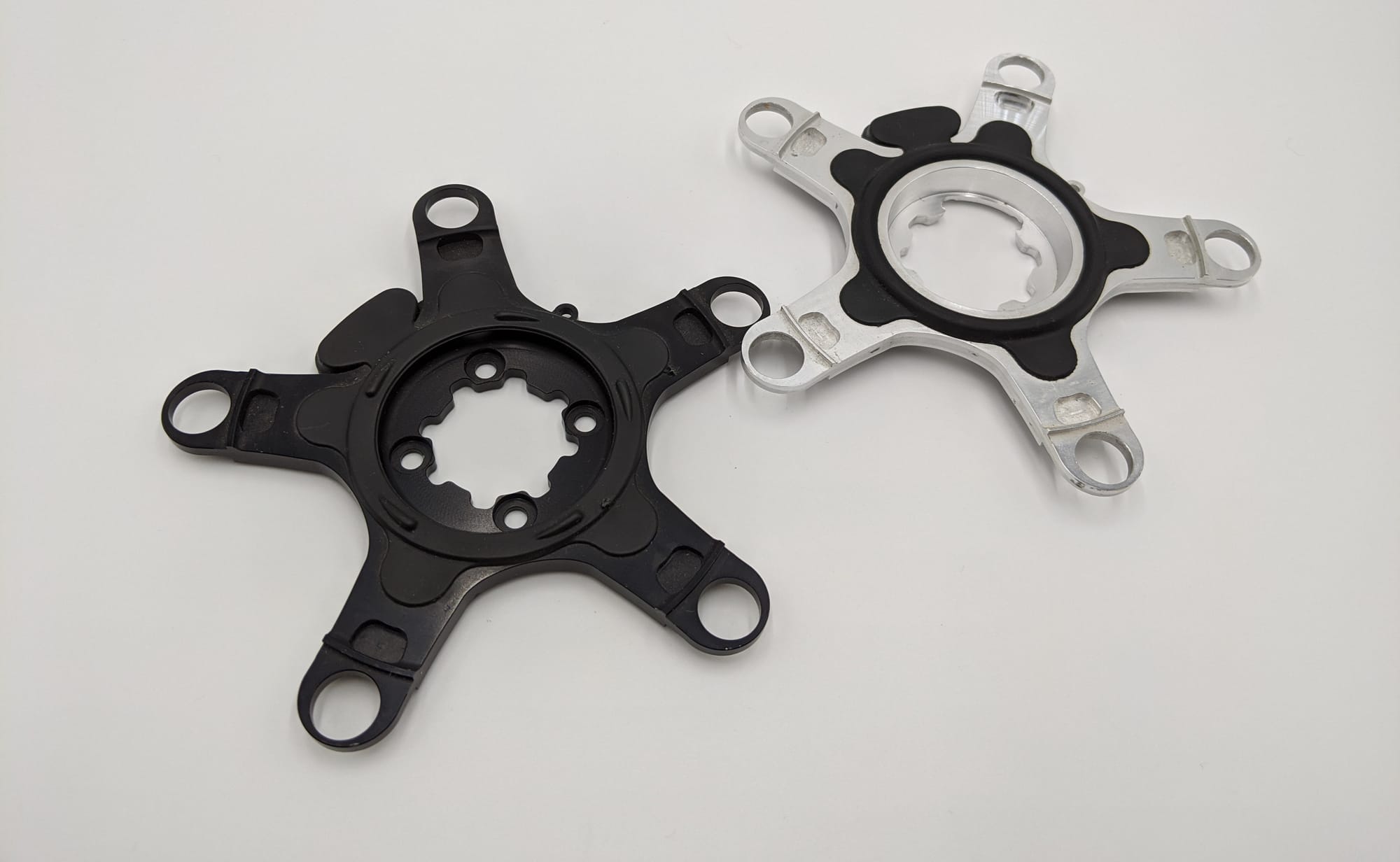
Examples of flexible silicone and urethane parts from my business over the years showing a range of: embedded parts; molds made of silicone (blue); black urethane bumpers; silicone seal for a gas mask; machined aluminum parts with overmolded flexible urethane.
Since 2018, I’ve worked with RTV polymers through my business, Prototyping Tech, serving industries including medical, aerospace, consumer products, electronics, scientific instruments, and more. Most of our work has fallen into two buckets:
- Functional Prototypes – Production identical stand-ins for future injection molded parts, perfect for hands-on testing and marketing.
- Short-Run Production – Economical batches of engineered polymer parts without the high lead time or tooling cost of injection molding or liquid silicone rubber molding.
My medical and aerospace customers often specify the urethane or silicone that their project needs. What keeps me coming back to recommend and use cast resins in new projects is the sheer range of properties, such as:
- UV and chemical resistance
- Very high heat deflection temperature (especially for silicones)
- Flame retardance (often required for aerospace parts)
- Foamed, filled or solid parts
- Biocompatible and food safe materials
- Mechanical properties ranging far beyond what current 3D printing materials can achieve
Furthermore it's possible to embed hardware such as threaded inserts, electronics, LEDs, magnets, and also overmold onto other parts—opening the door to hybrid solutions.
So, you need a flexible part. First give printing a shot.
It's a cheaper, faster place to start, and you'll probably learn some valuable lessons from the parts even if they don't come out perfectly. There are 4 additive manufacturing modalities you could look at to start:
- FDM/Extrusion of thermoplastics: Most likely you'll be using a TPU. For these to print well on FDM extrusion printers, this often requires a material on the hard side of the flexible range at 80A-95A. I haven't personally used foaming TPU's yet, however, there are some printable filaments that can foam during extrusion, giving you a lower density deposition that can effectively make a whole part more flexible.
- SLA/vat photocuring resins: Two resins I've had experience with are the Elastic 50A and Flexible 80A resins (in regular and biomed formulations) from Form Labs. I had much better printability and performance with the harder 80A resins, however, these are both prone to tearing with relatively low stress and at points of frequent flexure.
- PolyJet (Jetted photocuring resins): This is typically a more expensive and precise printing modality. The print head is able to build parts in multiple materials by jetting liquids that cure solid with UV light. A special feature of this form of printing is the ability to mix materials to get a range (even a gradient) of colors, and material properties in the same print!
- Selective Laser Sintering (SLS)/powder bed thermoplastics: These printers melt thermoplastic powder layer by layer with a laser, and don't require the use of support structures. It's possible to find 50A to 90A TPU's printed on this printer with 80A to 90A being most common. The parts come out with a grainy surface finish translated from the powder diameter of the input polymer. Here's a previous post about a D20 dice I designed and printed in SLS Nylon.
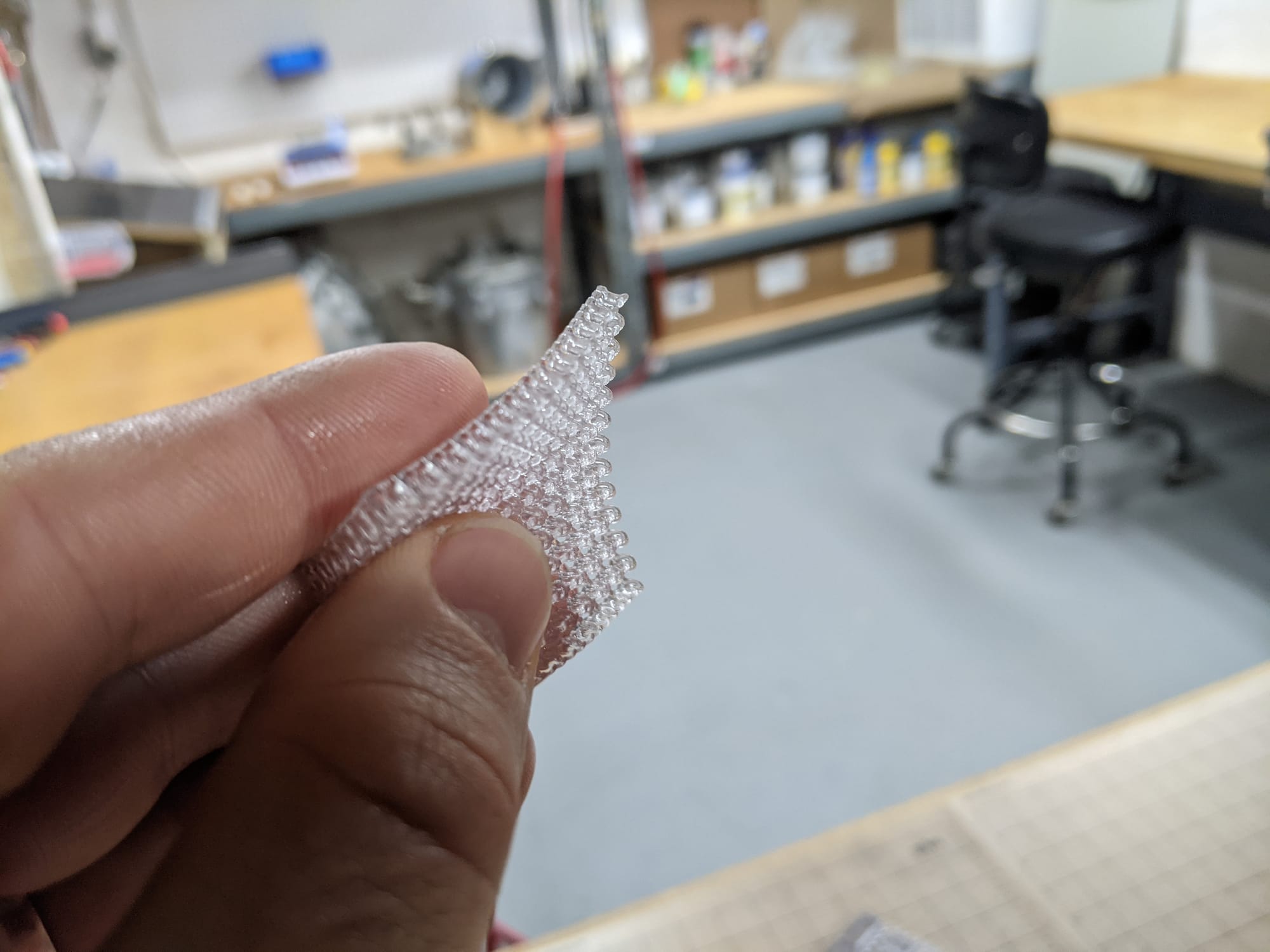
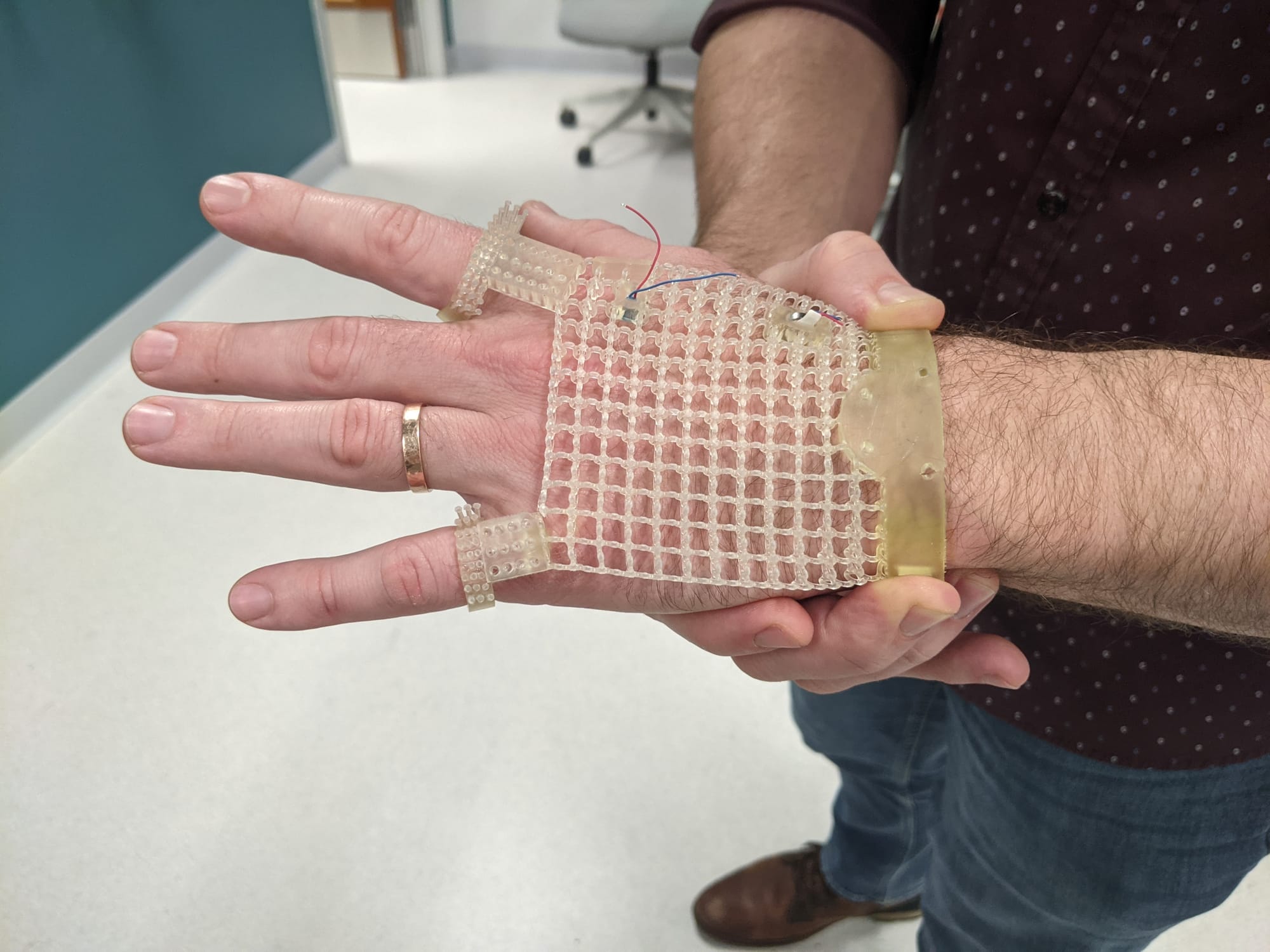
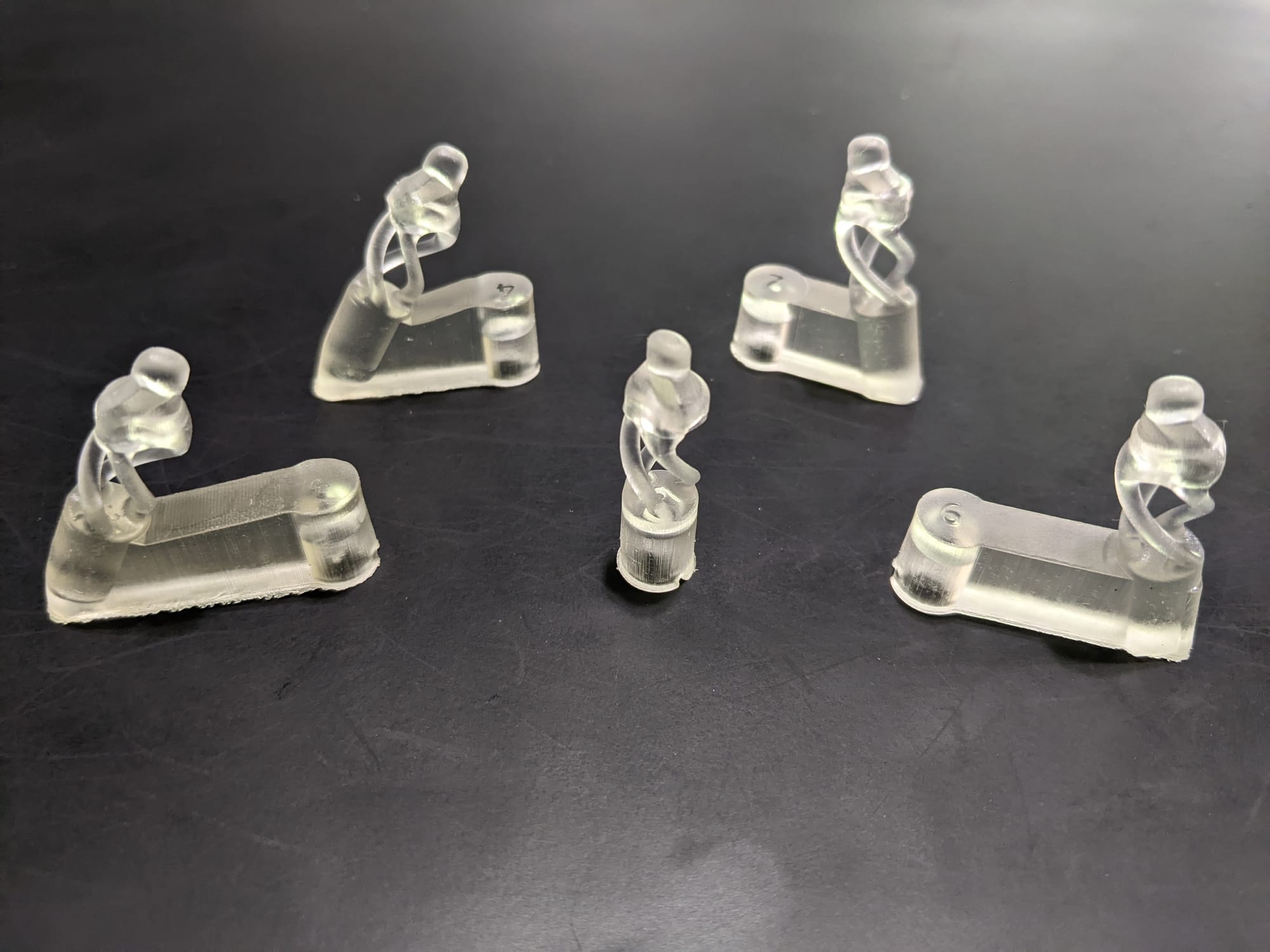
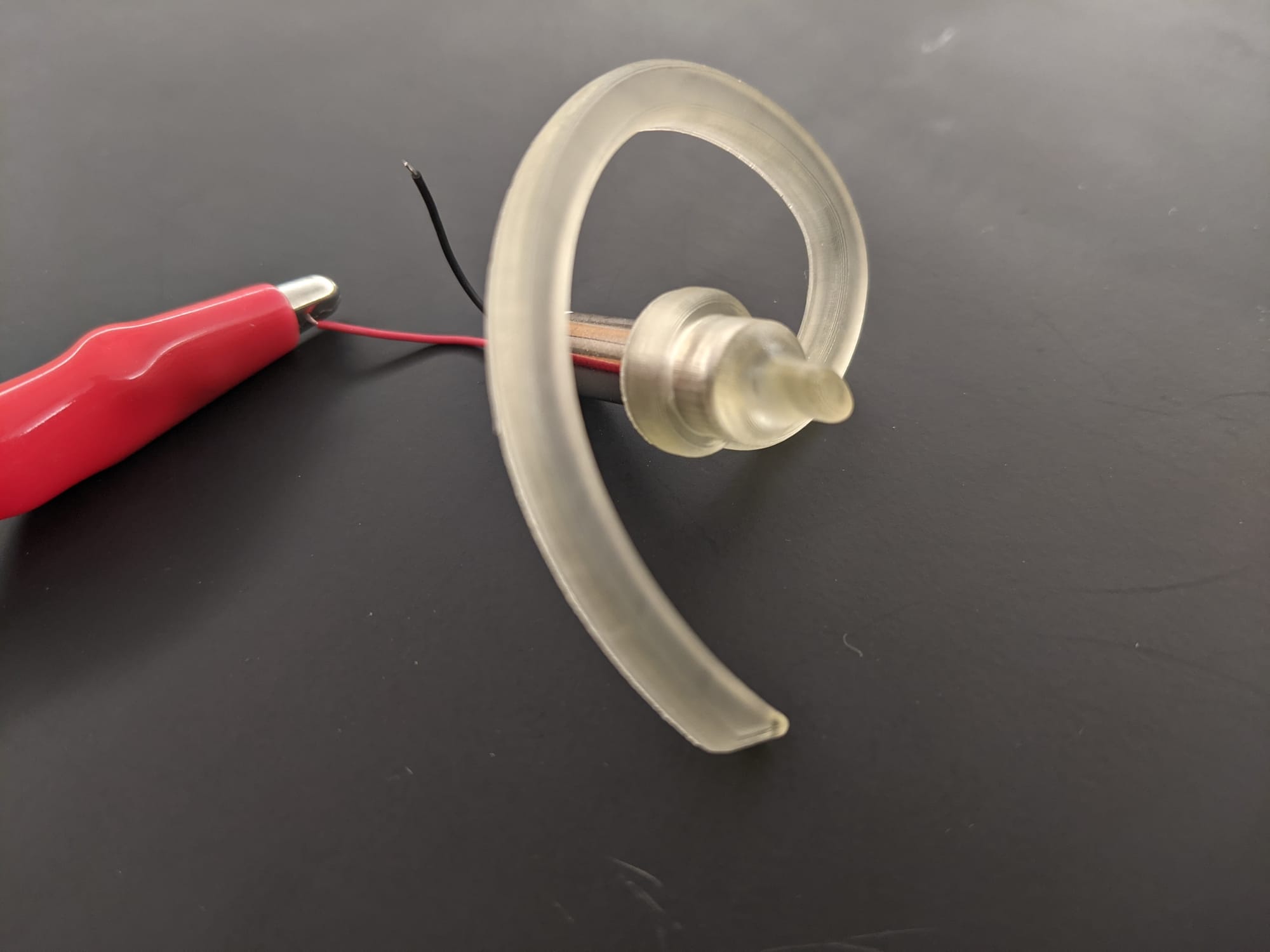
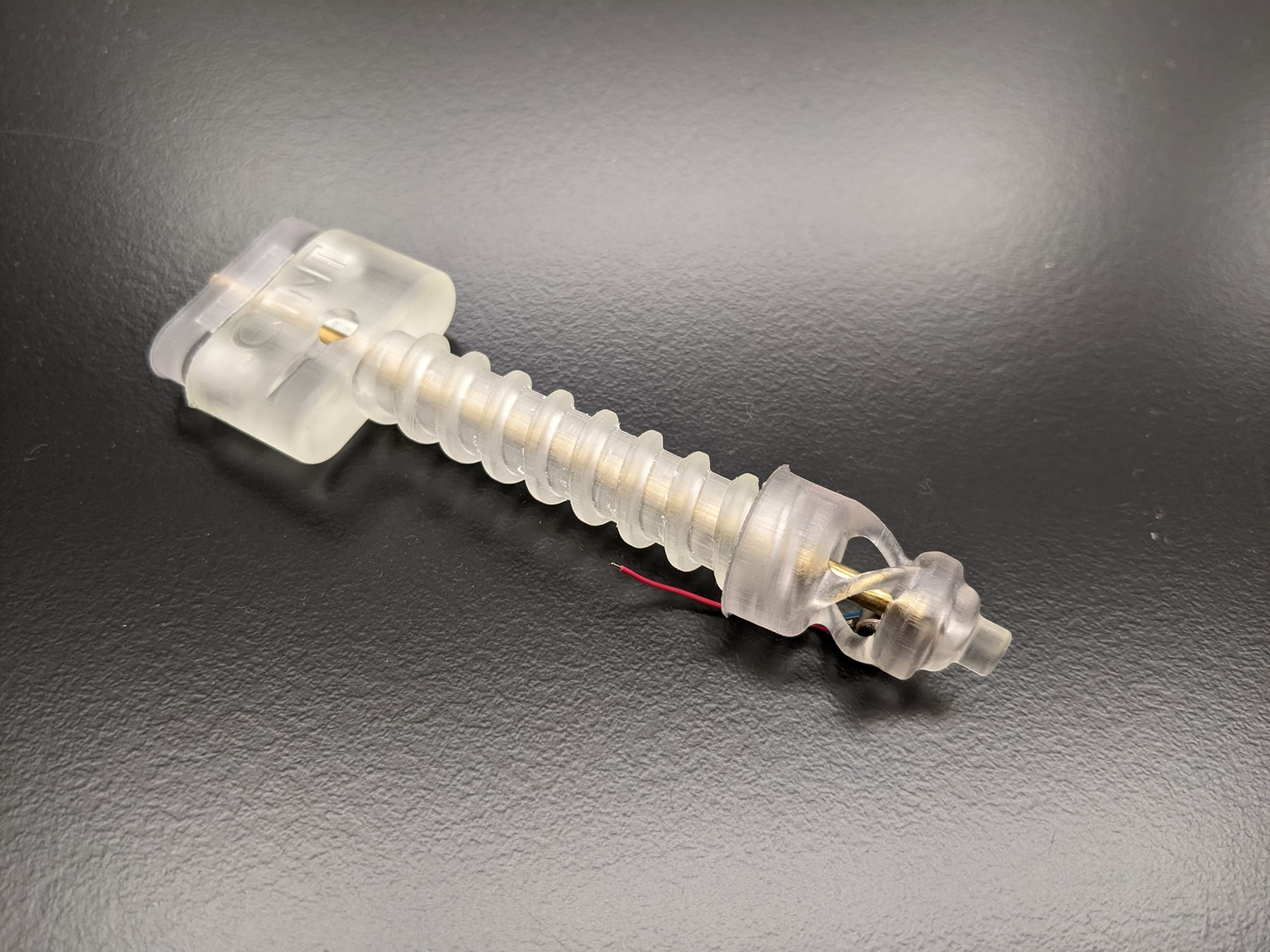
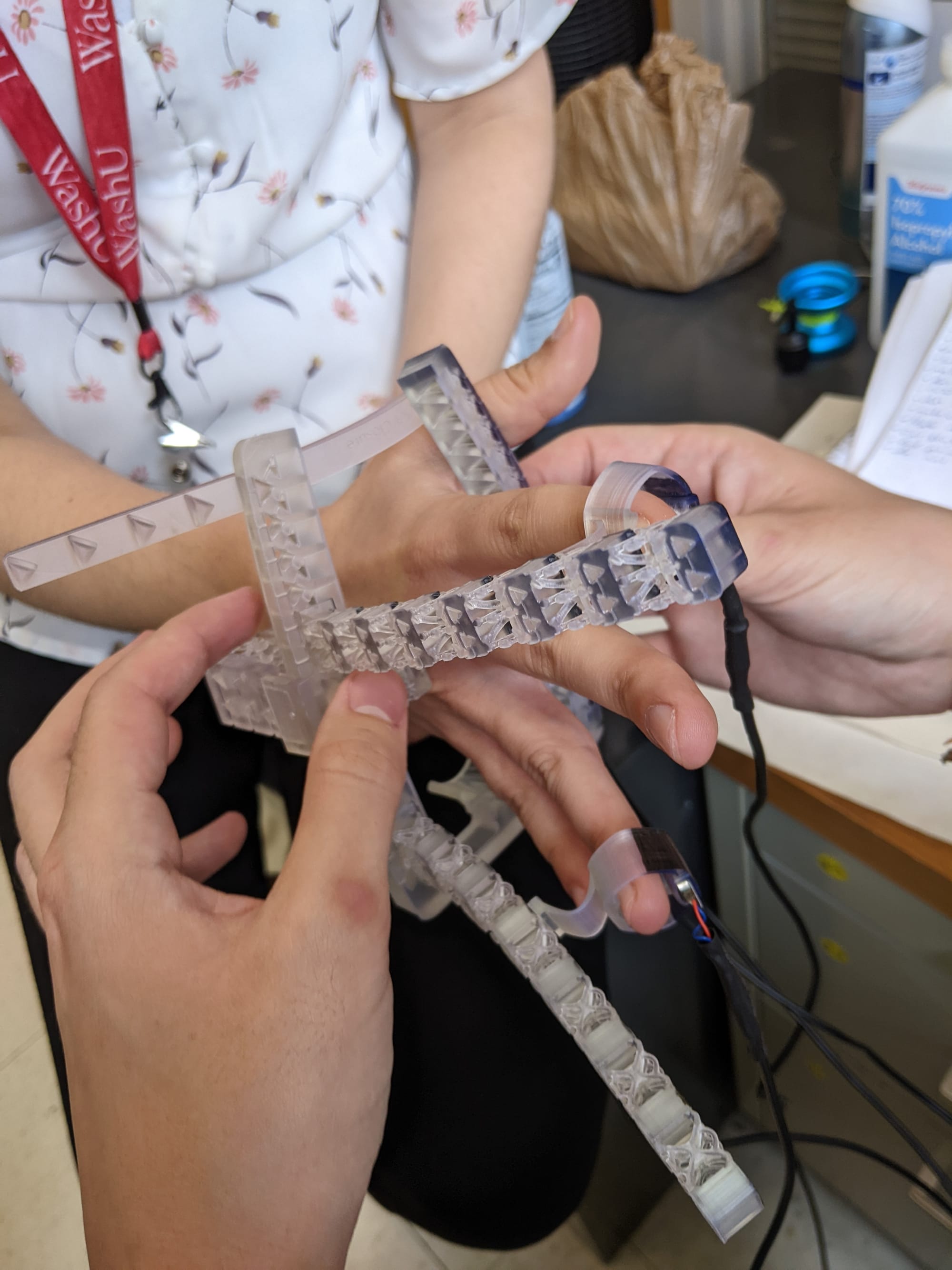
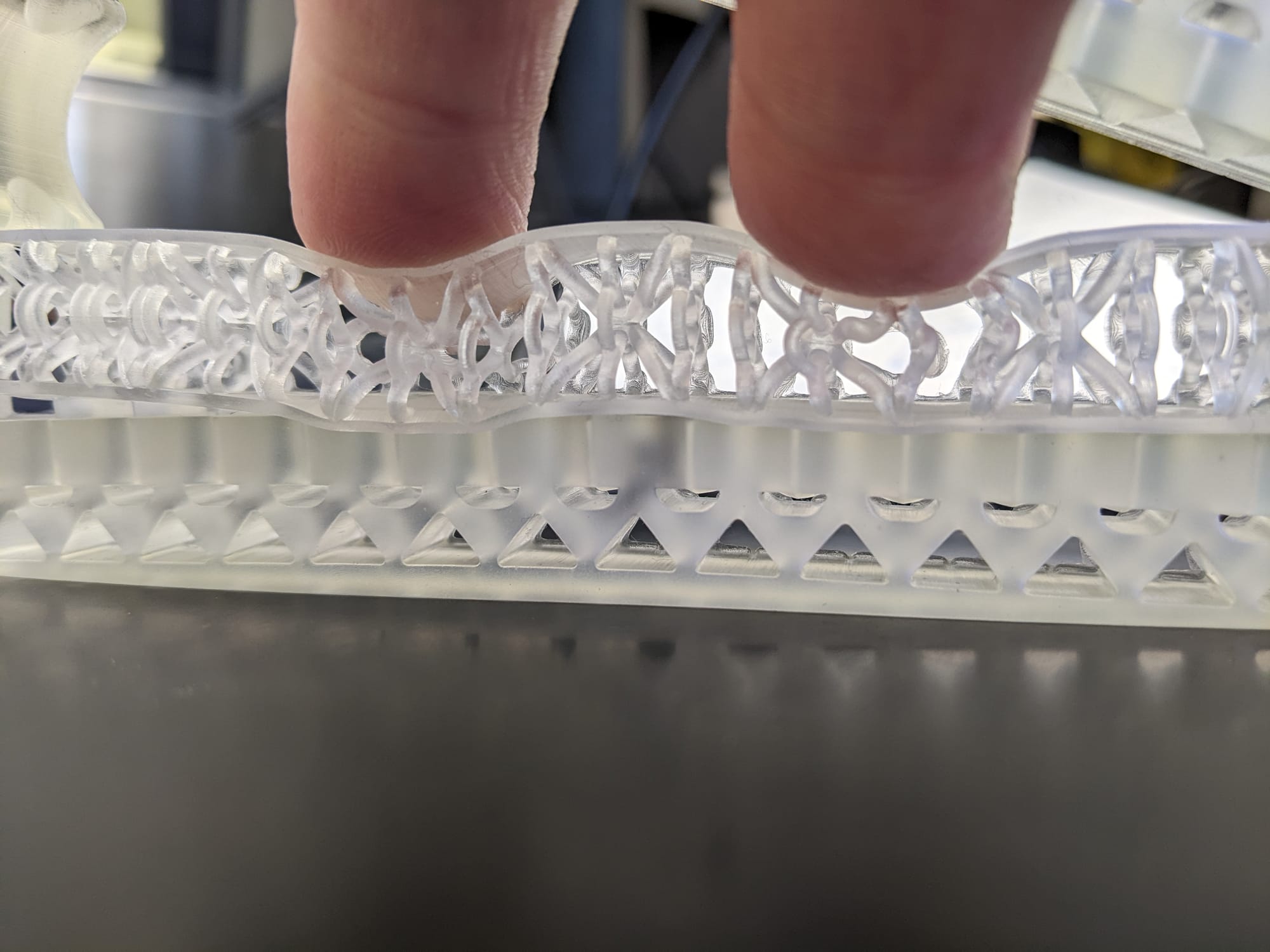
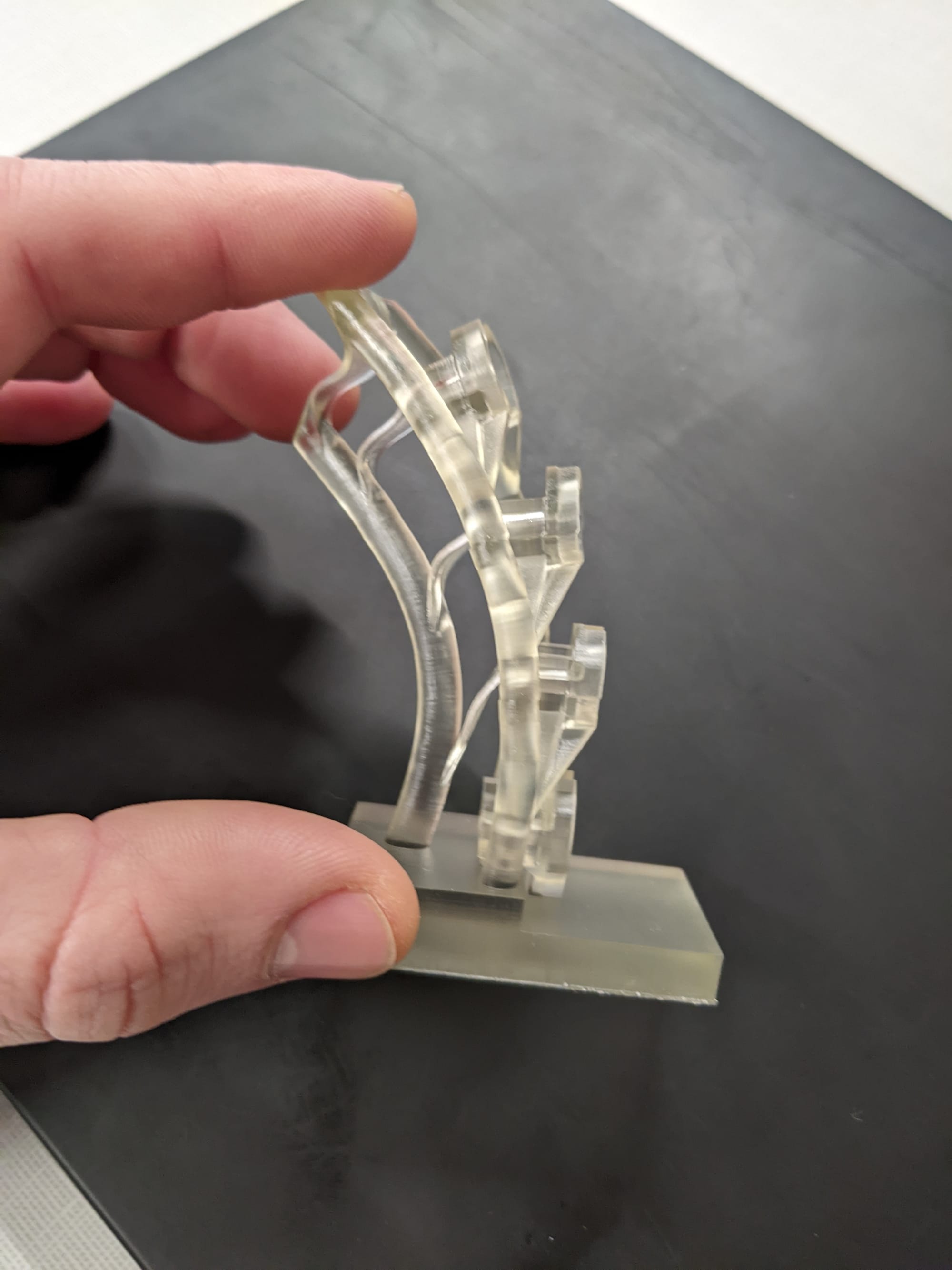
Projects with Flexible lattices, springs and vibration dampening elements printed in 50A and 80A SLA sesins.
Some custom 80A springs in FormLab Flexible Biomed 80A resin.
The two biggest issues I've encountered printing flexible structures are:
- Loss of precision: In larger parts, especially at larger z-heights, precision can become a real issue. This is an issue that's easy to visualize if you imagine building a tall structure out of something that is flexible, there's just more chance for flexing and wiggling to occur during deposition/between layers.
- Issues cleaning up support structures: Especially with the 50A resin, the tear strength is significantly impacted and it can be tough to cleanly trim larger support structures.
If printing isn't a match, check out casting:
Castable Material selection:
There's good chance that if you need a flexible part and printing doesn't meet your needs, it's either that there isn't a soft enough material or a material that's able to handle your requirements for elastic elongation or repeated flexure. This is a good time to turn to casting.
Silicones typically run from the bottom of the Shore OO (softer than marshmallows) up most of the way through the overlapping Shore A scale (up to the hardness of a shoe sole).
Polyurethanes typically run the range of the Shore A scale (about as soft as rubber bands), and well beyond into Shore D (the hardness of bone!)

Here's a link to the BJB Materials guide to shore hardness scales also describing the difference of how these hardness scales are actually measured.
Hardness is a rough approximation of many material properties which has lead to it's wide adoption in the industry. Hardness as measured on the Shore A and Shore D scales are often a common element of material naming conventions. However, beware, not all hardness materials perform the same. For example: a 40A silicone and a 40A polyurethane can perform quite differently in ways that matter to an end application in especially properties like: modulus of elasticity, elongation %, tear strength, and resilience to surface abrasion.
Polyurethanes are often cheaper and easier to work with, however, silicone is hard to outperform (especially platinum cure silicone) when it comes to UV and chemical resistance, elasticity and performance over a wide range of temperatures (often rated for use at -60° C all the way to 250° C). In fact, silicones don't not have a melting point, they remain solid until combustion occurs!
By preparing the surface of your mold and using an appropriate mold release, you are be able to mold the surface finish directly into the part from gloss to texture to pattern.
Tooling
Once the material is selected the tooling can be designed, and the part can be optimized for that specific material's casting properties.
For this offer, I'm here to help you select material, and then design and fabricate the mold for you while offering the relevant design for manufacturing (DFM) analysis of your part for casting and any future manufacturing process such as injection molding.
Factors include:
- Draft angles, undercuts, and parting lines
- Best practices for embedding inserts or electronics
- Tolerances and expected shrinkage
- Thin walls and minimum feature size
If you're needing silicone parts, I'll fabricate your tooling in the resin I worked with 3D Resin Solutions to dial in: Platinum Cure Safe SLA Resin. You are also able to buy this resin on the 3D Resin Solutions website.
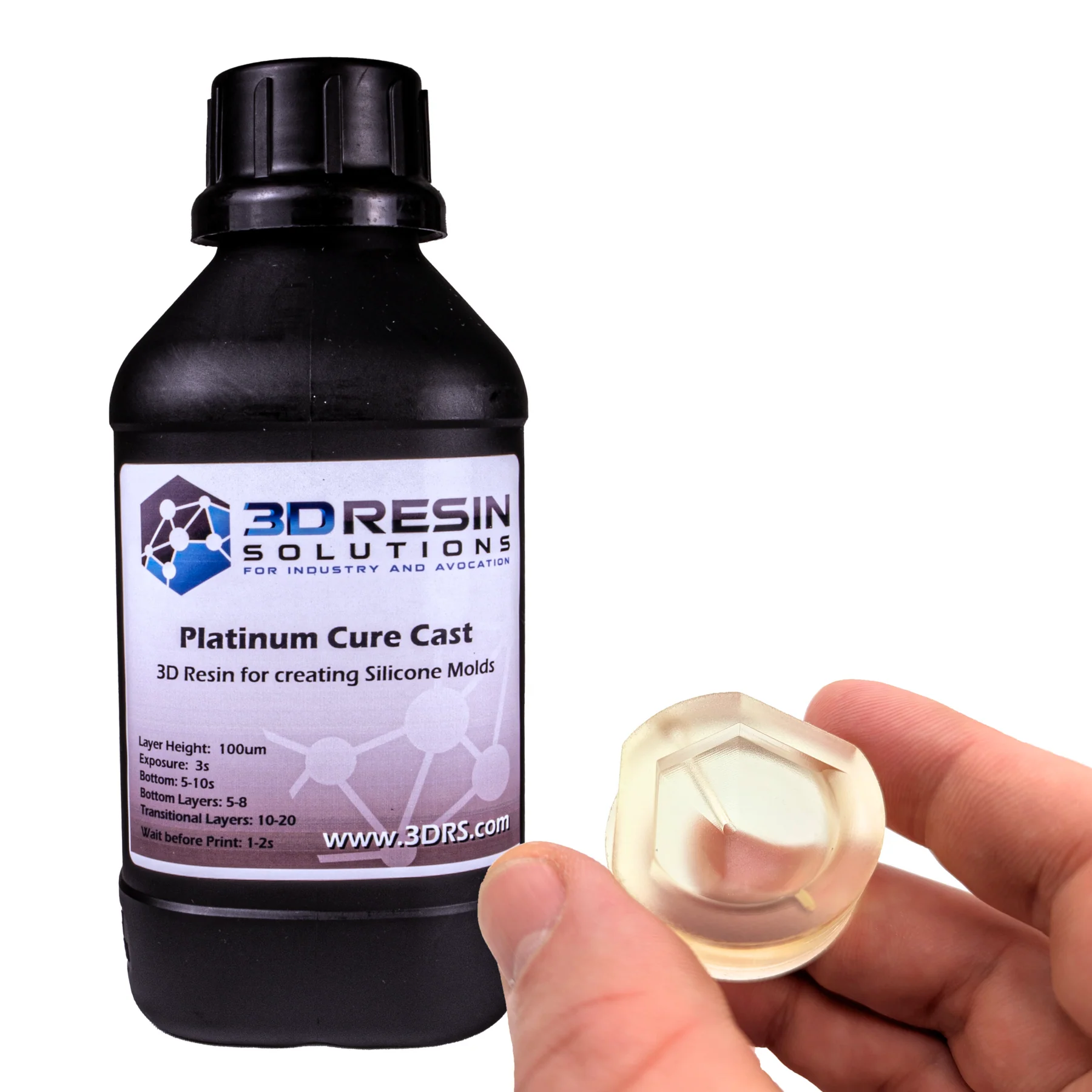
I've never offered tooling through my business before, only finished parts, so this is a special limited time offer. Please reach out to me at Josh@JoshAdams.io if you'd like to discuss a custom mold that you can use in your own workshop!